Drehen (Verfahren)

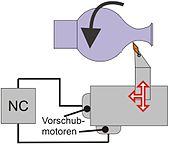
Das Drehen ist gemeinsam mit dem Bohren, Fräsen und Schleifen eines der wichtigsten Fertigungsverfahren der Zerspantechnik. Wie bei allen diesen Verfahren werden von einem Werkstück Späne abgetrennt, um die gewünschte Form zu erzeugen. Beim Drehen rotiert das Werkstück – das Drehteil – um seine eigene Achse, während das Werkzeug – der Drehmeißel – die am Werkstück zu erzeugende Kontur abfährt. Die entsprechende Werkzeugmaschine ist eine Drehmaschine. Eine rein manuelle Variante wie beim Schleifen und Bohren gibt es nicht, bei weicheren Werkstoffen kann aber das Werkzeug mit der Hand geführt werden. Grundsätzlich lassen sich alle zerspanbaren Werkstoffe drehen. Besonderheiten zum Drehen von Holz finden sich unter Drechseln. Berufe, die sich mit dem Drehen befassen, sind der Drechsler für die Holzbearbeitung und der Dreher, der inzwischen gemeinsam mit dem Fräser vom Zerspanungsmechaniker abgelöst worden ist. Betriebe oder Abteilungen von Betrieben, die sich hauptsächlich dem Drehen widmen, werden als Dreherei bezeichnet.
Da bei den Drehmeißeln sämtliche Winkel und Radien der Schneide bekannt sind, zählt das Drehen zur Gruppe Spanen mit geometrisch bestimmter Schneide, zu der auch das Bohren und Fräsen zählen.
Das Drehen ist seit dem Altertum bekannt und war während der industriellen Revolution von Bedeutung zur Herstellung von überwiegend runden Teilen wie Schrauben und Spindeln für die Textilindustrie. Heute wird es für die Herstellung von Achsen, Wellen und Flanschen sowie allgemein rotationssymmetrischen Teilen eingesetzt.
Die erreichbaren Genauigkeiten bezüglich Abmessungen, Formen und Oberflächenrauheit sind wie bei den meisten zerspanenden Verfahren vergleichsweise gut. Die Werkstücke sind nach dem Drehen entweder einbaufertig oder müssen nur noch durch Schleifen fertigbearbeitet werden.
Das Drehen wird in zahlreiche Verfahrensvarianten eingeteilt. Wird der Drehmeißel parallel zur Rotationsachse des Werkstückes bewegt (Runddrehen oder Längsdrehen), so entstehen zylindrische Formen. Wird er dagegen senkrecht zur Rotationsachse bewegt, ergeben sich ebene Formen (Plandrehen). Außerdem gibt es Varianten für die Gewindefertigung oder für beliebige rotationssymmetrische Formen (z. B. Kegel oder Kugeln). Für größere Serien geeignet ist das Profildrehen mit Werkzeugen, die die zu fertigende Form als Negativ enthalten. Gedreht werden neben Außenflächen auch Innenflächen an Hohlkörpern. Die beim Drehen verwendeten Spannmittel sind verfahrenstypisch und werden kaum anderweitig benutzt. Dazu zählen unter anderem Drehfutter, Spannzangen und Zentrierspitzen.
Die allgemeinen Grundlagen der Zerspantechnik betreffen die zerspanenden Fertigungsverfahren gleichermaßen, sodass das Drehen hinsichtlich Drehmeißelverschleiß, Standzeiten, Energieumwandlung und Wärme keine Besonderheiten aufweist. Hierzu siehe Verschleiß (Spanen), Standzeit (Zerspanen) und Energieumwandlung und Wärme beim Spanen.
Definitionen[Bearbeiten | Quelltext bearbeiten]


Das Drehen wird häufig als ein spanendes Fertigungsverfahren definiert, bei dem das Werkstück durch seine Rotation die Schnittbewegung erzeugt und das (einschneidige) Werkzeug die Vorschubbewegung. Diese Definition ist in fast allen Fällen korrekt. Sie kann als erster Überblick über die Verfahren und als Abgrenzung gegenüber dem Fräsen dienen. Das Fräsen wird im Gegensatz dazu als ein Verfahren definiert, bei dem das (meist mehrschneidige) Werkzeug rotiert und das Werkstück steht.[1][2][3]
Wälzdrehen und Schäldrehen sind im Unterschied zu dieser Definition Sondervarianten, bei denen sich die Werkzeuge drehen. Beim Wälzdrehen dreht sich das Werkzeug mit der Vorschubbewegung senkrecht zum Werkstück, um sein Profil auf ihm abzubilden, und beim Schäldrehen drehen sich die (mehrschneidigen) Werkzeuge insgesamt um ein stehendes Werkstück. Der wesentliche Unterschied zum Fräsen liegt darin, dass beim Drehen die Rotationsachse der Schnittbewegung mit der Symmetrieachse des Werkstücks identisch ist, während beim Fräsen diese Rotationsachse im Werkzeug liegt. In der DIN 8589, die alle spanenden Fertigungsverfahren definiert, steht daher Folgendes:
Drehen ist Spanen mit geschlossener (meist kreisförmiger) Schnittbewegung und beliebiger Vorschubbewegung in einer zur Schnittrichtung senkrechten Ebene. Die Drehachse der Schnittbewegung behält ihre Lage zum Werkstück unabhängig von der Vorschubbewegung bei.[4]
Diese Definition findet sich auch häufig in der Fachliteratur.[5][6][7][8] Sie ist meist mit dem Hinweis verbunden, dass in der industriellen Praxis fast immer das Werkstück die Schnittbewegung vollführt.[9] Mit dem Ovaldrehen gibt es eine Variante, bei der die Schnittbewegung nicht kreisförmig, aber dennoch in sich geschlossen ist.
Im englischsprachigen Raum versteht man unter turning (wörtlich: „Drehen“) nur das Außendrehen. Das Innendrehen wird als boring bezeichnet.[10] Beide Verfahren werden manchmal als lathe processes (wörtlich: „Drehmaschinen-Prozesse“) bezeichnet; dazu zählt allerdings auch das Bohren, da auf einer Drehmaschine ohne Zusatzeinrichtungen auch gebohrt werden kann.[11]
Geschichte[Bearbeiten | Quelltext bearbeiten]
Das Drehen ist ein sehr altes Fertigungsverfahren, das aus der Bronzezeit stammt. Mit dem Bohren, Schleifen, Sägen und Schaben gibt es jedoch eine Reihe von Verfahren der Zerspantechnik, die bereits seit der Steinzeit bekannt sind.[12] Für das Bohren und Schleifen gab es erste Maschinen. Etwa zeitgleich mit dem Drehen entstand auch das Feilen und Raspeln;[13] innerhalb der Zerspantechnik ist lediglich das Fräsen jünger, das im 19. Jahrhundert entstand.[14]
Im Mittelalter gab es eine Reihe von Verbesserungen an den Drehmaschinen, die die Produktivität erhöhten. Im 17. Jahrhundert wurde das Drehen im Kunsthandwerk beliebt, und im 17. und 18. Jahrhundert gab es Neuerungen in der Uhrmacherei und der Feinmechanik, die die Genauigkeit erhöhten und im Zuge der Industrialisierung auch in den allgemeinen Maschinenbau übernommen wurden. Gedreht wurden Teile für Dampfmaschinen, die Eisenbahn, Textilmaschinen und andere Werkzeugmaschinen. Wichtige Teile waren Schrauben und Spindeln, die in großen Stückzahlen benötigt wurden. Im Laufe des 20. Jahrhunderts wurde das Drehen zunächst durch elektrische Steuerungen und dann durch CNC-Steuerungen weiter automatisiert.
Altertum[Bearbeiten | Quelltext bearbeiten]

