Schnellarbeitsstahl

Schnellarbeitsstahl ist ein hochlegierter Werkzeugstahl, der hauptsächlich als Schneidstoff genutzt wird, also für Fräswerkzeuge, Bohrer, Drehmeißel und Räumwerkzeuge. Die Bezeichnung bezieht sich auf die gegenüber gewöhnlichem Werkzeugstahl drei- bis viermal höheren Schnittgeschwindigkeiten. Während gewöhnlicher Werkzeugstahl bereits ab etwa 200 °C seine Härte verliert, behält Schnellarbeitsstahl bis etwa 600 °C seine Härte. Die gebräuchlichen Kurzbezeichnungen beginnen mit HSS oder HS, abgeleitet vom englischen High Speed Steel. Deutsche Bezeichnungen sind Hochgeschwindigkeitsstahl, (Hochleistungs-)Schnellschnittstahl, Hochleistungsschnellarbeitsstahl und Hochleistungsschnittstahl.
Die Bezeichnungen AHSS und HSS sind nicht unmittelbar verwandt, obwohl es sich in beiden Fällen um Werkzeugstähle handelt. AHSS steht für Advanced High Strength Steel (Deutsch etwa: Weiterentwickelter hochfester Stahl) und bezeichnet moderne hochfeste unlegierte Kaltarbeitsstähle.[1]
Schnellarbeitsstahl verdrängte bei Zerspanungswerkzeugen nach seiner Entwicklung 1906 sehr rasch den gewöhnlichen Werkzeugstahl (Kaltarbeitsstahl) und hat diesen dort inzwischen fast vollständig ersetzt.
Von allen in der modernen, industriellen Zerspantechnik genutzten Schneidstoffen wie u. a. Hartmetall, Cermets oder Bornitrid, verfügt Schnellarbeitsstahl zwar über die höchste Bruchfestigkeit und beste Schleifbarkeit, aber die geringste Warmhärte und Verschleißfestigkeit, sodass mit anderen Schneidstoffen noch höhere Schnittgeschwindigkeiten möglich sind.
Die wichtigsten Legierungselemente sind Kohlenstoff, Wolfram, Molybdän, Vanadium, Chrom und Cobalt, deren Anteil bis über 30 % ausmachen kann. Seine Härte erhält Schnellarbeitsstahl, wie alle anderen Werkzeugstähle auch, durch sein martensitisches Grundgefüge, das aus Eisen und Kohlenstoff besteht. Die übrigen Legierungselemente sorgen für eine bessere Verschleißbeständigkeit und für die Beständigkeit des Martensits bis zu Temperaturen von 600 °C. Die hohe Warmhärte und hohe Wärmefestigkeit gegenüber gewöhnlichem Werkzeugstahl beruht auf der Wärmebehandlung: Zunächst wird der Schnellarbeitsstahl bei über 1200 °C geglüht und danach abgeschreckt, um das martensitische Grundgefüge zu erzeugen. Anschließend folgt mehrmaliges Anlassen bei etwa 550 °C, bei dem die Sprödigkeit zurückgeht und aus dem Martensit winzige Carbide (Wolfram-/Molybdän-/Vanadium-Kohlenstoff-Verbindungen) ausscheiden, die für die Warmhärte und Wärmefestigkeit verantwortlich sind.
Anwendungen, Vergleich mit gewöhnlichem Werkzeugstahl und anderen Schneidstoffen[Bearbeiten | Quelltext bearbeiten]
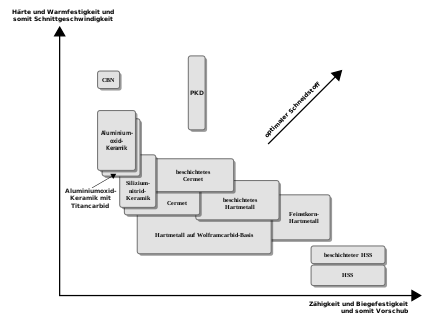
Aus Schnellarbeitsstahl werden verschiedene Zerspanungswerkzeuge hergestellt. Darunter sind Drehmeißel, Fräswerkzeuge, Bohrer und Räumwerkzeuge. Die letzten beiden bestehen besonders häufig aus Schnellarbeitsstahl; für Drehmeißel und Fräswerkzeuge sind andere Schneidstoffe weiter verbreitet, vor allem das Hartmetall, das von allen Schneidstoffen dem Schnellarbeitsstahl am ähnlichsten ist. HSS-Werkzeuge werden bei komplizierteren Werkzeugformen wie bei Profilwerkzeugen bevorzugt, da sie sich sehr gut schleifen lassen. Gewöhnlicher Werkzeugstahl (Kaltarbeitsstahl) wird nur noch bei Werkzeugen angewandt, die keine hohen Schnittgeschwindigkeiten erreichen können wie Feilen und Raspeln, sowie bei Werkzeugen für die Holzbearbeitung. Ansonsten wurde Kaltarbeitsstahl in der Zerspantechnik vollständig von Schnellarbeitsstahl verdrängt. Vorteile der HSS-Werkzeuge gegenüber Hartmetall-Werkzeugen liegen im niedrigeren Preis, der guten Schleifbarkeit, die komplizierte Werkzeugformen ermöglicht und auch das Nachschleifen stumpfer Werkzeuge erlaubt, sowie in der höheren Festigkeit: HSS-Werkzeuge sind weniger bruchempfindlich bei stoßartiger Belastung.
