Epoxidharz


Als Epoxidharz oder abgekürzt EP-Harz bezeichnet man Kunstharze, die Epoxidgruppen tragen.[1][2] Es handelt sich um Reaktionsharze, die nach Vermischung mit einem Härter zu einem duroplastischen Kunststoff reagieren. Der Härter ist dabei Reaktionspartner und bildet zusammen mit dem Harz einen makromolekularen Polyether mit in der Regel zwei endständigen Epoxidgruppen. Je nach Anwendung können Farb- und weitere Zusatzstoffe eingebunden werden.
Nach der Aushärtung besitzen Epoxidharze gute mechanische Eigenschaften sowie eine gute Temperatur- und Chemikalienbeständigkeit und gelten als hochwertige, aber teure Kunststoffe. Sie werden u. a. als Reaktions- und Einbrennlacke, Klebstoffe, für Laminate, als Einbettmittel in der Metallographie und als Formmassen für Komponenten in der Elektrotechnik und Elektronik verwendet.[3]
Geschichte
[Bearbeiten | Quelltext bearbeiten]Epoxide wurden zuerst von Paul Schlack in Wolfen (Patentanmeldung 1934, erteilt 1939) und Pierre Castan in der Schweiz (Patent-Anmeldung 1938 in der Schweiz, erteilt 1940, von der Ciba AG produziert) entwickelt.
Epoxidharze (Präpolymere und Monomere)
[Bearbeiten | Quelltext bearbeiten]Die meisten kommerziell verwendeten Epoxidharze werden durch die Umsetzung von einer Verbindung mit Hydroxygruppen und Epichlorhydrin hergestellt:
- Zuerst reagiert eine Hydroxygruppe in einer Kupplungsreaktion mit Epichlorhydrin, gefolgt von einer Dehydrohalogenierung.
Derartige Epoxidharze werden Glycidyl-basierte Epoxidharze genannt. Die Hydroxygruppe kann dabei von aliphatischen Diolen, Polyolen, phenolischen Verbindungen oder Dicarbonsäuren stammen. Als Phenole werden Verbindungen wie Bisphenol A und Novolake verwendet. Als mehrwertige Alkohole werden Verbindungen wie 1,4-Butandiol eingesetzt. Di- und Polyole führen zu Diglycid-Polyethern. Für Diglycid-Esterharze werden Dicarbonsäuren, wie Hexahydrophthalsäure verwendet. Statt einer Hydroxygruppe kann aber auch das Stickstoffatom eines Amins oder Amids reagieren.
Die zweite Möglichkeit zur Herstellung von Epoxidharzen ist die Umsetzung aliphatischer oder cycloaliphatischer Alkene mit Persäuren:[3][4]
Für diese Herstellung ist im Gegensatz zu Glycidyl-basierten Epoxidharzen kein azides Wasserstoffatom, sondern eine Doppelbindung notwendig.
Bisphenol-basierte Epoxid-Harze
[Bearbeiten | Quelltext bearbeiten]Etwa 75 % aller weltweit verwendeten Epoxidharze basieren auf Bisphenol A. Aus diesem wird in einer Reaktion mit Epichlorhydrin Bisphenol-A-diglycidylether hergestellt:
- In einer zweistufigen Reaktion wird zuerst Epichlorhydrin an Bisphenol A addiert (es entsteht Bis(3-chlor-2-hydroxy-propoxy)bisphenol A), anschließend in einer Kondensationsreaktion mit einer stöchiometrischen Menge an Natriumhydroxid das Bis-Epoxid gebildet. Das Chloratom wird in Form von Natriumchlorid abgespalten, das Wasserstoffatom in Form von Wasser.
Höhermolekulare Diglycidylether (n ≥ 1) bilden sich bei der Reaktion des gebildeten Epoxids mit weiterem Bisphenol A:
Bei wenigen Moleküleinheiten (n = 1 bis 2) erhält man eine viskose, klare Flüssigkeit und man spricht von flüssigen Epoxidharzen. Bei mehr Moleküleinheiten (n = 2 bis 30) erhält man einen farblosen Feststoff, entsprechend spricht man von festen Epoxidharzen.
Anstelle von Bisphenol A können auch andere Bisphenole verwendet werden (speziell Bisphenol F) oder bromierte Bisphenole.