Das Drehen hat sich im letzten Jahrtausend v. Chr. aus dem Bohren entwickelt und war den Kulturen um das Mittelmeer und des Alten Orients bekannt, wie aus dieser Zeit erhaltene Werkstücke zeigen, die von den Etruskern, aber auch aus Bayern stammen.[15] Eine Abbildung am Grab des ägyptischen Priesters Petosiris aus dem 3. Jahrhundert v. Chr.[16] zeigt das Drehen mittels Zugschnurdrehbank.[17] Ein Arbeiter zog mit den Händen abwechselnd beide Enden einer Schnur, die ein Werkstück umschlingt, sodass das Werkstück eine links- und eine rechtsläufige Drehung vollführte. Ein zweiter Arbeiter führte das Werkzeug. Genutzt wurden sie vor allem zur Bearbeitung von Holz sowie Elfenbein, Horn, Alabaster und Bronze.[18] Die Maschinen bestanden aus einem etwa kniehohen Rahmen, in dem sich eine senkrecht stehende Spindel drehen konnte, auf der sich das Werkstück befand. Gearbeitet wurde im Hocken, was der damals üblichen Arbeitsweise entsprach.[19] Die Werkzeuge waren vermutlich aus Bronze.[20]
Verbreitung[Bearbeiten | Quelltext bearbeiten]
In Ägypten wurde das Drehen genutzt, wie auch bei den Babyloniern, Assyrern und Phöniziern. Gleichermaßen beherrschten Griechen und Römer die Technik.[21] Die Kelten beherrschten das Drehen nachweislich seit dem 7. Jahrhundert v. Chr. Auch bei den Germanen war die Technik bekannt. Gedrehte germanische Holzfüße sind aus dem 3. Jahrhundert v. Chr. nachgewiesen.[22] Der Römer Vitruv erwähnt in seinem 24 v. Chr. entstandenen Werk De Architectura[23] „zwei auf einer Drehbank angefertigte Achsen in einem Holzrahmen“ (Vitr. 10.15.4). Wie die römische Drehbank ausah, ist nicht bekannt. Die einzige erhaltene Abbildung auf einem Sarkophag aus dem 2. Jahrhundert zeigt nur ein Fragment.[24] Die Maschine wurde mit einem Fidelbogen angetrieben und besaß eine Schwungscheibe. Oreibasios, ein Leibarzt eines Kaisers, soll 382 n. Chr. eiserne Muttern gedreht haben.[25]
Mittelalter[Bearbeiten | Quelltext bearbeiten]

Im 13. Jahrhundert wurde das Drehen durch die aufkommende Wippendrehbank vereinfacht, die sich von einer einzelnen Person bedienen ließ. Das eine Ende der Schnur wurde an einem Pedal angebracht und das andere Ende an einer federnden Latte. Die älteste Abbildung stammt aus einer französischen Bible moralisée aus dem 13. Jahrhundert, die eine arbeitende Nonne zeigt.[26] Im 15. Jahrhundert wurden Kurbeln zum Antrieb von Drehbänken für die Metallbearbeitung genutzt. Durch diesen Antrieb konnte sich das Werkstück kontinuierlich in ein und dieselbe Richtung drehen. Damit war eine bessere Kraftübertragung möglich. Der Meister hatte beide Hände frei, um das Werkzeug zu halten, und konnte bessere Oberflächen erzielen. Allerdings benötigte man wieder einen Gehilfen zum Bedienen der Kurbel.[27]
-
Video: Drehen auf dem Nachbau einer Wippendrehbank
Kunstdrehen vom 16. bis zum 18. Jahrhundert[Bearbeiten | Quelltext bearbeiten]