Kaltarbeitsstahl verliert bereits bei Temperaturen ab 200 °C seine Härte und wird somit als Schneidstoff unbrauchbar. Der Effekt begrenzt die Schnittgeschwindigkeit bei der Bearbeitung von Stahl auf etwa 5 m/min. Schnellarbeitsstahl behält seine Härte bis etwa 600 °C, was Schnittgeschwindigkeiten bis etwa 80 m/min erlaubt. Werkzeuge aus Hartmetall, Schneidkeramiken und Bornitrid eignen sich für Temperaturen von über 1000 °C. In der industriellen Praxis wird die Schnittgeschwindigkeit nicht mehr durch die Temperatur begrenzt, sondern durch den Verschleiß. HSS-Werkzeuge können beschichtet werden mit Titannitrid und anderen Stoffen, die die Verschleißfestigkeit erhöhen, was vor allem die Standzeit der Werkzeuge erhöht und etwas höhere Schnittgeschwindigkeiten erlaubt.[2][3]
Geschichte[Bearbeiten | Quelltext bearbeiten]
Nachdem Ende des 19. Jahrhunderts der Bedarf nach einem Schneidstoff, der höhere Schnittgeschwindigkeiten als Werkzeugstahl ermöglicht, immer größer wurde, entwickelten Taylor und White bis 1906 den Schnellarbeitsstahl, der sich rasch durchsetzte. Ab den 1930ern und verstärkt seit den 1960er Jahren wurde der seinerseits durch das Hartmetall und andere Schneidstoffe verdrängt, aber nie vollständig ersetzt. Die genauen metallurgischen Zusammenhänge zur Erklärung der hohen Warmhärte von Schnellarbeitsstahl konnten erst Mitte des 20. Jahrhunderts geklärt werden.[4]
Ausgangssituation[Bearbeiten | Quelltext bearbeiten]
Im Laufe der industriellen Revolution wurden immer häufiger Werkstücke aus Stahl zerspant, während zuvor vorwiegend Holz und weichere Metalle wie Kupfer und Zinn bearbeitet wurden. Stahl ist wesentlich fester als diese Werkstoffe und führte zu viel höherem Verschleiß der Werkzeuge, die aus gewöhnlichem Werkzeugstahl bestanden, sodass die wirtschaftlich sinnvollen Schnittgeschwindigkeiten bei nur 5 m/min lagen. Werkzeugstahl war seit langem bekannt, bestand nur aus Eisen und Kohlenstoff und konnte bereits bei 750 °C bis 835 °C gehärtet werden, verlor aber seine Härte bereits ab etwa 200 °C. Die erste Verbesserung gelang 1868 Robert Mushet mit einem Werkzeugstahl, der mit 6 bis 10 % Wolfram, 1,2 bis 2 % Mangan und 0,5 % Chrom legiert war. Zum Härten konnte er an Luft gekühlt werden statt im Wasserbad, was als Selbsthärtung bezeichnet wurde. Bei der Härtung im Wasser kam es immer wieder zu Brüchen der Werkstücke. Mit Mushets Werkzeugstahl konnten Schnittgeschwindigkeiten bis 7 m/min erreicht werden.[5]
In den 1860ern wurde es mit Entwicklung des Siemens-Martin-Verfahrens und des Bessemer-Verfahrens möglich, Temperaturen von über 1800 °C zu erzeugen. Damit wurde es zum ersten Mal in der Geschichte möglich, Stahl zu schmelzen, was seinen Reinheitsgrad verbesserte. Bei noch höheren Temperaturen schmelzende Metalle wie Wolfram (über 3300 °C) konnten mit der damals neuen Elektrochemie erzeugt werden, sodass sie als Legierungselemente zur Verfügung standen. Zu wirtschaftlichen Kosten waren sie erst zur Jahrhundertwende verfügbar nach dem Ausbau der elektrischen Energieversorgung.
Entwicklung durch Taylor und White[Bearbeiten | Quelltext bearbeiten]
Um die Jahrhundertwende begann der amerikanische Ingenieur Frederick Winslow Taylor nach Möglichkeiten zu suchen, die Produktion wirtschaftlicher zu gestalten. Er entwickelte daraus unter anderem Organisationsprinzipien, die als Taylorismus oder Scientific Management bekannt sind. Er erforschte auch etwa 10 Jahre lang die Zerspantechnik und schrieb 1906 sein Buch On the Art of Cutting Metals (wörtlich: Über die Kunst/Technik Metall zu schneiden), in dem er erstmals allgemeine Zusammenhänge der Zerspantechnik erläuterte, darunter auch die nach ihm benannte Taylor-Gerade, die einen Zusammenhang angibt zwischen Standzeit der Werkzeuge und der Schnittgeschwindigkeit sowie Zusammenhänge zwischen der Werkzeuggeometrie, dem Vorschub, der Schnitttiefe und Kühlschmierstoffen. Gemeinsam mit dem Metallurgen Maunsel White ermittelte er in standardisierten Versuchen für verschiedene Werkzeug-Werkstoffe diejenigen Schnittgeschwindigkeiten, die zu einer Standzeit von 20 Minuten führten. Danach wandten sie sich der Wärmebehandlung und Zusammensetzung der Werkzeuge zu. Sie variierten für verschiedene chemische Zusammensetzungen jeweils die Höhe der Glühtemperatur, die bis zur Schmelztemperatur reichen konnte, sowie die Höhe der Temperaturen, bei der sie anschließend durch Anlassen weiterbehandelt wurden und bestimmten danach die Schnittgeschwindigkeiten für die 20-Minuten-Standzeit. 