Novolak-Epoxidharze
[Bearbeiten | Quelltext bearbeiten]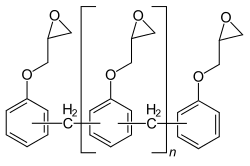
Die Umsetzung von Phenolen mit Formaldehyd führt zu Novolaken. Das anschließende Anfügen von Epoxidgruppen mit Epichlorhydrin erzeugt Novolake mit Glycidyl-Resten, wie Epoxyphenol-Novolak (EPN) oder Epoxycresol-Novolak (ECN). Diese hochviskosen bis festen Harze tragen typischerweise 2 bis 6 Epoxidgruppen pro Molekül. Durch die hohe Funktionalität dieser Harze bildet sich durch die Härtung hochvernetzte Polymere mit hoher Temperatur- und Chemikalienbeständigkeit, aber geringer mechanischer Flexibilität.[3]
Aliphatische Epoxidharze
[Bearbeiten | Quelltext bearbeiten]Es gibt zwei Sorten aliphatischer Epoxidharze: Solche, die durch Epoxidierung von Doppelbindungen erhalten werden (cycloaliphatische Epoxide und epoxidierte Pflanzenöle) und solche, die durch Reaktion mit Epichlorhydrin gebildet werden (Glycidyl-Ether und -Ester).

Cycloaliphatische Epoxide enthalten einen oder mehrere aliphatische Ringe im Molekül, an welchen der Oxiranring enthalten ist (z. B. 3,4-Epoxycyclohexylmethyl-3′,4′-epoxycyclohexancarboxylat). Sie werden durch die Reaktion eines cyclischen Alkens mit einer Persäure hergestellt (siehe oben).[5] Cycloaliphatische Epoxide zeichnen sich durch ihr aliphatisches Gerüst, einen hohen Oxiran-Gehalt und die Abwesenheit von Chlor aus, was zu niedriger Viskosität sowie (wenn ausgehärtet) zu guter Wetterbeständigkeit, niedrigen dielektrischen Konstanten und hohem Tg führt. Jedoch polymerisieren aliphatische Epoxidharze bei Raumtemperatur nur sehr langsam, sodass meist höhere Temperaturen und geeignete Beschleuniger notwendig sind. Da Aliphaten im Gegensatz zu Aromaten eine niedrigere Elektronendichte aufweisen, reagieren cycloaliphatische Epoxide im Vergleich zu Bisphenol-A-basierten Epoxidharze (besitzen aromatische Ethergruppen) weniger leicht mit Nukleophilen. Somit können nur schlecht gewöhnliche, nukleophile Härter wie z. B. Amine zur Vernetzung verwendet werden. Cycloaliphatische Epoxide werden daher meist thermisch oder UV-initiiert in einer elektrophilen bzw. kationischen Reaktion homopolymerisiert. Durch die niedrige dielektrischen Konstanten sowie die Abwesenheit von Chlor werden cycloaliphatischen Epoxide häufig zur Verkapselung elektronischer Systeme verwendet, wie etwa von Mikrochips oder LED. Zudem werden sie für strahlengehärtete Farben und Lacke verwendet. Durch ihren hohen Preis sind sie jedoch bisher auf derartige Anwendungen beschränkt geblieben.[3]
Epoxidierte Pflanzenöle bilden sich durch Epoxidierung von ungesättigten Fettsäuren, ebenfalls durch Umsetzung mit Persäuren. In diesem Fall können die Persäuren auch in-situ durch Umsetzung von Carbonsäuren mit Wasserstoffperoxid gebildet werden. Verglichen mit LERs (liquid epoxy resins) weisen sie sehr niedrige Viskositäten auf. Wenn sie jedoch in größeren Mengen als Reaktivverdünner genutzt werden, führt dies häufig zu verringerter chemischer und thermischer Widerstandsfähigkeit und zu schlechteren mechanischen Eigenschaften der gehärteten Epoxide. In großem Umfang hergestellte epoxidierte Pflanzenöle wie epoxidierte Soja- und Leinöle werden zum großen Teil als Sekundärweichmacher und Costabilisatoren für PVC genutzt.[3]
Aliphatische Glycidyl-Epoxidharze niedriger molarer Masse (mono-, bi- oder auch höherfunktional) werden durch die Reaktion von Epichlorhydrin mit aliphatischen Alkoholen oder Polyolen gebildet (es entstehen Glycidyl-Ether) oder mit aliphatischen Carbonsäuren (es entstehen Glycidyl-Ester). Die Reaktion wird in Anwesenheit einer Base wie Natriumhydroxid durchgeführt, analog der Bildung von Bisphenol A-diglycidether. Auch aliphatische Glycidyl-Epoxidharze weisen meist eine niedrige Viskosität auf. Sie werden daher anderen Epoxidharzen zur Herabsetzung der Viskosität als Reaktivverdünner oder auch als Haftvermittler zugegeben. Epoxidharze aus (langkettigen) Polyolen werden darüber hinaus zur Verbesserung der Zug- und Schlagfestigkeit zugesetzt.