Im 16. Jahrhundert florierte das Kunsthandwerk und mit ihm das Kunstdrehen.[28][29] Selbst in Adelskreisen war es beliebt. Kaiser Maximilian I. besaß eine besonders reich verzierte Drehbank von 1518.[30] Der Franzose Charles Plumier schrieb 1701 ein Buch mit dem Titel L’art de tourner („Die Kunst/Technik des Drehens“).[31] Im Vorwort erklärte er: „In Frankreich, Italien, England und Deutschland wird die Beschäftigung mit Dreharbeiten so hoch geschätzt, daß es kaum Menschen von Geist geben dürfte, die nicht versuchen, sich mit dieser Kunst hervorzutun […]“[32] Er demonstrierte eine Drehbank zum Ovaldrehen, die mit Hilfe einer Schablone Werkstücke kopieren konnte. Eine weitere dort abgebildete, aber nicht realisierte Drehbank eignet sich zum Gewindeschneiden. Verarbeitet wurden nach wie vor hauptsächlich nichtmetallische Werkstoffe sowie gelegentlich sehr weiche Metalle wie Zinn. Die Maschinen bestanden ebenfalls noch aus Holz.[33]
Feinmechanik und Uhrmacherei im 17. und 18. Jahrhundert[Bearbeiten | Quelltext bearbeiten]
In der Feinmechanik und insbesondere in der Uhrmacherei wurden im 17. und 18. Jahrhundert schon sehr weit entwickelte Maschinen eingesetzt, die im allgemeinen Maschinenbau erst etwa ein Jahrhundert später im Zuge der Industrialisierung genutzt wurden. Für die Feinmechanik waren hohe Maßgenauigkeiten bei den Werkstücken nötig, die meist aus Kupferlegierungen (Messing und Bronze) bestanden. Die Maschinen und die Werkstücke waren jedoch sehr klein und konnten daher durchgängig aus teurem Metall bestehen. An den Maschinen waren Werkzeughalter angebracht, die über Kurbeln bewegt werden konnten und so deutlich genauere Werkstücke erlaubten. Mit Zahnrädern konnte man auch die Werkzeugbewegung an die Drehzahl koppeln und so nahezu identische Schrauben mit gleichmäßigem Gewinde herstellen.[34]
Im 17. und 18. Jahrhundert wurden die Maschinen, Werkzeuge und Verfahren des Handwerks auch erstmals wissenschaftlich untersucht und beschrieben. Das entsprechende Fachgebiet wurde in Deutschland als Technologie bezeichnet und für künftige Verwaltungsbeamte unterrichtet, um so eine gute Wirtschaftsförderung zu ermöglichen. Christoph Weigel der Ältere beschrieb in seinem Buch Abbildung Der Gemein-Nützlichen Haupt-Stände von 1698 zahlreiche Künstler und Handwerker. Eine Abbildung zeigt einen Drechsler an einer Drehbank mit Fußhebel. Als Werkstoffe werden Gold, Silber, Messing, Bein, Holz und Schmucksteine genannt.[35] In Frankreich wurden die Gewerbe unter anderem in der Description des arts et métiers von Réaumur und der Encyclopédie von Diderot beschrieben. Zu sehen ist unter anderem ein Werkzeughalter für die Drehbänke der Uhrenmacher.[22]
Industrialisierung in England[Bearbeiten | Quelltext bearbeiten]
Der Physiker Johann Heinrich Moritz von Poppe erwähnte in seinem Buch Geschichte aller Erfindungen und Entdeckungen um 1837 „Kunstdrehbänke, Figurirbänke und andere Drehmaschinen“, die seit Mitte des 18. Jahrhunderts erfunden worden seien, und darunter besonders die „Schraubendrehbänke und Schraubenschneidmaschinen“.[36]

Durch die generelle Verwendung des Werkzeughalters, der aus der Feinmechanik bekannt war, wurde die Arbeit des Drehens wesentlich erleichtert. Die Werkzeuge wurden nun in der Maschine eingespannt und über Handräder bewegt. Dadurch sanken einerseits die benötigte Kraft, die der Arbeiter auf das Werkzeug ausüben musste, und andererseits die Anforderung an seine Geschicklichkeit. James Nasmyth beschrieb den Werkzeughalter der Drehmaschine als eine der wichtigsten Neuerungen im Maschinenbau. In seinem Aufsatz[37] von 1841 – einem der ersten Aufsätze über Werkzeugmaschinen überhaupt – findet sich ein in der modernen Literatur häufig gezeigtes Bild, das das Drehen von 1800 (ohne Werkzeughalter) mit dem Drehen von 1840 vergleicht. Während der ältere Arbeiter angestrengt an seiner Drehmaschine mit hölzernen Rahmen das Werkzeug mit beiden Händen hält und sich dagegenstemmen muss, steht der Arbeiter von 1840 lässig vor seiner Maschine mit eisernem Rahmen und Werkzeughalter. Die Arbeit ist so einfach, dass er nur eine Hand benötigt, um am Handrad zu drehen, das den Werkzeugschlitten bewegt.

Während der industriellen Revolution in Großbritannien wurden mit Dampfmaschinen angetriebene Drehmaschinen gebaut, die für die Industrialisierung von besonderer Bedeutung waren. Damit wurden zunächst vor allem Teile für Textilmaschinen und Schrauben hergestellt. Spindeln für Textilmaschinen wurden zu Millionen benötigt. Die Werkstücke bestanden Mitte des 18. Jahrhunderts immer häufiger aus Eisenwerkstoffen (Schmiedeeisen und Gusseisen, ab etwa 1870 auch Stahl), die deutlich schwieriger zu bearbeiten waren. Um die Genauigkeit zu steigern, wurden die Maschinen selbst auch aus Eisen gebaut.[38][39] Sie hing jedoch in hohem Maße von der Geschicklichkeit der Arbeiter ab. Der Mangel an geeignetem Personal und die große Bedeutung des Drehens für den Maschinenbau führte 1785 in Großbritannien zu einem Auswanderungsverbot[40] für Dreher und einem Exportverbot für sämtliche Werkzeugmaschinen, also auch der Drehmaschinen. Im frühen 19. Jahrhundert übernahm der Brite Henry Maudslay, der auch als Gründungsvater des britischen Werkzeugmaschinenbaus gilt, die zahlreichen konstruktiven Details der Drehbänke aus der Feinmechanik in den Maschinenbau. Eine seiner ersten Maschinen war eine Tischdrehmaschine für die Fertigung von Schrauben. Die Genauigkeit der Schrauben war nun nicht mehr von der Geschicklichkeit des Arbeiters abhängig.[41] Außerdem waren die verschiedenen Schrauben so gleichmäßig, dass sie untereinander austauschbar waren (sogenannter Austauschbau). Zuvor waren alle Schrauben individuell und jede passte ausschließlich in ein zu ihr gehörendes Gewinde. Erst mit Maudslays Verbesserung verbreitete sich die Nutzung von Schrauben als Verbindungselement. Zuvor waren vor allem Stifte und Keile gebräuchlich.[42]
Industrialisierung in Deutschland und den USA[Bearbeiten | Quelltext bearbeiten]