1906 lag die beste bekannte Zusammensetzung bei 0,67 % C, 18,91 % W, 5,47 % Cr, 0,11 % Mn, 0,29 % V und Eisen als Rest. Die günstigste Wärmebehandlung lag bei Glühen bei 1250–1290 °C, also knapp unter der Solidustemperatur, bei der das Material zu schmelzen beginnt, anschließendem Abschrecken in flüssigem Blei (620 °C) und dann weiteres Abkühlen auf Raumtemperatur. Danach wurden sie bei knapp unter 600 °C angelassen. Die Werkzeuge behielten bis etwa 600 °C ihre Härte und ermöglichten bei der Zerspanung von Stahl Schnittgeschwindigkeiten bis 30 m/min. Diesen Schnellarbeitsstahl stellte Taylor auf der Weltausstellung von 1906[6] der Öffentlichkeit vor.[7]
Erforschung[Bearbeiten | Quelltext bearbeiten]
Taylor und White war klar, dass sie einen vollkommen neuen Mechanismus zur Härtung von Stahl entdeckt hatten, die genaue Funktion konnte jedoch erst in den 1950ern geklärt werden durch den Einsatz von Elektronenmikroskopen. Beim Anlassen scheiden zwischen 400 °C und 600 °C winzige Partikel aus dem Grundgefüge aus, die Durchmesser von nur 0,05 µm haben und somit unter gewöhnlichen, optischen Mikroskopen nicht sichtbar sind. Schnellarbeitsstähle waren somit die ersten Werkstoffe, die durch Ausscheidungshärtung behandelt wurden, und waren damit den Aluminiumlegierungen, die heute für diesen Härtemechanismus bekannt sind, um etwa 10 Jahre voraus.[8]
Verbreitung[Bearbeiten | Quelltext bearbeiten]
Nach der Weltausstellung von 1906 war Taylor ein weltberühmter Mann. Er demonstrierte dort das Drehen von Stahl bei Schnittgeschwindigkeiten, die so hoch waren, dass die Schneiden seiner Werkzeuge rot zu glühen begannen und dennoch nicht versagten. Schätzungen zufolge wurden allein in den USA in den nächsten Jahren HSS-Werkzeuge im Wert von insgesamt 20 Millionen Dollar verkauft, was dank der höheren Schnittgeschwindigkeiten zu Produktionssteigerungen im Wert von 8 Milliarden Dollar führte. Die damaligen Werkzeugmaschinen waren jedoch nicht auf die hohen Belastungen ausgelegt. In Versuchen der damals berühmten, deutschen Firma Ludwig Loewe waren die Maschinen nach wenigen Wochen vollkommen unbrauchbar. In Europa wurde der Schnellarbeitsstahl zunächst bei gewöhnlichen Schnittgeschwindigkeiten genutzt, wo er zu deutlich höheren Standzeiten führte als bei Nutzung von Werkzeugstahl. Die Maschinenhersteller boten zwar bald Maschinen an, die auf die höheren Schnittgeschwindigkeiten ausgelegt waren; da die alten jedoch bei sachgemäßem Umgang sehr langlebig waren, verlief die Umstellung zunächst schleppend. Erst als in den 1920ern eine neue Generation angeboten wurde, die auch über elektrische Antriebe und Steuerungen verfügte statt der bislang gebräuchlichen mechanischen Steuerungen und Antriebe mit Dampfmaschinen, wurden die hohen möglichen Schnittgeschwindigkeiten ausgeschöpft.[9]
In den 1930er Jahren wurde das Hartmetall als neuer Schneidstoff entwickelt, mit dem etwa dreimal höhere Schnittgeschwindigkeiten möglich waren als mit HSS. Die Nutzung verlief zunächst schleppend aus Kostengründen und weil die Maschinen abermals nicht auf die noch höheren Belastungen ausgelegt waren. Ab den 1960ern wurde Hartmetall zum industriellen Standard, konnte den Schnellarbeitsstahl aber ebenso wenig vollständig verdrängen wie die später entwickelten Schneidkeramiken, Bornitrid- und Diamant-Werkzeuge. Bis zum 21. Jahrhundert wurde Schnellarbeitsstahl noch weiter verbessert, die Steigerungen bei der Schnittgeschwindigkeit fallen jedoch gering aus. Mit wesentlichen Verbesserungen wird nicht gerechnet.
Gefüge und Zusammensetzungen[Bearbeiten | Quelltext bearbeiten]
Das Gefüge, also die Mikrostruktur, bestimmt wie bei den meisten Werkstoffen entscheidend die mechanischen Eigenschaften des Schnellarbeitsstahls. Das Gefüge hängt ab von der Art und Menge der Legierungselemente und dem Wärmebehandlungszustand.