Halogenierte Epoxidharze
[Bearbeiten | Quelltext bearbeiten]Halogenierte Epoxidharze werden für spezielle Eigenschaften zugesetzt, es kommen bromierte und fluorierte Epoxidharze zum Einsatz.[3]
Bromiertes Bisphenol A wird verwendet, wenn flammhemmende Eigenschaften benötigt werden, wie etwa in manchen elektrischen Anwendungen (z. B. Leiterplatten). Das tetrabromierte Bisphenol A (TBBPA, 2,2-Bis(3,5-dibromphenyl)propan) oder dessen Diglycidether, 2,2-Bis[3,5-dibrom-4-(2,3-epoxypropoxy)phenyl]propan, können dazu der Epoxid-Formulierung beigemischt werden. Die Formulierung kann dann in derselben Weise wie reines Bisphenol A umgesetzt werden. Einige (unvernetzte) Epoxidharze mit sehr hoher molarer Masse werden technischen Thermoplasten beigefügt, ebenfalls um flammhemmende Eigenschaften zu erzielen.
Fluorierte Epoxidharze wurden für einige Hochleistungsanwendungen erforscht, wie beispielsweise der fluorierte Diglycidether 5-Heptafluorpropyl-1,3-bis[2-(2,3-epoxypropoxy)hexafluor-2-propyl]benzol. Da es eine niedrige Oberflächenspannung besitzt, wird es als Netzmittel (Tensid) für den Kontakt mit Glasfasern zugesetzt. Die Reaktivität gegenüber Härtern ist vergleichbar mit Bisphenol A. Ausgehärtet führt das Epoxidharz zu einem Duroplasten mit hoher chemischer Widerstandsfähigkeit und niedriger Wasseraufnahme. Die kommerzielle Verwendung von fluorierten Epoxidharzen wird jedoch durch ihre hohen Kosten und ihren niedrigen Tg eingeschränkt.
Charakterisierung
[Bearbeiten | Quelltext bearbeiten]Epoxidharz-Produkte werden über unterschiedliche Kennzahlen charakterisiert. Hierzu zählen die Molmasse bzw. die Molmassenverteilung, die Hydroxylzahl sowie das Epoxid-Äquivalentgewicht. Des Weiteren bestimmt die bereits erwähnte Glasübergangstemperatur eine entscheidende Rolle für die Eigenschaften der später erhaltenen Produkte.
Härter und Härtung
[Bearbeiten | Quelltext bearbeiten]Härter |
![]() 1,3-Diaminobenzol |
![]() Diethylentriamin |
![]() Hexahydrophthalsäure - anhydrid |
Als Härter werden mehrwertige Amine („aminische Härter“), wie zum Beispiel 1,3-Diaminobenzol, und aliphatische Amine, wie zum Beispiel Diethylentriamin oder 4,4′-Methylenbis(cyclohexylamin), verwendet. Die Aushärtung mit aliphatischen Aminen erfolgt bereits bei Zimmertemperatur (Kalthärtung); aromatische Amine erfordern eine Heißhärtung. Bei „sauren Härtern“, die oft Dicarbonsäureanhydride wie Hexahydrophthalsäureanhydrid sind, erfolgt die Aushärtung bei höheren Temperaturen, oft im Bereich zwischen 120 °C bis 160 °C. Die reaktiven Ethylenoxidringe der Epoxidharze reagieren in Additionsreaktionen mit den funktionellen Gruppen der Härter. Weiterhin findet durch den katalytischen Einfluss der Aminogruppen in wechselndem Umfang eine anionische Polymerisation der Epoxidgruppen statt. Starke Säuren bewirken eine kationische Polymerisation.
Verarbeitung
[Bearbeiten | Quelltext bearbeiten]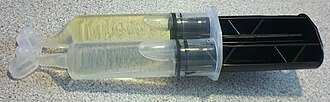
Wie bei allen Reaktionsharzen muss beim Anmischen von Reaktionsharzmassen das stöchiometrische Harz-Härter-Verhältnis genau eingehalten werden – andernfalls verbleiben Teile von Harz oder Härter ohne Reaktionspartner. Diese unreagierten funktionellen Gruppen bleiben zurück und die Vernetzung bleibt unvollständig, was zu einem weichen Produkt und zu klebrigen Oberflächen führt. Einige Epoxidsysteme sind jedoch weniger empfindlich und innerhalb enger Grenzen ausdrücklich für eine Variation des Mischungsverhältnisses geeignet. Dadurch lassen sich Härte, Elastizität und andere Eigenschaften beeinflussen; so wird die Säurebeständigkeit durch einen höheren Anteil Epoxidharz erhöht. Da eine inhomogene Mischung der beiden Komponenten den gleichen negativen Effekt wie ein falsches Mengenverhältnis hat, sind umfangreiche Mischprozeduren beim Anmischen notwendig. Wenn die Farbgebung des resultierenden Kunststoffes ohne Belang ist, können als Durchmischungsindikator die beiden Ausgangsstoffe kontrastreich gefärbt sein. Die Polyaddition ist stark exotherm. Die entstehende Reaktionswärme kann so groß werden, dass es zum Brand kommt; zumindest können jedoch die Eigenschaften des Harzes durch die Überhitzung negativ beeinflusst werden. Für Bauteile mit großen Wanddicken werden daher niedrigreaktive Harze verwendet.