Nach Deutschland gelangten diese Neuerungen im Rahmen der Industrialisierung mit einigen Jahrzehnten Verzögerung (siehe auch Industrialisierung in Deutschland). Deutsche Beamte erleichterten die Umgehung der Export- und Auswanderungsverbote. Sie organisierten Reisen deutscher Ingenieure und Facharbeiter nach England, halfen bei Zöllen und vergaben Kredite für die Anschaffung von Maschinen. Teilweise wurden diese sogar auf Staatskosten beschafft und den Unternehmen überlassen, mit der Auflage, diese Maschinen jedem Interessenten zu zeigen, um den Nachbau zu ermöglichen. Besonders häufig handelte es sich dabei um Drehmaschinen. Beim Import englischer Maschinen flossen auch Bestechungsgelder. Es handelte sich somit um eine frühe Form von Wirtschaftsspionage. 1835 produzierten von 129 deutschen Maschinenbauunternehmen 19 auch Werkzeugmaschinen, darunter vor allem Dreh-, Bohr- und Zahnradfräsmaschinen.[43]
Gegen 1870 war der Bedarf an identischen Maschinenteilen in Amerika im Rahmen der dort beginnenden Industrialisierung besonders hoch (siehe auch: Geschichte der Vereinigten Staaten#Industrialisierung). Dort entstand erstmals der Drehautomat, der die Werkzeugbewegung und das Wechseln der Werkzeuge selbstständig übernahm. Die Automaten konnten von einer angelernten Hilfskraft bedient werden und mussten nur noch von einer Fachkraft eingerichtet werden, was unter anderem die Auswahl der Werkzeuge betraf. Die Hilfskraft führte die Rohteile zu, entnahm die fertigen Werkstücke aus der Maschine und entfernte die Späne. Gefertigt wurden vor allem Schrauben, sodass die englische Bezeichnung bis heute screw machine (wörtlich: „Schraubenmaschine“) lautet. Weitere wichtige Maschinenteile waren Gewindespindeln für Textil- oder Werkzeugmaschinen, Spindeln für Spinnmaschinen, Wellen zur Kraftübertragung sowie Achsen und Räder für Dampflokomotiven.[44]
Seit 1900[Bearbeiten | Quelltext bearbeiten]
1907 veröffentlichte der Amerikaner Frederick Winslow Taylor die Ergebnisse seiner etwa zehn Jahre dauernden Forschungen zur Zerspantechnik in seinem Buch On the Art of Cutting Metals („Über die Kunst/Technik Metall zu schneiden“), in dem hauptsächlich das Drehen behandelt wird. Bis heute wird das Drehen in der Forschung als Standardverfahren für das Zerspanen betrachtet. Die Materialkennwerte zur Berechnung der Zerspankraft wurden beim Drehen ermittelt. Für andere Verfahren müssen Korrekturfaktoren berücksichtigt werden. Von Taylor stammt auch der Taylorismus und der 1907 vorgestellte Schnellarbeitsstahl, mit dem dreimal höhere Schnittgeschwindigkeiten möglich waren. Mit der Einführung der elektrischen Steuerung in der ersten Hälfte des Jahrhunderts entstanden auch Kopierdreh- und Kopierfräsmaschinen, die ein Modell mit einem Taster erfassen und dessen Bewegung elektronisch an die Antriebe weitergeben konnten, um Werkstücke zu kopieren. Ab den 1920er Jahren wurden die Antriebe der Maschinen auf Elektromotoren umgestellt. Ältere E-Motoren waren für den industriellen Einsatz noch nicht robust genug gewesen.[22]
Ab den 1980er Jahren setzten sich bei den spanenden Werkzeugmaschinen allgemein die CNC-Steuerungen durch. Mit den als CNC-Drehmaschine bezeichneten Maschinen können sehr komplizierte Formen vollautomatisch hergestellt werden, ohne zuvor ein Modell anfertigen zu müssen wie beim Kopierdrehen. Stattdessen muss nur noch ein passendes Programm in den Speicher der Maschine geladen werden; die CNC-Steuerung führt das Werkzeug dann auf die erforderliche Bahn. Drehmaschinen hatten vor Erfindung der CNC-Steuerung gegenüber anderen Werkzeugmaschinen bereits einen sehr hohen (mechanischen) Automatisierungsgrad, sodass es wenig sinnvoll schien, diesen noch weiter erhöhen zu wollen. Dennoch machten CNC-Drehmaschinen lange Zeit weit über die Hälfte aller CNC-Maschinen aus. Durch große Produktivitätssteigerungen ging ihr Anteil schließlich auf knapp die Hälfte zurück, da für dieselbe Aufgabe weniger Drehmaschinen benötigt wurden. Außerdem sind mit ihnen, in Kombination mit entsprechenden Messgeräten, höhere Genauigkeiten möglich, wie sie auch von den Kunden gefordert werden. Es entstanden Drehmaschinen mit mehreren Werkzeugschlitten, die ein Werkstück gleichzeitig und damit in kürzerer Zeit bearbeiten können. Drehzentren verfügen über einen automatischen Werkzeugwechsel, Drehzellen zusätzlich über eine automatische Werkstückversorgung, sodass die Nebenzeiten für den Wechsel geringer ausfallen. Dreh-Fräs-Zentren können in einer einzigen Maschine die Werkstücke sowohl durch Drehen als auch durch Fräsen und Bohren bearbeiten, sodass keine weiteren Maschinen nötig sind. Bei der konventionellen Fertigung müssen die Drehteile dagegen aus der Drehmaschine entnommen und anschließend in die Fräs- und Bohrmaschinen eingespannt werden.[45]
Bedeutung und Werkstückspektrum[Bearbeiten | Quelltext bearbeiten]
Das Drehen ist zusammen mit dem Bohren und Fräsen eines der bedeutendsten[46] und am häufigsten[47] angewandten Fertigungsverfahren der Zerspantechnik und der Fertigungstechnik. Der wertmäßige Anteil der spanenden Werkzeugmaschinen liegt relativ konstant bei etwa einem Drittel des gesamten Produktionswertes sämtlicher Werkzeugmaschinen. Davon wiederum entfällt etwa ein Drittel auf Drehmaschinen oder Bearbeitungszentren, die sich für das Drehen eignen. Die wirtschaftliche Bedeutung zeigte sich spätestens in der Industrialisierung, in der es ohne Drehen und Drehmaschinen nicht möglich gewesen wäre, die zahlreichen Teile für Dampf- und Textilmaschinen herzustellen.[48] Zu diesen Teilen, die auch für moderne Maschinen benötigt werden, zählen Achsen, Wellen, Schrauben, Gewindespindeln, Radnaben, sowie Kleinteile – heute vor allem für die Automobilindustrie und den Allgemeinen Maschinenbau, gegen 1900 insbesondere für Nähmaschinen und Fahrräder. Weitere durch Drehen hergestellte Teile sind Spannfutter für das Drehen, Fräsen oder Bohren, Walzen für Walzwerke, verschiedene Fräs- und Bohrwerkzeuge, Linsen oder Spiegel für die optische Industrie. Durch Feindrehen (Präzisionsdrehen) werden Kugellagerkomponenten hergestellt sowie Pumpenkolben, Synchronräder, Einspritzdüsen, Lagerbüchsen, Normalien, Bauteile von optischen Geräten und Instrumenten (Teile von Okularen und Objektiven), Gehäuse für Pumpen, Flansche, Gehäusedeckel und Teile für Laufwerke von Festplatten.[49][50]
-
Zeichnung einer Welle
-
Gedrehte Schachfiguren
-
Besonders große Welle in einer Drehmaschine
-
Turbinenteil auf einer Karusselldrehmaschine mit Arbeiter (oben links) zum Größenvergleich
-
Räder einer Lokomotive auf einer Radsatzdrehmaschine
-
Ein Flansch
-
Messerköpfe (Fräswerkzeuge)
Erreichbare Genauigkeiten und Oberflächenqualitäten[Bearbeiten | Quelltext bearbeiten]
Das Drehen ist wie die meisten spanenden Fertigungsverfahren relativ präzise. Die Werkstücke sind entweder einbaufertig oder müssen nur noch durch Schleifen nachbearbeitet werden. Die erreichbaren Genauigkeiten hängen wie bei fast allen Verfahren von den Abmessungen der Werkstücke ab und verringern sich mit deren Größe.
Die erreichbaren Maßgenauigkeiten, angegeben als ISO-Toleranz die den Größeneinfluss berücksichtigt, liegen beim Drehen üblicherweise bei IT10 bis IT7 (kleine Zahlen sind genauer). Mit Sondermaßnahmen ist auch IT6 erreichbar. Die Maßgenauigkeit beim Drehen bewegt sich damit im Rahmen dessen, was in der Zerspantechnik üblich ist. Beim Fräsen und Räumen ist sie genauso gut, beim Bohren schlechter (IT14 bis IT12) und beim Schleifen deutlich besser (IT9 bis IT3, mit Sondermaßnahmen auch bis IT1). Mit dem Gießen und Schmieden als konkurrierenden Fertigungsverfahren sind Genauigkeiten von etwa IT11, mit Sondermaßnahmen auch IT8 erreichbar.[51]
Beim Feindrehen oder Präzisionsdrehen sind Genauigkeiten von IT6 bis IT7 erreichbar. Das Hoch- oder Ultrapräzisionsdrehen reicht von IT5 bis IT01. Beim Hartdrehen reicht die Genauigkeit bis IT5. Bei den üblichen Werkstückabmessungen liegen die Maßabweichungen somit unter einem Mikrometer.
Die Oberflächenqualität wird meist als Rauheit gemessen. Beim Drehen ist auf der Oberfläche eine Spur von der Spitze des Werkzeuges erkennbar. Die Rauheit ist beim Drehen umso geringer und damit besser, je größer der Spitzenradius des Werkzeuges und je geringer sein Vorschub ist. Beim Schruppen (Grobbearbeitung) liegen die Rauheiten bei gemittelten Rautiefen von bis 100 µm beim Schlichten (Feinbearbeitung) bei 16 µm bis 25 µm. Mit Präzisionsvarianten sind bis zu 3 oder 4 µm erreichbar, was einer mittleren Rauheit von etwa 0,15 µm entspricht.[52][53]
Bewegungen und Geschwindigkeiten[Bearbeiten | Quelltext bearbeiten]