Gefüge im Gebrauchszustand[Bearbeiten | Quelltext bearbeiten]
Nach dem Gießen und während der Bearbeitung der HSS-Werkzeuge ähnelt das Gefüge dem normaler Stähle; es sind zusätzlich noch Partikel aus Legierungselementen enthalten mit Größen von einigen Mikrometern, die jedoch keinen besonderen Einfluss haben. Bei fertigen HSS-Werkstücken liegt der Werkstoff im abgeschreckten und angelassenen Zustand vor. Die Grundmasse besteht wie bei allen Werkzeugstählen aus Martensit, das hauptsächlich aus Eisen und Kohlenstoff besteht. Die kleinen Kohlenstoff-Atome befinden sich in den Lücken zwischen den deutlich größeren Eisen-Atomen, sodass diese sich kaum bewegen können, weshalb Martensit sehr hart und verschleißfest ist. Außerdem sind noch Teile der übrigen Legierungselemente im Martensit eingebunden, was zur hohen Festigkeit von Schnellarbeitsstahl durch Mischkristallverfestigung führt.[10] Das gesamte Eisen befindet sich im Martensit, aber nur ein Teil des Kohlenstoffs; der übrige Teil verbindet sich mit den Legierungselementen (außer Cobalt) zu Carbiden, Verbindungen die noch deutlich härter sind als Martensit. Ihre Härte spielt für die Gesamthärte des Schnellarbeitsstahls keine wesentliche Rolle. Carbidfreier Martensit wandelt sich ab etwa 200 °C in weichere Formen des Stahls um. Die Carbide selbst sind thermisch sehr beständig und lösen sich erst bei über 1000 °C wieder im Grundgefüge. Die Carbide liegen in Form von winzigen Partikeln (Körnern) vor. Die größeren mit Durchmessern im Bereich von Mikrometern entstehen nach dem Gießen, sie machen etwa 10 bis 15 % des Volumens aus.[11] Sie bestehen auch teilweise noch bei Temperaturen von über 1290 °C und sorgen dafür, dass Schnellarbeitsstahl bei diesen Temperaturen geglüht werden kann ohne seine Festigkeit durch Kornwachstum zu verringern. Die kleineren Partikel sind deutlich kleiner als ein Mikrometer (etwa 0,05 µm[12]), sind sehr zahlreich, entstehen als Ausscheidung beim Anlassen, befinden sich in der Nähe der Korngrenzen der Martensitkörner und behindern Diffusion, die bei höheren Temperaturen einsetzen würde und einen Abfall an Härte und Festigkeit bewirken würde. Außerdem verspannen sie das Martensitgitter, sodass es sich erst bei Temperaturen ab 600 °C umwandeln kann.[13][14]
Legierungselemente[Bearbeiten | Quelltext bearbeiten]


Neben dem Kohlenstoff, der in sämtlichen Stählen vorliegt, enthält Schnellarbeitsstahl eine Reihe von weiteren Legierungselementen. Die größte Bedeutung haben Wolfram und Molybdän, die untereinander austauschbar sind. Außer dem Cobalt verbinden sie sich alle mit Kohlenstoff zu Carbiden.[15] Molybdän und Wolfram bilden zusammen mit Eisen das Doppelkarbid[16] Fe3(W,Mo)3C mit einer Vickershärte von 1.150 HV.[17]
Die Legierungselemente haben folgende Wirkung und Aufgaben:[18]
- Wolfram: Bildet Karbide (insb. Wolframcarbid), erhöht die Warmhärte, die Anlassbeständigkeit und die Verschleißfestigkeit.
- Molybdän: Kann Wolfram ersetzen und hat bei halber Masse die gleiche Wirkung wie Wolfram. Molybdän bildet Karbide, verbessert die Durchhärtung, die Zähigkeit, Warmhärte, Anlassbeständigkeit und Verschleißfestigkeit. Molybdänreiche Sorten müssen einer aufwendigeren Wärmebehandlung unterzogen werden, die jedoch Stand der Technik ist.[19] Außerdem[20] sind sie meist günstiger.
- Vanadium: Bildet Vanadiumcarbid, das, wie in einigen anderen Stählen, wegen seiner Härte (2000 HV) die Verschleißbeständigkeit erhöht.
- Cobalt: Erhöht die Temperatur, bis zu der der Werkstoff einsetzbar ist, also ab der sich der Martensit umwandelt. Es behindert das Wachstum der ausgeschiedenen Carbide.[21]
- Chrom: Ist an der Karbidbildung beteiligt und verbessert die Durchhärtbarkeit. Dadurch können auch Werkzeuge mit größeren Querschnitten gehärtet werden.
- Kohlenstoff: Wird einerseits benötigt, um Martensit zu bilden und andererseits, um die Karbide zu bilden. Sein Anteil wird an die Anteile der übrigen Elemente angepasst.
Sorten und Bezeichnungen[Bearbeiten | Quelltext bearbeiten]
Die Bezeichnungen beginnen mit „HS“ (DIN EN ISO 4957) oder „S“ gefolgt von einer Ziffernfolge, die den prozentualen Anteil der metallischen Legierungselemente angibt in der Reihenfolge Wolfram-Molybdän-Vanadium-Cobalt (W-Mo-V-Co). Die Standardsorte HS6-5-2 beispielsweise enthält 6 % Wolfram, 5 % Molybdän, 2 % Vanadium, (kein Cobalt), Chrom nach Norm, eine darauf abgestimmte Menge an Kohlenstoff und sonst Eisen. Im englischsprachigen Raum werden sie in zwei Gruppen eingeteilt:[22] Wolframreiche Sorten beginnen mit einem T (von engl. Tungsten = Wolfram), molybdänreiche beginnen mit einem M. In beiden Fällen folgt eine Nummer zur Unterscheidung verschiedener Sorten, die aber keine weitere Bedeutung hat.[23] Pulvermetallurgisch hergestellte Sorten, erhalten den Zusatz PM. Sie weisen höhere Festigkeiten auf, sind aber teurer.
Die Schnellarbeitsstähle werden in insgesamt vier Gruppen eingeteilt, die sich in der Menge an Wolfram und Molybdän unterscheiden.
- Die erste Gruppe enthält 18 % Wolfram und fast kein Molybdän. Dazu zählen die Sorten HS18-0-1 und 18-1-2-5.
- Die zweite Gruppe enthält 12 % Wolfram und bis 4 % Molybdän. Beispiele sind die Sorten HS 12-1-4-5 und HS-10-4-3-10.
- Die dritte Gruppe enthält 6 % Wolfram und 5 % Molybdän. Dazu zählt die Standardsorte HS6-5-2 sowie HS6-5-3 oder HS6-5-2-5.