Die Verarbeitungsdauer von Reaktionsharzmassen wird Topfzeit genannt. Sie hängt von der Verarbeitungstemperatur, der Einstellung der Reaktionsharzmassen und der Ansatzgröße ab. Übliche Topfzeiten liegen bei einigen Minuten bis hin zu mehreren Stunden. Während der Topfzeit steigt die Viskosität des Harzes in einer nichtlinearen Kurve immer weiter an, bis schließlich keine Verarbeitung mehr möglich ist. Die Angabe der Topfzeit ist in der Regel bei einem Harz/Härter-Ansatz von 100 g bei 20 °C gemacht – größere Verarbeitungsmengen entwickeln eine höhere Temperatur und haben eine wesentlich kürzere Verarbeitungszeit.
Eine Erwärmung des angemischten Harzes verringert die Viskosität und verbessert dadurch im Allgemeinen die Verarbeitbarkeit, verkürzt aber auch die Topfzeit. Eine Erhöhung der Verarbeitungstemperatur um 10 °C bewirkt eine Halbierung der Topf- bzw. Aushärtezeit (RGT-Regel). Niedrigreaktive Epoxidharze benötigen lange Härtezeiten und möglichst eine erhöhte Härtungstemperatur (30 °C bis 40 °C). Bei Bedarf können noch Beschleuniger (hochreaktive Härter) zugegeben werden, die die Reaktionszeit verkürzen. Einige Epoxidharze können zur vollständigen Vernetzung und zum Erreichen einer höheren Wärmeformbeständigkeit nach der Aushärtung einer Warmhärtung unterzogen werden.
Beim Warmhärten (Temperung) steigt die Glasübergangstemperatur (Tg) der Matrix um ca. 20 °C bis 25 °C über die maximale Warmhärtungstemperatur an – dies ist der sogenannte Temperaturvorlauf. Raumtemperaturanhärtende Systeme härten bei Raumtemperatur teilweise mit einer sehr spröden Matrix – eine Härtung über 40 °C/5 h bis 6 h beseitigt diese und verbessert zusätzlich die mechanischen Eigenschaften.
Die Reaktionsharzmassen werden häufig mit niedrigviskosen Zusätzen modifiziert. Durch die niedrigere Viskosität der Reaktionsharzmasse wird eine bessere Penetration in poröse Werkstoffe (Tränkung von Geweben, Beschichtung von Beton) erreicht oder die Verarbeitbarkeit durch Spritzpressen (RTM-Verfahren) verbessert. Andererseits erlauben derartige Reaktionsharzmassen eine höhere Beladung mit Füllstoffen, woraus bei der Härtung ein geringerer Volumenschrumpf resultiert. Ebenfalls können die mechanischen Eigenschaften des gehärteten Harzes verbessert werden, ebenso die Ökonomie. Für diese Zwecke werden bevorzugt Glycidylether verwendet, da diese – im Gegensatz zu nicht reaktiven Verdünnern – kovalent an das Polymer gebunden werden und daher auch nicht migrieren können.
Gebräuchlich als Reaktivverdünner sind:
Monoglycidylether neigen dazu, die Polyaddition abzubrechen, da sie nur monofunktionell sind. Daher beeinträchtigen sie die Festigkeit und die Temperaturbeständigkeit, erhöhen aber die Flexibilität. Glycidylether von Phenolen wirken hier weniger nachteilig als Alkylglycidylether, werden aber toxikologisch ungünstiger beurteilt. Bei den Alkylglycidylethern werden langkettige (C12–C14) wegen ihres niedrigen Dampfdrucks bevorzugt eingesetzt; sie lassen sich günstig aus Fettalkoholen herstellen.
- Polyglycidylether
Diese mehrfunktionellen Reaktivverdünner werden eingesetzt, wenn höhere Ansprüche an die mechanischen Eigenschaften gestellt werden. Da sie über mindestens zwei (wie der häufig eingesetzte 1,6-Hexandioldiglycidylether) Epoxidgruppen verfügen, bewirken sie keinen Abbruch der Polyaddition.