Allgemein wird die Spanungsbewegung unterschieden nach der Schnittbewegung, die zum Abtrennen des Spanes führt, und der Vorschubbewegung, die für eine kontinuierliche Spanabnahme sorgt. Beim Drehen ist die Schnittbewegung die Rotationsbewegung, die üblicherweise vom Werkstück ausgeführt wird; nur in seltenen Fällen rotieren die Werkzeuge um das Werkstück. Die Vorschubbewegung ist üblicherweise die Bewegung des Werkzeuges, das sich parallel zur Drehachse bewegen kann (Längsdrehen), senkrecht dazu (Querdrehen) oder auch in einer Ebene zwischen diesen beiden Bewegungsrichtungen. Auf manchen Spezialmaschinen wird auch das Drehteil entlang der Drehachse verschoben, um die Vorschubbewegung auszuführen, während das Werkzeug stillsteht.
Die Umfangsgeschwindigkeit des Werkstücks an der Bearbeitungsstelle entspricht der Schnittgeschwindigkeit (von englisch cut ‚Schnitt‘) und wird meist in m/min angegeben. In der Zerspantechnik kommt es grundsätzlich nur auf eine Relativbewegung zwischen Werkstück und -zeug an. Welcher der beiden Wirkpartner sich bewegt und welcher steht, ist nachrangig. Per Konvention werden die Vektoren der Bewegungen so dargestellt, als ob sich das Werkzeug bewegen würde. Beim Drehen auf gewöhnlichen Drehmaschinen zeigt die Schnittgeschwindigkeit daher nach oben, also entgegen der tatsächlichen Werkstückbewegung.
Die Geschwindigkeit in Vorschubrichtung wird als Vorschubgeschwindigkeit bezeichnet (von englisch feed ‚Vorschub‘), sie ist jedoch von untergeordneter Bedeutung. Eine wichtige kinematische Größe ist dagegen der Vorschub , also die Strecke, die das Werkzeug pro Umdrehung in Vorschubrichtung zurücklegt, angegeben meist in mm/Umdrehung. Die Vorschubgeschwindigkeit lässt sich aus der Drehzahl und dem Vorschub berechnen. Der Winkel zwischen der Schnittrichtung und der Vorschubbewegung wird allgemein als Vorschubrichtungswinkel (kleines griechisches Phi) bezeichnet. Beim Drehen (sowie Bohren und weiteren Verfahren) beträgt er konstant 90°. Beim Fräsen dagegen ändert er sich während einer Umdrehung kontinuierlich.
Die Resultierende aus Schnitt- und Vorschubgeschwindigkeit ist die Wirkgeschwindigkeit . Ihr Vektor bildet mit dem Vektor der Schnittgeschwindigkeit den Wirkrichtungwinkel . Meistens entspricht die Wirkgeschwindigkeit in Betrag und Richtung näherungsweise der Schnittgeschwindigkeit.[54]
Drehverfahren[Bearbeiten | Quelltext bearbeiten]
Die Drehverfahren können nach verschiedenen Gesichtspunkten eingeteilt werden. Besonders häufig findet sich die Einteilung nach DIN 8589, die auf der ersten Gliederungsebene nach der erzeugten Form einteilt und daher einen guten Eindruck der herstellbaren Geometrien vermittelt. Weitere wichtige Einteilungen sind
- das Außendrehen und das Innendrehen (Bearbeitung der Innenflächen von Hohlkörpern),
- das Schruppen (Grobbearbeitung) und Schlichten (Feinbearbeitung),
- das Kegeldrehen zur Herstellung kegelförmiger Formelemente,
- das Hartdrehen für gehärtete Werkstücke,
- das Hochgeschwindigkeitsdrehen mit besonders hohen Schnittgeschwindigkeiten.
Je nach Menge des Kühlschmierstoffes unterscheidet man in Nassdrehen und Trockendrehen sowie nach dem Automatisierungsgrad in Drehen auf konventionellen Drehmaschinen, Drehen auf CNC-Drehmaschinen oder auf Drehautomaten.[55]
Einteilung nach erzeugter Form (DIN 8589)[Bearbeiten | Quelltext bearbeiten]
Die wohl wichtigste Einteilung der Verfahrensvarianten findet sich in der DIN 8589 und wird in der Fachliteratur häufig zitiert. Sämtliche zerspanenden Fertigungsverfahren werden auf der ersten Gliederungsebene einheitlich nach der erzeugten Form eingeteilt. Im Falle des Drehens ergibt sich:
- Plandrehen: Herstellung planer (ebener) Flächen
- Runddrehen: Herstellung kreisrunder Formen
- Schraubdrehen: Herstellung von Gewinden
- Wälzdrehen: Herstellung von Wälzflächen (Verzahnungen)
- Profildrehen: Herstellung beliebiger Formen mit Profilwerkzeugen, die die herzustellende Form als Negativ enthalten
- Formdrehen: Herstellung beliebiger Formen durch gesteuerte Werkzeugbewegung
Die weitere Unterteilung folgt verschiedenen Kriterien wie der Werkzeugbewegung (längs oder quer zur Drehachse), den verwendeten Werkzeugen oder der Art der Bewegungserzeugung (manuell, maschinell).
Alle genormten Verfahren und Verfahrensvarianten tragen eine Ordnungsnummer. Bei den Drehverfahren beginnen diese alle mit der Folge 3.2.1. (3. Hauptgruppe: Trennen, 2. Gruppe: Spanen mit geometrisch bestimmter Schneide, 1. Verfahren: Drehen).
Plandrehen[Bearbeiten | Quelltext bearbeiten]