- Die vierte Gruppe enthält maximal 2 % Wolfram und 9 % Molybdän. Zu ihr gehören die Sorten HS2-9-1, HS2-9-2 oder HS2-10-1-8.
Die molybdänreichen Sorten sind besonders zäh und unempfindlich gegenüber schlagartigen Beanspruchungen.
Der Vanadiumgehalt schwankt zwischen 0 und 4 %, der Cobaltgehalt beträgt entweder null oder mindestens 5 % für Werkzeuge mit erhöhten Temperaturanforderungen. Alle Sorten enthalten 4–5 % Chrom.[24][25]
Eigenschaften[Bearbeiten | Quelltext bearbeiten]
Härte und Warmhärte[Bearbeiten | Quelltext bearbeiten]
Die Härte bei Raumtemperatur ist ähnlich wie gewöhnlicher gehärteter Stahl bei Werten von 800 bis 900 HV (Vickershärte), bzw. etwa 65 HRC (Rockwell). Bis etwa 400 °C verringert sie sich nur geringfügig, danach schneller, ab 600 °C fällt die Härte rapide ab auf Werte, die für Werkzeuge nicht mehr brauchbar sind.[26] Gewöhnlicher Werkzeugstahl verliert seine Härte bereits ab etwa 200 °C. Die konkurrierenden Hartmetalle erreichen Härten von 1300 bis 1700 HV, Schneidkeramiken sogar 1400 bis 2400. Beide behalten sie bis Temperaturen von 1000 °C und höher.[27]
Festigkeit, Biegefestigkeit und Warmfestigkeit[Bearbeiten | Quelltext bearbeiten]
Die Druckfestigkeit bei Raumtemperatur beträgt etwa 2000 bis 3000 N/mm2, bei 600 °C beträgt sie noch 1700 N/mm2.[28] Werkzeugstähle liegen etwas darunter, Hartmetalle darüber mit Werten von 4000 bis 5900 N/mm2 bei Raumtemperatur.[29]
Die Biegefestigkeit bei Raumtemperatur liegt bei Schnellarbeitsstahl bei etwa 2500 bis 3800 N/mm2, was der höchste Wert aller Schneidstoffe ist. Die Biegefestigkeit bestimmt vor allem die Bruchempfindlichkeit bei schlagartigen Belastungen. Hartmetalle erreichen Werte von 800 bis 2200 N/mm2, Schneidkeramiken nur noch 300 bis 700 N/mm2.[30]
Verschleißfestigkeit und Verschleiß[Bearbeiten | Quelltext bearbeiten]
In der Zerspantechnik kommen verschiedene Verschleißmechanismen vor. Je nach herrschender Temperatur an der Schneide sind sie verschieden stark ausgeprägt.
Plastische Deformation[Bearbeiten | Quelltext bearbeiten]
Bei hohen Temperaturen (über 600 °C) und hohen Druck- oder Scherkräften kommt es zu plastischen (dauerhaften, nicht-elastischen) Verformungen. Die dazu nötigen Kräfte und Temperaturen kommen nur vor bei der Zerspanung von hochfesten Werkstoffen wie hochlegiertem Stahl, Titan oder Nickel, sowie insbesondere bei deren Legierungen. Hohe Temperaturen treten vor allem bei hohen Schnittgeschwindigkeiten auf. In der industriellen Praxis ist dieser Verschleißtyp nur selten zu sehen, da die Werkzeuge extrem schnell verschleißen; dieser Verschleißtyp stellt jedoch den begrenzenden Faktor für die Schnittgeschwindigkeit dar. Die Deformation kann sowohl als Kolkverschleiß (auf der Spanfläche) als auch als Verformung der Schneidkante auftreten. Ursache ist auch der Verfestigungseffekt bei hohen Umformgeschwindigkeiten in Folge der hohen Schnittgeschwindigkeiten, die zu höheren Kräften und damit auch Temperaturen führen.[31]
Diffusion[Bearbeiten | Quelltext bearbeiten]
Diffusion ist ein Verschleißmechanismus, der erst bei hohen Temperaturen auftritt und in der industriellen Praxis ebenfalls selten ist. Die Legierungselemente des Werkzeuges wandern dabei in den Span, während aus dem Span unerwünschte Elemente in das Werkzeug wandern. Beide Effekte verringern die Festigkeit des Werkzeuges. Bei hohen Temperaturen kommt Diffusionsverschleiß bei Schnellarbeitsstahl zwar vor, aber der Verschleiß durch plastische Deformation ist wesentlich größer.[32]
Verklebungen (Adhäsion)[Bearbeiten | Quelltext bearbeiten]
Bei niedrigen Schnittgeschwindigkeiten kommt es teilweise zu Verklebungen (Adhäsion) des Spanes mit dem Werkzeug. Wenn nachfolgendes Werkstückmaterial auf die Verklebungen treffen, dann können durch Mikroverschweißungen Teile der Werkzeugoberfläche mit herausgerissen werden. Außerdem kann es bei geringen Schnittgeschwindigkeiten zur Aufbauschneidenbildung kommen, die ebenfalls negative Effekte hat. Verklebungen kommen häufig vor bei Schnellarbeitsstahl.[33]
Abrieb (Abrasion)[Bearbeiten | Quelltext bearbeiten]
Abrieb (Abrasiver Verschleiß) ist die Hauptursache für den Verschleiß von Schnellarbeitswerkzeugen. Wenn im Werkstoff des Werkstückes Partikel enthalten sind, die härter sind als der Martensit des Werkzeuges, dann fungieren diese Partikel wie Schleifkörner und trennen Material aus dem Werkzeug heraus. Viele Werkstück-Werkstoffe enthalten solche Partikel, in Stahl beispielsweise Oxide, Nitride und Carbide. An Gussstücken haften oft Sandkörner an. Durch Verklebungen werden auch manche Karbide aus dem Werkzeug herausgerissen und mitsamt dem Span über die Werkzeugoberfläche geführt.[34]
Bearbeitbarkeit[Bearbeiten | Quelltext bearbeiten]
Im ungehärteten Zustand lässt sich Schnellarbeitsstahl gut zerspanen (siehe Zerspanbarkeit von Stahl), bei hohen Temperaturen auch schmieden, allerdings deutlich schwerer als die meisten anderen Stahlsorten. Im gehärteten Zustand lässt sich Schnellarbeitsstahl praktisch nur noch durch Schleifen bearbeiten; er ist aber sehr gut schleifbar, während konkurrierende Schneidstoffe nur sehr schlecht schleifbar sind. Für HSS sind vor allem gewöhnliche Schleifscheiben ausreichend, während für Hartmetalle und Schneidkeramiken Diamantschleifscheiben nötig sind.
