Chemisch-mechanisches Polieren
Chemisch-mechanisches Polieren, auch chemisch-mechanisches Planarisieren (CMP, engl: chemical mechanical polishing, auch chemical mechanical planarization) ist ein Polierverfahren in der Waferbearbeitung um dünne Schichten gleichmäßig abzutragen.
Geschichte und Motivation
[Bearbeiten | Quelltext bearbeiten]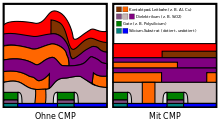
Für die Herstellung von mikroelektronischen Schaltungen werden unter anderem dünne Schichten in mehreren Schritten auf einem sehr ebenen und glatten Wafer aufgetragen und strukturiert. Wie in Abb. 1 illustriert, entstehen dabei nach einigen Schichten starke Unebenheiten, die zum Abreißen einer höher gelegenen Schicht führen können und so Mehrschichtsysteme schwer realisierbar werden lassen. Dieses Problem verstärkt sich bei zunehmender Komplexität der Schaltungen, da hier mehr Metallisierungsebenen für die Bauelementverdrahtung benötigt werden. Ein weiterer Punkt ist die negative Beeinflussung der fotolithografische Strukturierung durch eine unebene Oberfläche. Eine genaue Abbildung ist nur auf planaren Oberflächen möglich und die Anforderungen an die fotolithografische Strukturierung steigen zusätzlich mit jedem Technologieknoten, bei dem die zu fertigenden Strukturen stetig verkleinert werden.
Schon sehr früh wurden in der Halbleitertechnik Verfahren zur Einebnung angewendet, wie zum Beispiel der „BPSG-Reflow-Prozess“[1] bei dem eine Schicht aus Borphosphorsilicatglas (BPSG) aufgebracht und angeschmolzen wurde. Die erzielte Planarität dieser Verfahren reichten aber Anfang der 1990er Jahre nicht mehr aus, so dass bereits zuvor nach alternativen Verfahren gesucht wurde.
Das Polieren von Glas ist eine seit Jahrhunderten praktizierte Technik. Das chemisch-mechanische Polieren wurde für den Einsatz in der Halbleitertechnik zum ersten Mal Anfang/Mitte der 1980er Jahre vorgeschlagen.[2][3] Damals wie heute waren Siliciumdioxidschichten und deren Einebnung ein wichtiger Aspekt in der Halbleitertechnik. In den letzten 20 Jahren hat sich CMP in der Halbleitertechnik zu einem Standardverfahren und Schlüsseltechnologie entwickelt. Der Vorteil des CMP ist im Wesentlichen die „Einfachheit“ des Grundprinzips, das prinzipiell mit allen Materialien funktioniert: Nach dem Auftragen einer Schicht wird diese zurückpoliert und Unebenheiten werden so ausgeglichen. Anschließend hat man eine glatte, ebene Unterlage, auf der man Fotolacke auftragen und präzise belichten kann.
Funktionsprinzip
[Bearbeiten | Quelltext bearbeiten]
Der zu polierende Wafer wird von dem Waferträger (Carrier) aufgenommen und mit einem definierten Druck auf den Polierteller mit dem Poliertuch gepresst. Währenddessen beginnen sich Waferträger und Poliertuch in dieselbe Richtung zu drehen (es ist auch eine ungleichsinnige Drehrichtung möglich). Hier gibt es verschiedenste Möglichkeiten, die Geschwindigkeiten zu variieren oder den Waferträger in eine oszillierende Bewegung zu versetzen, um so den Abtrag und dessen Gleichmäßigkeit zu optimieren.
Das Poliertuch besteht zumeist aus Polyurethan-Schäumen oder mit Polyurethan behandeltem Vliesstoff. Man hat hier die Möglichkeit, zwischen unterschiedlichen Härten und Perforationen zu wählen.
Während des gesamten Poliervorgangs wird über ein Pumpensystem eine kolloidiale Poliermittel-Suspension (Slurry), bei der Grabenisolation beispielsweise 30 bis 200 nm große Siliciumdioxid-, Cer(IV)-oxid- oder Aluminiumoxid-Partikel, auf den inneren Bereich des Poliertuches geleitet, das sich durch die Rotationsbewegung über das Poliertuch verteilt. So entsteht zwischen Wafer und Poliertuch ein dünner Poliermittelfilm, der die zu polierenden Schichten chemisch angreift, mit den in ihm enthaltenen Abrasivpartikeln für eine mechanische Bearbeitung der Oberfläche sorgt und so das Material abträgt.
Das Polierergebnis hängt wesentlich von einer gleichmäßigen Druckverteilung ab. Daher haben beispielsweise die Dichte der Strukturen auf dem Wafer sowie die Planarität des „Chucks“ und des Poliertellers Einfluss auf die Politur, denn jede Unebenheit und Verformung hat eine Änderung der Druckverhältnisse auf dem Wafer zur Folge und kann daher das Ergebnis verschlechtern (Inhomogenität). Daher ist die Unterseite des Chucks mit einem Backing-Film beklebt, dessen weiche Faser Unebenheiten ausgleicht und mittels Adhäsion die Rotation des Chucks auf den Wafer überträgt.
Nach einer definierten Zeit wird der Wafer vom Poliertuch genommen und (innerhalb der CMP-Maschine) einer ersten Vorreinigung mit Reinstwasser unterzogen. Die restlose Entfernung des Poliermittels beugt möglicher Kristall- und Kratzerbildung vor und unterbindet die fortlaufende Ätzung der Waferoberfläche.

Währenddessen beginnt der Konditionierer das Poliertuch für den nächsten Wafer vorzubereiten (Ex-situ-Konditionierung). Dies geschieht, indem eine rotierende mit Diamanten besetzte Scheibe unter Zugabe von deionisiertem Wasser über das sich ebenfalls drehende Poliertuch gefahren wird, es auf diese Weise anrauht und die Poren im Poliertuch von Poliermittelresten und Material der Waferschichten befreit. Dieser Arbeitsschritt kann einmal oder mehrmals nach dem Polieren stattfinden, aber auch während des Polierens gefahren werden. Im letzteren Fall spricht man von In-situ-Konditionierung. Für welche Art der Konditionierung man sich entscheidet, hängt stark vom Prozess ab.
Literatur
[Bearbeiten | Quelltext bearbeiten]- Y. Li (Hrsg.): Microelectronic Applications of Chemical Mechanical Planarization. Wiley-Interscience, Hoboken, NJ 2008.
- H. Liang, D. Craven: Tribology in Chemical Mechanical Planarization. CRC Press, Boca Raton, FL, 2005.
- J. M. Steigerwald (Hrsg.): Chemical Mechanical Planarization of Microelectronic Materials. John Wiley & Sons, Inc., New York 1997, S. 181 ff.
Einzelnachweise
[Bearbeiten | Quelltext bearbeiten]- ↑ Ulrich Hilleringmann: Silizium-Halbleitertechnologie. Vieweg+Teubner Verlag, 2008, ISBN 978-3-8351-0245-3, S. 153 ff.
- ↑ K. D. Beyer: A “Dirty” Risk. In: Innovative Leader. Volume 8, Nr. 6, 1999, S. 407 (HTML, abgerufen am 12. April 2010).
- ↑ M. A. Fury: The early days of CMP. In: Solid State Technology. Band 40, Nr. 4, 1997, S. 81–88 (HTML-Version [abgerufen am 13. April 2010]).