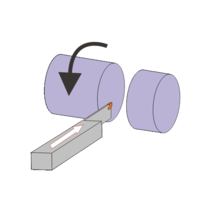
Beim Plandrehen mit der Ordnungsnummer 3.2.1.1 werden ebene (plane) Oberflächen erzeugt, die an der Stirnseite des Drehteils liegen. Die erzeugten Flächen liegen also senkrecht zur Drehachse. Es wird zwischen drei Varianten unterschieden:
- 3.2.1.1.1 Beim Quer-Plandrehen bewegt sich das Werkzeug senkrecht (quer) zur Drehachse. Es ist die wichtigste Variante und wird in der Praxis auch kurz als Plandrehen bezeichnet. Es wird meist als erster Arbeitsgang durchgeführt, um eine Bezugsfläche in axialer Richtung für die weitere Bearbeitung zu erzeugen.[56] Beim Schlichten (Feinbearbeitung) wird meist von innen nach außen gearbeitet, während beim Schruppen (Grobbearbeitung) eher von außen nach innen gearbeitet wird.[57] Das Quer-Plandrehen ist typisch für die Bearbeitung auf Drehautomaten, bei denen meist Kleinteile von der Stange gefertigt werden. Wie bei allen Quer-Drehverfahren ist zu beachten, dass sich bei konstanter Drehzahl die Schnittgeschwindigkeit verändert. Bei konventionellen Drehmaschinen und Drehautomaten wird sie über ein Stufengetriebe innerhalb eines Bereiches gehalten, moderne CNC-Drehmaschinen können eine konstante Schnittgeschwindigkeit erreichen.[58]
- 3.2.1.1.2 Das Quer-Abstechdrehen dient dazu, Werkstückteile abzutrennen oder das gesamte Werkstück vom stangenförmigen Rohmaterial abzutrennen.[59] Die Werkzeuge sind dabei sehr schmal, um den Materialverlust zu minimieren; sie neigen daher jedoch auch zum Schwingen, was beim Spanen als Rattern bezeichnet wird. Die Werkzeuge verfügen über eine Hauptschneide, die zur Drehachse orientiert ist, sowie links und rechts davon zwei Nebenschneiden. Beim Einstechdrehen ist die Hauptschneide nicht parallel zur Drehachse (Werkzeug-Einstellwinkel ist größer 90°). Dadurch hat während des Abstechens das Verbindungsstück zwischen den zu trennenden Teilen die Form eines Kegelstumpfes. In der Endphase der Bearbeitung verjüngt sich dessen Spitze immer weiter, bis das Werkstück fast ohne Restzapfen abgetrennt wird.[60][61]
- 3.2.1.1.3 Beim Längs-Plandrehen bewegt sich das Werkzeug parallel zur Drehachse. Das Werkstück ist dabei hohl und die Werkzeugschneide ist breiter als die Dicke des Werkstücks. Die entstehende Fläche ist ringförmig.[62]
-
Quer-Plandrehen
-
Quer-Abstechdrehen
-
Längs-Plandrehen
Runddrehen[Bearbeiten | Quelltext bearbeiten]