Reaktionsharzmassen können mit Zuschlagstoffen (z. B. pyrogenem Siliciumdioxid) versehen werden, um sie thixotrop einzustellen. Dieses verdickte Harz kann als Füllmasse oder Klebstoff verwendet werden. Andere Zuschlagstoffe dienen als Füllmittel (Hohlkugeln aus Glas, Keramik oder Kunststoffen), um die Dichte des Harzes zu verringern, um die Griffigkeit bzw. Abrasionsbeständigkeit der Oberfläche zu verbessern (Quarzsand, keramische Pulver) oder um die maximale Dauer-Betriebstemperatur zu steigern (Metallische Füllstoffe: Aluminium-, Eisen/Stahlpulver). Zuschlagstoffe (wie Aluminiumhydroxid) können das brandhemmende Verhalten von Epoxidharz verbessern. Dies ist besonders beim Einsatz in Verkehrsmitteln wichtig.
Das Aushärten kann mittels Zugabe von Photoinitiatoren mit Ultraviolett gestartet werden, wodurch Aushärtezeiten im Sekundenbereich erreicht werden.[6]
Eigenschaften
[Bearbeiten | Quelltext bearbeiten]Das ungefüllte ausgehärtete Harz hat eine Dichte von 1020 bis etwa 1200 kg/m3. Der Elastizitätsmodul beträgt 3000 bis 4500 MPa und die Zugfestigkeit etwa 80 MPa. Diese Werte variieren je nach Formulierung und Herstellung.
Die Dielektrizitätszahl beträgt im Temperaturbereich −40 bis etwa +60 °C etwa 4 und steigt ebenso wie der dielektrische Verlustfaktor bei beginnender Erweichung (80 bis 100 °C) stark an. Der Verlustfaktor hat bei 40 °C ein Minimum, beträgt dort 50 bis 100 · 10−4 und steigt bei 100 bis 120 °C durch Orientierungspolarisation großer Kettensegmente auf etwa das 10 bis 20-fache an. Bei −40 °C ist ebenfalls ein Maximum (3 bis 10-facher Wert desjenigen bei 40 °C), hier hervorgerufen durch Orientierungspolarisation kurzer Kettensegmente.[7] Es werden Werkstoffe mit CTI-Werten (Kriechstromfestigkeit) von über 600 V angeboten. Durch Bromierung wird das Material schwer entflammbar (UL94 V-1 oder besser).
Die Wärmeleitfähigkeit beträgt 0,21 W/(m·K)[8] und kann durch Füllstoffe wesentlich gesteigert werden (isolierende elektrische Vergussmassen etwa 1,26 W/(m·K)[9] bis 6 W/(m·K)[10]).
Die chemische Schwindung bei der Polyaddition ist mit 0,5 bis 5 % deutlich geringer als bei den ungesättigten Polyesterharzen. Sie kann mit Füllstoffen noch weiter verringert werden.
Das ungefüllte Harz ist transparent gelblich bis wasserklar und ist auch ultraviolettbeständig bzw. vergilbungsfrei erhältlich. Bei Wellenlängen unterhalb 400 nm wird Epoxidharz nahezu intransparent, im Infrarotbereich ist es bis 2000 nm transparent. Der Brechungsindex liegt bei 1,5 bis 1,59 (bei 589,3 nm Natrium-D-Linie).[11]
Verwendung
[Bearbeiten | Quelltext bearbeiten]- Vielseitiger Konstruktions-Klebstoff, etwa im Bootsbau, Haushalt und Modellbau
- Speziell eingestellte Epoxidharze finden als Metallkleber Anwendung
- Mörtel auf Kunststoffbasis (Reaktionsharzmörtel)
- zur Produktion von Steinteppichen
- Gießharz zur Herstellung von Bauteilen im Gussverfahren
- Wird in Verbindung mit Glasfaser, Kohlenstofffaser und Aramidfaser beim Bau von modernen Hochleistungs-Segelflugzeugen, aber auch zunehmend bei großen Passagierflugzeugen (Kohlenstoff- bzw. Carbonfaser) als Faserverbundkunststoff eingesetzt
- Glasfaserverstärkter Kunststoff kommt für die Herstellung der Rotorblätter von Windkraftanlagen zum Einsatz
- Herstellung von Mineralgussgestellen für den Maschinenbau
- Industriefußboden; Betonbeschichtung; Betonreparatur
- Ionenaustauschersäulen (Chemie)
- Anstrich; schwerer Korrosionsschutz (Schiffbau, Stahlkonstruktionen)
- Abdichtung von Holzterrarien (Terrarientechnik), da ausgehärtet ungiftig
- Bindemittel für verschiedene Anstrichstoffe (Lacke), durch Kombination von Phenolharzen entstehen Innenschutzlackierungen für Verpackungsmittel aller Art, von Haarspraydosen bis zu Lebensmittelverpackungen (sogenannte Goldlacke)
- Lacke zum Schutz vor Graffiti
- Herstellung von wasserlöslichen Kunstharzen zur kathodischen Tauchlackierung (KTL, Automobilbau)