Herstellung und Wärmebehandlung[Bearbeiten | Quelltext bearbeiten]
Zur Herstellung der Schnellarbeitsstähle gibt es zwei verschiedene Methoden: Die schmelzmetallurgische, auf die der Großteil der Produktionsmenge entfällt, und die pulvermetallurgische. Bei der ersten Variante wird das Rohmaterial geschmolzen und zu Barren vergossen, bei der zweiten dienen Pulver als Ausgangsmaterial. Bei beiden Varianten wird das Material anschließend geschmiedet und durch Fräsen und Bohren in Form gebracht. Eine Variante der pulvermetallurgischen Herstellung ist das „Matrizenpressen“, bei dem das Material direkt in Formen gepresst wird ohne Schmieden und Spanen.[35] Alle Varianten enden mit der Wärmebehandlung und dem anschließenden Schleifen der Endkontur.
Schmelzmetallurgische Herstellung[Bearbeiten | Quelltext bearbeiten]
Der Stahl wird zunächst bei 1550 °C geschmolzen und die Legierungselemente werden zugesetzt. Die Schmelze wird dann in Barrenform gegossen. Da niedrigschmelzende Bestandteile zuerst erstarren und daher ungleichmäßig verteilt sind (sogenannte Seigerung, bei hochlegierten Werkstoffen wie Schnellarbeitsstahl besonders ausgeprägt), erfolgt anschließend ein Blockglühen bei 900 °C, um die Bestandteile gleichmäßiger zu verteilen (homogenisieren). Zusätzlich kann das Elektroschlackeumschmelzen (ESU) erfolgen, bei dem immer nur ein kleiner Teil des Blockes geschmolzen wird und diese flüssige Stelle durch den Block geführt wird. Das Material gewinnt dadurch an Reinheit und wird gleichmäßiger, der Prozessschritt ist jedoch relativ teuer. Anschließend erfolgt das Walzen und Schmieden, das zum Zerkleinern der verschiedenen Hartstoffe (Ledeburit und Karbide) dient und bei Temperaturen um 1200 °C erfolgt. Danach erfolgt das Weichglühen, um die nachfolgende Schmiedeschritte und die spanende Bearbeitung (Fräsen, Bohren) zu ermöglichen, bei der die grobe Form der Werkzeuge herausgearbeitet wird.[36]
Pulvermetallurgische Herstellung[Bearbeiten | Quelltext bearbeiten]
Zur Erzeugung der Pulver gibt es zwei Möglichkeiten: Wasserverdüsen und Gasverdüsen.[37]
- Gasverdüstes Pulver wird in Kapseln gefüllt und heißisostatisch gepresst, also bei hohen Temperaturen und bei konstantem Druck. Anschließend erfolgt die Warmumformung (Walzen, Schmieden) und das Spanen, danach die Wärmebehandlung.
- Für wasserverdüstes Pulver gibt es abermals zwei Methoden der Weiterverarbeitung:
- Kaltisostatisches Pressen bei Raumtemperatur. Die Porosität wird dabei nicht vollständig beseitigt. Danach erfolgt ein Sintern, eine Art Glühen knapp unter der Schmelztemperatur, bei normalem Umgebungsdruck. Danach erfolgt das Walzen und Schmieden zur Beseitigung der Poren, dann Spanen und schließlich die Wärmebehandlung.
- Matrizenpressen: Diese Variante wird für die Herstellung von Wendeschneidplatten angewandt. Das Pulver wird in Formen gepresst und vollständig verdichtet, die Porosität wird also vollständig beseitigt. Anschließend werden die Platten durch heißisostatisches Nachverdichten nachbearbeitet und schließlich wärmebehandelt. Walzen, Schmieden oder Spanen erfolgt hier nicht. Diese Variante ähnelt somit der Herstellung der Wendeplatten aus Hartmetall.
Wärmebehandlung[Bearbeiten | Quelltext bearbeiten]
Die Wärmebehandlung ist der entscheidende Schritt, bei dem der Schnellarbeitsstahl seine Warmhärte und -festigkeit erhält. Außerdem ist es der letzte Schritt vor dem Fertigarbeiten durch Schleifen. Die Wärmebehandlung besteht aus zwei Teilschritten: Dem Glühen und Abschrecken, sowie das anschließende Anlassen. Diese Prozesse werden auch bei vielen anderen Stählen angewandt, bei Schnellarbeitsstahl gibt es jedoch einige Besonderheiten.