Beim Runddrehen mit Ordnungsnummer 3.2.1.2 werden runde Oberflächen erzeugt, die auf der Mantelfläche eines Zylinders liegen, dessen Achse mit der Drehachse zusammenfällt. Es wird zwischen den fünf Varianten Längs-, Breitschlicht-, Schäl-, Längs-Abstech- und Quer-Runddrehen unterschieden. Vor allem das Längs-Runddrehen hat eine große Bedeutung und wird in Normen und in der Fachliteratur als Referenz herangezogen. In Lehrbüchern wird häufig diese Variante gewählt, um grundsätzliche Begriffe und Phänomene der Zerspantechnik zu erläutern. Diese Variante wird für Kleinteile in der Uhrenindustrie ebenso genutzt wie für die Großserienfertigung von Turbinenläufen oder Antriebswellen mit Längen von bis zu 20 m.[63]
- 3.2.1.2.1 Beim Längs-Runddrehen bewegt sich das Werkzeug parallel zur Drehachse. Als wichtigste Variante wird es in der Praxis kurz als Runddrehen bezeichnet. Es lässt sich mit einer großen Bandbreite verschiedener Werkzeuge durchführen, die auf die jeweiligen Anforderungen zugeschnitten sind.[64]
- 3.2.1.2.2 Beim Breitschlicht-Runddrehen oder Breitschlichtdrehen wird ein Werkzeug mit sehr großem Eckenradius und sehr kleinem Werkzeug-Einstellwinkel der Nebenschneide verwendet, wobei große Vorschübe möglich werden.[65]
- 3.2.1.2.3 Das Schäldrehen, Schäl-Runddrehen oder Schälen ist eine Sondervariante des Längs-Runddrehens mit besonders hohem Vorschub. Dieser wird üblicherweise durch die gleichzeitige Verwendung mehrerer Werkzeuge erreicht, die meist einen kleinen Einstellwinkel der Nebenschneide aufweisen. Die Werkzeuge sind in der Regel radial um das Werkstück herum angeordnet, um das sie sich drehen, während das Werkstück nur den Vorschub ohne Rotation ausführt.[66] Das Schäldrehen wird oft genutzt, um Blankstahl herzustellen, und zeichnet sich durch ein hohes Zeitspanvolumen aus. Es ist sehr produktiv und kann sehr gute Oberflächen erzeugen.[67][68] Vorschübe von bis zu 15 mm und Rauheiten von = 2–10 µm sind erreichbar.[69]
- 3.2.1.2.4 Das Längs-Abstechdrehen dient dazu, runde Scheiben von Platten abzutrennen.[70][71] Es weist große Ähnlichkeit auf mit dem Längs-Profildrehen und dem Längs-Einstech-Profildrehen.[72]
- 3.2.1.2.5 Das Quer-Runddrehen ist eine selten angewandte Variante, bei der die Vorschubbewegung senkrecht zur Drehachse liegt und das Werkzeug mindestens so breit ist wie die erzeugte Fläche.[73][74][75]
-
Längs-Runddrehen
-
Breitschlicht-Runddrehen
-
Schäldrehen
-
Längs-Abstechrunddrehen
-
Quer-Runddrehen
Schraubdrehen[Bearbeiten | Quelltext bearbeiten]

Das Schraubdrehen mit der Ordnungsnummer 3.2.1.3 dient zur Erzeugung von schraubenförmigen Oberflächen mit Profilwerkzeugen. Die zu erzeugende Form ist also zum Teil in der Form des Werkzeugs enthalten. Diese Variante wird zur Herstellung von Gewinden genutzt. Die Steigung des Gewindes entspricht dem Vorschub (mm pro Umdrehung).[76][77] Nach den verwendeten Werkzeugen wird zwischen Gewindedrehen, Gewindestrehlen und Gewindeschneiden unterschieden. Schrauben, Muttern und andere Massenteile mit Gewinden werden heute meist durch das wirtschaftlichere Umformen gefertigt. Das Schraubdrehen wird nur eingesetzt, um Spezialanfertigungen herzustellen, oder für Gewinde, die sich an Werkstücken befinden, die auch ohne Gewinde drehend bearbeitet werden müssten.
- 3.2.1.3.1 Das Gewindedrehen ist ein Schraubdrehen mit Vorschub parallel zur Drehachse mit einfach profiliertem Werkzeug,[78] dem Gewindedrehmeißel beziehungsweise den Gewindedrehplatten.[79] Bei einem Übergang des Werkzeuges wird nur ein Teil der Tiefe des Gewindes erzeugt, es sind also mehrere Übergänge mit einer Zustellung nötig. Es wird unterschieden zwischen Werkzeugen mit Teilprofil, die nur die Tiefe des Gewindes erzeugen können, aber nicht den Außendurchmesser, und Werkzeugen mit Vollprofil, die auch den Außendurchmesser miterzeugen können. Mit dem Gewindedrehen lassen sich links- und rechtsgängige oder auch mehrgängige Gewinde herstellen.[80][81] Die Vorschubbewegung wird bei konventionellen Drehmaschinen mechanisch an die Umdrehung des Werkstückes gebunden. Auf Zug- und Leitspindeldrehmaschinen wird dazu die Leitspindel verwendet. Die Steigung des Gewindes lässt sich über austauschbare Zahnräder einstellen. Auf Revolverdrehautomaten wird stattdessen eine Leitpatrone (Ersatzleitspindel) verwendet. Auf CNC-Maschinen ist der Vorschub dagegen elektronisch an die Umdrehung des Werkstückes gebunden.[82]

- 3.2.1.3.2 Beim Gewindestrehlen wird ein mehrprofiliger Gewindestrehler verwendet, in dem die Zustellungen im Werkzeug integriert sind. Es ist daher nur noch ein einziger Übergang nötig. Die Vorschubbewegung läuft dabei ebenfalls parallel zur Drehachse.[83] Beim Gewindestrehlen sind somit mehrere Profile gleichzeitig im Einsatz. Bei Gewindestrehlern wird zwischen Flach- und Rundgewindestrehlern unterschieden. Letzterer ist selbst als Gewinde ausgeführt, um das zu erzeugende Gewinde nicht zu zerstören. Er wird bevorzugt für die Fertigung von Innengewinden eingesetzt. Für die Herstellung eines linksgängigen Gewindes muss ein Strehler mit einem rechtsgängigen Gewinde genutzt werden und umgekehrt.[84][85]