- Sanierung von Rohren, insbes. Rohrinnensanierung (etwa von Trinkwasserleitungen, Fußbodenheizungen)
- Bemalung von Radwegen[12]
- Vergießen von elektrischen Bauteilen oder anderen Objekten zwecks Isolation und Korrosionsschutz
- Leiterplattenmaterial wie FR-4 als Trägermaterial von elektronischen Schaltungen
- Matrixmaterial für die Herstellung von Faserverbundbauteilen, unter anderem für Luft- und Raumfahrt, für den Motorsport, in der Orthopädietechnik und für den Yachtbau; häufig auch im Handlaminierverfahren
- Plastination; insbesondere spezielle Epoxidharze, wie Epoxy E-12, werden zur Fixierung anatomischer Präparate eingesetzt[13]
- Wird auf Kanten (coping) von Skateboardrampen für bessere Rutschfähigkeit und als Schutz aufgebracht
- Trägermaterial in der Kunst
- Material zur Abformung in der Bildhauerei
- Herstellung von Dünnschliffen
- Bau von Epoxidharz-Tischen wie z. B. Rivertable[14]
Beim Bau von Bootsrümpfen hat Epoxidharz gegenüber manchen Polyesterharzen unter anderem den Vorteil, dass es Osmoseschäden ausschließt, selbst wenn Seewasser durch eine beschädigte Gelcoat-Schicht dringt und mit dem Werkstoff in Berührung kommt. Deshalb wird Epoxidharz auch zur Reparatur von Osmoseschäden an Polyesterharz-Bootsrümpfen verwendet.
Umweltverträglichkeit
[Bearbeiten | Quelltext bearbeiten]Epoxidharz war über lange Zeit nicht recyclingfähig und die Stoffe zu dessen Herstellung wurden überwiegend aus Erdöl gewonnen. Forschende aus Graz konnten jedoch erstmals biobasierte Epoxid-Duroplaste herstellen, die durch eine Reaktion mit Methanol wieder komplett in ihre Bestandteile zerlegt werden können. Das ermöglicht eine komplette Wiederverwertung.[15]
Epoxidharz ist bereits seit längerem auch als Variante erhältlich, welche zu 99–100 % aus nachwachsenden Rohstoffen gewonnen wurde. Preislich und von in Bezug auf Festigkeit und Klarheit unterscheiden sich diese neuen Produkte kaum von herkömmlichen Produkten.[16][17]
Sicherheit und Gesundheit
[Bearbeiten | Quelltext bearbeiten]Herstellung
[Bearbeiten | Quelltext bearbeiten]Epoxidharz wird industriell gewöhnlich aus einer Reaktion von Bisphenol A und Epichlorhydrin hergestellt. Aufgrund der spezifischen Charakteristik insbesondere dieser beiden Reaktanten sind bei der Herstellung von Epoxidharz besondere Sicherheitsvorschriften zu beachten (zu möglichen Gesundheitsgefahren und Stand der Forschung siehe insbesondere auch die Artikel Bisphenol A und Epichlorhydrin).
Epoxidharz wurde unter der Bezeichnung Bisphenol-A-diglycidylether 2013 von der EU gemäß der Verordnung (EG) Nr. 1907/2006 (REACH) im Rahmen der Stoffbewertung in den fortlaufenden Aktionsplan der Gemeinschaft (CoRAP) aufgenommen. Hierbei werden die Auswirkungen des Stoffs auf die menschliche Gesundheit bzw. die Umwelt neu bewertet und ggf. Folgemaßnahmen eingeleitet. Ursächlich für die Aufnahme der Substanz waren die Besorgnisse bezüglich Verbraucherverwendung, hoher (aggregierter) Tonnage und weit verbreiteter Verwendung sowie der Gefahren ausgehend von einer möglichen Zuordnung zur Gruppe der CMR-Stoffe und als potentieller endokriner Disruptor. Die Neubewertung läuft seit 2015 und wird von Dänemark durchgeführt. Um zu einer abschließenden Bewertung gelangen zu können, wurden weitere Informationen nachgefordert.[18]
Verarbeitung
[Bearbeiten | Quelltext bearbeiten]Epoxidharz-Produkte
Sicherheitshinweise | ||||||||
---|---|---|---|---|---|---|---|---|
Name |
Bisphenol-A-Epichlorhydrinharze mit durchschnittlicher Molmasse ≤700 g/mol | |||||||
CAS-Nummer | ||||||||
|
Epoxidharz wird üblicherweise in zwei Komponenten geliefert, die vom Anwender gebrauchsfertig zu mischen sind. Die sog. „A-Komponente“ enthält meist das Epoxidharz, die „B-Komponente“ den Härter, der in einem vorbestimmten Mischungsverhältnis dem Harz zuzugeben ist.