Ziel des Glühens ist es, möglichst viele Legierungselemente im eisenhaltigen Grundgefüge zu lösen. Die Löslichkeit steigt allgemein mit der Temperatur, bei Stahl ist jedoch entscheidend, dass sich die Mikrostruktur bei hohen Temperaturen (je nach Kohlenstoffgehalt) ändert und in Form von Austenit vorliegt, in dem die Löslichkeit deutlich größer ist. Die Werkstücke werden langsam auf Glühtemperatur erhitzt, da die Wärmeleitfähigkeit von Schnellarbeitsstahl gering ist und die Wärme im Inneren der Werkstücke nur langsam steigt. Außerdem würde es bei stark verschiedener Außen- und Innentemperatur zu Wärmespannungen kommen, die die Werkstücke durch Risse zerstören würden. Je höher die Temperatur ist, desto mehr Legierungselemente können gelöst werden und je länger geglüht wird, umso größer ist der Anteil, der tatsächlich gelöst wird. Mit der Temperaturhöhe und Glühdauer wird jedoch auch der unerwünschte Effekt des Kornwachstums beschleunigt, der die Festigkeit verringert. Geglüht wird bei ungefähr 1200 °C. Auch bei diesen hohen Temperaturen liegt noch ein Teil der Legierungselemente in Form von Carbiden vor, die das Kornwachstum begrenzen, weshalb Schnellarbeitsstahl zu den wenigen Stählen zählt, die bei diesen Temperaturen ohne nennenswerten Festigkeitsverlust (also ohne Kornwachstum) geglüht werden können.
Nach der gewünschten Glühdauer wird der Werkstoff relativ schnell abgekühlt (Abschrecken). Dadurch entsteht das martensitische Grundgefüge, das Schnellarbeitsstahl seine Härte verleiht. Wegen der hohen Abkühlgeschwindigkeiten verbleiben mehr Legierungselemente gelöst als bei Raumtemperatur eigentlich gelöst werden können. Die Eisenatome können sich daher kaum bewegen. Ein für das nachfolgende Anlassen wichtiger Nebeneffekt liegt darin, dass die Legierungselemente über den gesamten Werkstoff fein verteilt sind und nicht in Partikeln angehäuft vorliegen wie bei langsamer Abkühlung. Ein kleiner Teil des Gefüges liegt immer noch als Austenit vor (Restaustenit).

Beim anschließenden Anlassen laufen in den einzelnen Gefügebestandteilen unterschiedliche Prozesse ab, die von der Höhe der Temperatur abhängen. Bis etwa 400 °C ändert sich nur das martensitische Grundgefüge. Die zwangsgelösten Elemente verlassen das Eisengitter und die Härte geht zurück, bei niedrigen Temperaturen nur unwesentlich, bei höheren immer schneller. Bis etwa 350 °C wird vor allem Kohlenstoff aus dem Martensit ausgeschieden, darüber auch die metallischen Legierungselemente, die sich mit dem Kohlenstoff zu den Karbiden verbinden. Da die Legierungselemente fein verteilt sind, bilden sie zahlreiche winzige Partikel und führen so zu einer Ausscheidungshärtung. Ab etwa 450 °C scheiden aus dem Restaustenit ebenfalls fein verteilte Karbide aus. Wegen der geringeren Anteile an Legierungselementen im Restaustenit wandelt er sich nun in Martensit um (Sekundärmartensit), was ebenfalls zu einer Härtezunahme führt. Die Härtezunahme durch die Ausscheidung von Carbiden und Bildung von Sekundärmartensit fällt dabei größer aus als der Härteverlust des ursprünglichen Martensits. Das Anlassen wird meist bei Temperaturen um 560 °C durchgeführt und ein- oder zweimal wiederholt.[38]
Oberflächenbehandlungen und Beschichtungen[Bearbeiten | Quelltext bearbeiten]
Die Oberflächen der HSS-Werkzeuge können entweder einer Oberflächenbehandlung unterzogen werden oder sie werden beschichtet. Beides erhöht den Verschleißwiderstand und damit die Standzeit und geringfügig die anwendbare Schnittgeschwindigkeit.[39] Die folgenden Verfahren werden genutzt:[40]
- Nitrieren erhöht den Stickstoffgehalt an der Oberfläche.
- Dampfanlassen bildet eine dünne Schicht aus Eisen(II,III)-oxid.
- Verchromen, Aufbringen einer Schicht aus Chrom von etwa 50 bis 70 µm Dicke.
- PVD-Beschichten (Physikalische Gasphasenabscheidung), mit Titannitrid oder Titanaluminiumnitrid.
- Kaum genutzt wird das CVD-Beschichten (Chemische Gasphasenabscheidung), da die dafür nötigen Temperaturen weit über 600 °C liegen. Lediglich bei Wendeplatten aus HSS, die sich kaum verziehen, wird es genutzt. Nach der Beschichtung müssen sie nachgehärtet werden.[41]
Die Beschichtungen erhöhten auch dann noch die Verschleißfestigkeit, wenn sie bei ehemals verschlissenen Werkzeugen durch Nachschleifen teilweise entfernt wurden.[42]
Einzelnachweise[Bearbeiten | Quelltext bearbeiten]
- ↑ Was ist Werkzeugstahl? ( des vom 16. Mai 2018 im Internet Archive) Info: Der Archivlink wurde automatisch eingesetzt und noch nicht geprüft. Bitte prüfe Original- und Archivlink gemäß Anleitung und entferne dann diesen Hinweis. , In: Kontur-Werkzeugstahl.de
- ↑ Alfred Herbert Fritz, Günter Schulze:: Fertigungstechnik. Springer, 11. Auflage, 2015, S. 296 f.