Üblicherweise sind Epoxidharze mit den GHS-Symbolen GHS07 („Achtung“) und GHS09 („Umweltgefährlich“) und mit entsprechenden H- und P-Sätzen versehen. Die vielfach zum Einsatz kommenden Epoxidharz-Härter auf Amin-Basis müssen üblicherweise ebenfalls mit GHS-Symbolen (häufig GHS05, „Ätzend“) gekennzeichnet und ebenfalls mit H- und P-Sätzen versehen werden. Da die Gefährdungs- und Sicherheitshinweise in Abhängigkeit von eingesetztem Produkt und Härtertyp variieren, ist den Sicherheitsdatenblättern der verwendeten Produkte besondere Aufmerksamkeit zu schenken.
Schutzausrüstung bei der Applikation
Da der direkte Hautkontakt als weitaus schädlicher anzusehen ist als etwa eine Aufnahme über die Atemwege (z. B. durch ungenügende Belüftung), ist persönliche Schutzausrüstung beim Einsatz vieler Epoxidprodukte vorgeschrieben. Zum Hautschutz eignen sich ausschließlich spezielle Nitril- oder Butyl-, Butyl/Viton- und PE-Laminat-Handschuhe. Ungeeignet sind dünne Einweg-Handschuhe unabhängig vom Material (zum Beispiel Latex, Vinyl oder Nitril). Die allergenen Stoffe durchdringen diese Handschuhe auch ohne Beschädigung innerhalb weniger Minuten, während der Eigenschutz der Haut durch Schwitzen bei fehlender Belüftung geschwächt wird. Hautschutzsalben bieten ebenfalls keinen akzeptablen Schutz. Unter Umständen kann zusätzlich das Tragen eines Schutzanzugs notwendig sein.
Einsatzgebiete
[Bearbeiten | Quelltext bearbeiten]Bezüglich der Verwendung von Epoxidharz-Systemen können ggf. je nach Einsatzgebiet und Anwendungsbereich ergänzende – auch gesetzliche – Anforderungen an Sicherheit und Gesundheit bestehen, so z. B. in den Bereichen Kinderspielzeug, Trinkwasser, Lebensmittelbedarfsgegenstände etc.
Arbeitsschutz
[Bearbeiten | Quelltext bearbeiten]Inhaltsstoffe von Epoxidharzen haben sensibilisierende Eigenschaften. Bei ungeeigneter Arbeitsweise kann der Verarbeiter sensibilisiert werden, danach kann es zu allergischen Reaktionen in Form von Hautausschlägen kommen, vor allem beim Kontakt mit nicht ausgehärteten Epoxidharzen. Um Möglichkeiten zur Vermeidung von epoxidharzbedingten allergischen Hauterkrankungen zu erarbeiten, wurden verschiedene Arbeitskreise gegründet und Forschungsprojekte initiiert. Die bisherigen Ergebnisse dieser Arbeiten finden sich gesammelt auf der Epoxidharzseite des Instituts für Arbeitsschutz der Deutschen Gesetzlichen Unfallversicherung (IFA)[20].
Literatur
[Bearbeiten | Quelltext bearbeiten]- Walter Krauß (Hrsg.): Kittel: Lehrbuch der Lacke und Beschichtungen. Band 2: Bindemittel für lösemittelhaltige und lösemittelfreie Systeme, 2. Aufl., Hirzel Verlag, 1998, ISBN 978-3-7776-0886-0.
- Barbara Schmid, Jürgen Wehde, Ursula Vater: Gefahrstoffinformation und Gefährdungsbeurteilung bei der Verarbeitung von Epoxidharzen. In: Gefahrstoffe – Reinhaltung der Luft. 70(1/2), 2010, S. 17–21.
- Edward M. Petrie: Epoxy Adhesive Formulations. Verlag Mc Graw-Hill, 2006, ISBN 0-07-145544-2.
Weblinks
[Bearbeiten | Quelltext bearbeiten]- MATERIALARCHIV: Epoxidharze. – Umfangreiche Materialinformationen und Bilder
- The Chemistry of Epoxide. Polymer Science Learning Centre (PSLC), The University of Southern Mississippi – The Department of Polymer Science, Hattiesburg (Mississippi USA) 2005; Leicht verständliche Erklärung (englisch).