- ↑ Wilfried König, Fritz Klocke: Fertigungsverfahren 1: Drehen, Bohren, Fräsen. 8. Auflage, Springer 2008, S. 110–113.
- ↑ Trent, Wright: Metal Cutting. Butterworth Heinemann, 2000, 4. Auflage, S. 132.
- ↑ Trent, Wright: Metal Cutting. Butterworth Heinemann, 2000, 4. Auflage, S. 133, 138.
- ↑ Trent, Wright: Metal Cutting. Butterworth Heinemann, 2000, 4. Auflage, S. 139.
- ↑ Trent, Wright: Metal Cutting. Butterworth Heinemann, 2000, 4. Auflage, S. 138.
- ↑ Trent, Wright: Metal Cutting. Butterworth Heinemann, 2000, 4. Auflage, S. 142 f.
- ↑ Trent, Wright: Metal Cutting. Butterworth Heinemann, 2000, 4. Auflage, S. 139 f.
- ↑ Fritz, Schulze: Fertigungstechnik, 9. Auflage, S. 275.
- ↑ Trent, Wright: Metal Cutting. Butterworth Heinemann, 2000, 4. Auflage, S. 140.
- ↑ Trent, Wright: Metal Cutting. Butterworth Heinemann, 2000, 4. Auflage, S. 142.
- ↑ Wilfried König, Fritz Klocke: Fertigungsverfahren 1 : Drehen, Fräsen, Bohren. 8. Auflage. Springer, Berlin 2008, S. 117 f.
- ↑ Trent, Wright: Metal Cutting. Butterworth Heinemann, 2000, 4. Auflage, S. 142." the particles remain stable for many hours and harden the steel by blocking the dislocations which facilitate slip between the layers of iron atoms"
- ↑ Wilfried König, Fritz Klocke: Fertigungsverfahren 1 : Drehen, Fräsen, Bohren. 8. Auflage. Springer, Berlin 2008, S. 111 f.
- ↑ Wilfried König, Fritz Klocke: Fertigungsverfahren 1 : Drehen, Fräsen, Bohren. 8. Auflage. Springer, Berlin 2008, S. 110.
- ↑ Trent, Wright: Metal Cutting. Butterworth Heinemann, 2000, 4. Auflage, S. 140.
- ↑ Wilfried König, Fritz Klocke: Fertigungsverfahren 1 : Drehen, Fräsen, Bohren. 8. Auflage. Springer, Berlin 2008, S. 111 f.
- ↑ Trent, Wright: Metal Cutting. Butterworth Heinemann, 2000, 4. Auflage, S. 143.
- ↑ Trent, Wright: Metal Cutting. Butterworth Heinemann, 2000, 4. Auflage, S. 143.
- ↑ Trent, Wright: Metal Cutting. Butterworth Heinemann, 2000, 4. Auflage, S. 143.
- ↑ Trent, Wright: Metal Cutting. Butterworth Heinemann, 2000, 4. Auflage, S. 141.
- ↑ Wilfried König, Fritz Klocke: Fertigungsverfahren 1 : Drehen, Fräsen, Bohren. 8. Auflage. Springer, Berlin 2008, S. 110 f.
- ↑ Trent, Wright: Metal Cutting. Butterworth Heinemann, 2000, 4. Auflage, S. 143.
- ↑ Wilfried König, Fritz Klocke: Fertigungsverfahren 1 : Drehen, Fräsen, Bohren. 8. Auflage. Springer, Berlin 2008, S. 110 f.
- ↑ Trent, Wright: Metal Cutting. Butterworth Heinemann, 2000, 4. Auflage, S. 144.
- ↑ Fritz, Schulze: Fertigungstechnik, 11. Auflage, S. 296.
- ↑ Trent, Wright: Metal Cutting. Butterworth Heinemann, 2000, 4. Auflage, S. 145.
- ↑ Fritz, Schulze: Fertigungstechnik, 11. Auflage, S. 296.
- ↑ Fritz, Schulze: Fertigungstechnik, 11. Auflage, S. 296.
- ↑ Trent, Wright: Metal Cutting. Butterworth Heinemann, 2000, 4. Auflage, S. 150–155.
- ↑ Trent, Wright: Metal Cutting. Butterworth Heinemann, 2000, 4. Auflage, S. 155–157.
- ↑ Trent, Wright: Metal Cutting. Butterworth Heinemann, 2000, 4. Auflage, S. 157–159.
- ↑ Trent, Wright: Metal Cutting. Butterworth Heinemann, 2000, 4. Auflage, S. 159–161.
- ↑ Wilfried König, Fritz Klocke: Fertigungsverfahren 1 : Drehen, Fräsen, Bohren. 8. Auflage. Springer, Berlin 2008, S. 113.
- ↑ Wilfried König, Fritz Klocke: Fertigungsverfahren 1 : Drehen, Fräsen, Bohren. 8. Auflage. Springer, Berlin 2008, S. 114.
- ↑ Wilfried König, Fritz Klocke: Fertigungsverfahren 1 : Drehen, Fräsen, Bohren. 8. Auflage. Springer, Berlin 2008, S. 113–115.
- ↑ Wilfried König, Fritz Klocke: Fertigungsverfahren 1 : Drehen, Fräsen, Bohren. 8. Auflage. Springer, Berlin 2008, S. 115–118.
- ↑ Denkena: Spanen, 3. Auflage, S. 174.
- ↑ Wilfried König, Fritz Klocke: Fertigungsverfahren 1 : Drehen, Fräsen, Bohren. 8. Auflage. Springer, Berlin 2008, S. 118.
- ↑ Denkena: Spanen, 3. Auflage S. 174.
- ↑ Denkena: Spanen, 3. Auflage, S. 174.