- Praxisleitfaden der Berufsgenossenschaft Bau für den Umgang mit Epoxidharzen
- Leitfaden des Hamburger Amtes für Arbeitsschutz zur Gefährdungsbeurteilung von Epoxidharzsystemen mit Hinweisen zu Schutzmaßnahmen (PDF; 814 kB).
Einzelnachweise
[Bearbeiten | Quelltext bearbeiten]- ↑ Hans-Dieter Jakubke, Ruth Karcher (Hrsg.): Lexikon der Chemie. 3. Bände, Spektrum Akademischer Verlag, Heidelberg, 2003, ISBN 978-3-8274-1151-8.
- ↑ Deutsches Institut für Normung: DIN-Term Beschichtungsstoffe. Vincentz Network, 2001, ISBN 978-3-87870-721-9, S. 65, eingeschränkte Vorschau in der Google-Buchsuche.
- ↑ a b c d e f Ha Q. Pham, Maurice J. Marks: Epoxy Resins. In: Ullmann’s Encyclopedia of Industrial Chemistry. doi:10.1002/14356007.a09_547.pub2.
- ↑ Wolfgang Kaiser: Kunststoffchemie für Ingenieure. 3. Aufl. Hanser, München 2011, ISBN 978-3-446-43047-1, S. 437 ff.
- ↑ L. Hammerton, ed. by Rebecca Dolbey: Recent Developments in Epoxy Resins. RAPRA Review Reports, 1996, ISBN 978-1-85957-083-8, S. 8.
- ↑ Epoxid-Klebstoffe ( vom 5. Juli 2016 im Internet Archive) (PDF; 757 kB), auf panacol.de.
- ↑ M. Beyer, W. Boeck, K. Möller, W. Zaengl: Hochspannungstechnik: Theoretische und praktische Grundlagen. Springer Verlag, 1992, 362 Seiten, ISBN 978-3-540-16014-4 (Reprint), S. 206 f.
- ↑ H. Schürmann: Konstruieren mit Faser-Kunststoff-Verbunden. 2. Auflage, Springer-Verlag 2007; 672 Seiten, ISBN 978-3-540-72189-5, S. 269.
- ↑ Technisches Datenblatt zu ER2074 von Electrolube S. 2. ( vom 28. Januar 2017 im Internet Archive) (PDF; 93 kB), auf files.voelkner.de, abgerufen am 28. Januar 2017.
- ↑ Temperaturbeständiges Epoxid-Gießharz mit hoher Wärmeleitfähigkeit Pressemitteilung der Fa. Kyocera.
- ↑ Tech Tip 18: Verstehen der optischen Eigenschaften bei Epoxyanwendungen (PDF; 353 kB), Fa. Kummer Semiconductor Technology.
- ↑ Grünbeschichtungen für bessere Sichtbarkeit der Radwege in Berlin. Abgerufen am 25. April 2019.
- ↑ Plastination. The Medical University Vienna (englisch) Medizinische Universität Wien, aufgerufen am 14. Oktober 2021
- ↑ Epoxidharz Tisch selbst bauen ► Step-by-Step Anleitung. Abgerufen am 31. Mai 2023.
- ↑ Xianyuan Wu, Peter Hartmann, Dimitri Berne, Mario De bruyn, Florian Cuminet, Zhiwen Wang, Johannes Matthias Zechner, Adrian Daniel Boese, Vincent Placet, Sylvain Caillol, Katalin Barta: Closed-loop recyclability of a biomass-derived epoxy-amine thermoset by methanolysis. In: Science. Band 384, Nr. 6692, 12. April 2024, doi:10.1126/science.adj9989.
- ↑ Nachhaltige und biobasierte Epoxidharze. Abgerufen am 5. August 2024.
- ↑ Die Epoxidharz Revolution - Unsere neuen Produkte. Abgerufen am 5. August 2024.
- ↑ Community Rolling Action Plan (CoRAP) der Europäischen Chemikalienagentur (ECHA): 2,2'-[(1-methylethylidene)bis(4,1-phenyleneoxymethylene)]bisoxirane, abgerufen am 20. Mai 2019.
- ↑ a b Sicherheitsdatenblatt Epoxydharz L (PDF; 119 kB), von R&G Faserverbundwerkstoffe GmbH, abgerufen am 6. Mai 2013.
- ↑ Institut für Arbeitsschutz der Deutschen Gesetzlichen Unfallversicherung (IFA): Epoxidharze. Abgerufen am 9. November 2021.