- 3.2.1.3.3 Das Gewindeschneiden nutzt ein Gewindeschneideisen für die manuelle Fertigung oder einen Gewindeschneidkopf bei CNC-Maschinen, der sich parallel zur Drehachse bewegt. Die Werkzeuge verfügen über mehrere Schneiden, die radial über den Umfang verteilt sind. Meist wird es mit stehendem Werkstück und drehendem Werkzeug durchgeführt. Das Gewindeschneiden ähnelt von seiner Kinematik dem Schraubräumen.[86][87][88][89]
- 3.2.1.3.4 Das Kegelgewindedrehen ist ein neueres Verfahren mit Vorschub schräg zur Drehachse und mit einem Gewindedrehwerkzeug zur Herstellung von Kegelgewinden.[90]
- 3.2.1.3.5 Das Spiraldrehen ist mit dem Quer-Plandrehen verwandt und hat ebenfalls eine Vorschubbewegung, die senkrecht zur Drehachse verläuft. Auf der Stirnseite des Werkstückes wird mittels eines profilierten Drehmeißels eine spiralförmige Oberfläche erzeugt. Diese Oberfläche kann eine Nut oder eine Erhebung aufweisen. Der Vorschub je Umdrehung entspricht der Steigung der Spirale.[91]
-
Gewindedrehen: Links mit Teilprofilwerkzeug, rechts mit Vollprofil
-
Gewindestrehlen: Vergleich der Werkzeuggeometrie zum fertigen Gewinde
Wälzdrehen[Bearbeiten | Quelltext bearbeiten]
Das Wälzdrehen hat die Ordnungsnummer 3.2.1.4 und dient zur Fertigung von rotationssymmetrischen Wälzflächen. Dazu zählen typischerweise Verzahnungen. Beim Wälzdrehen wird mit dem Werkzeug eine Wälzbewegung durchgeführt, die der Vorschubbewegung überlagert ist. Verzahnungen, die nicht rotationssymmetrisch sind, wie Zahnstangen, lassen sich mit dem Wälzfräsen, Wälzhobeln oder Wälzstoßen erzeugen.[92]
Profildrehen[Bearbeiten | Quelltext bearbeiten]


Beim Profildrehen ist die zu erzeugende Form in der Form des Werkzeuges als Negativ enthalten. Es trägt die Ordnungsnummer 3.2.1.5 und dient zur Herstellung von rotationssymmetrischen Formen. Die Werkzeuge sind meist Sonderanfertigungen, bei denen in ein Werkzeug aus Schnellarbeitsstahl oder Hartmetall die gewünschte Form eingeschliffen wird. Härtere Schneidstoffe lassen sich nur schlecht schleifen. Eine Ausnahme sind die genormten Werkzeuge für Nuten, Freistiche oder runde Profile, sowie die Einstiche für Dichtungsringe oder Sicherungsringe.[93]
Das Profildrehen ist sehr produktiv und weist niedrige Bearbeitungszeiten auch für kompliziertere Formen auf. Dafür sind die Werkzeuge im Allgemeinen teurer.[94]
Es wird unterschieden zwischen Längs- und Quer-Profildrehen sowie verschiedenen Ein- und Abstechverfahren:
- 3.2.1.5.1 Beim Längs-Profildrehen werden Werkzeuge verwendet, deren Schneiden mindestens so breit sind wie die herzustellende Form. Diese werden parallel zur Drehachse bewegt.[95]
- 3.2.1.5.2 Das Längs-Profileinstechdrehen ist ein Sonderfall des Längs-Profildrehens, bei dem mit dem Werkzeug auf der Stirnseite des Werkstücks eingestochen wird, um eine ringförmige Nut zu erzeugen. Die Schneide muss jedoch nicht mindestens so breit sein wie die erzeugte Form.[96]
- 3.2.1.5.3 Das Längs-Profilabstechdrehen ist eine Variante des Längs-Abstechdrehens mit einem Profilwerkzeug, mit dem zugleich das Werkstück abgestochen und ein Profil erzeugt wird.[97]
- 3.2.1.5.4 Das Quer-Profildrehen entspricht dem Längs-Profildrehen, nur liegt stattdessen die Vorschubrichtung senkrecht zur Drehachse.[98] Bei Spanungsbreiten ab 15 mm bis 30 mm beginnen die Werkzeug zu rattern.[99][100]
- 3.2.1.5.5 Das Quer-Profileinstechdrehen entspricht dem Quer-Runddrehen mit einem Profilwerkzeug.[101]
- 3.2.1.5.6 Beim Quer-Profilabstechdrehen wird das Werkstück abgestochen wie beim Quer-Abstechdrehen und zugleich ein Profil erzeugt wie beim Quer-Profildrehen oder Querprofileinstechdrehen.[102][103]
-
Längs-Profildrehen
-
Längs-Profileinstechdrehen
-
Längs-Profilabstechdrehen
-
Quer-Profildrehen
-
Quer-Profileinstechdrehen
-
Quer-Profilabstechdrehen
Formdrehen[Bearbeiten | Quelltext bearbeiten]

Beim Formdrehen werden beliebige Formen erzeugt wie zum Beispiel Kugelköpfe oder Kegel. Diese Formen werden über die Vorschubbewegung des Werkzeuges erzeugt. Unterschieden wird nach der Art der Bewegungserzeugung in Freiform-, Nachform- (Kopier-), kinematisches und NC-Formdrehen. Das Formdrehen trägt die Ordnungsnummer 3.2.1.6.
- 3.2.1.6.1 Beim Freiformdrehen wird die Vorschubbewegung von Hand erzeugt. Dies kann an konventionellen Drehmaschinen mittels Handrädern geschehen oder ohne Hilfsmittel. Laut DIN 8589 zählt hierzu ausdrücklich das Drechseln, mit dem vor allem Holz bearbeitet wird.[104][105]
- 3.2.1.6.2 Beim Nachformdrehen wird die Vorschubbewegung über ein Bezugsprofil erzeugt.[106] Dabei kann es sich um eine Schablone, ein zweidimensionales Bezugsformstück oder ein Meisterstück handeln. Früher wurde es als Kopierdrehen bezeichnet. Als Weiterentwicklung können mit elektrischen Steuerungen einmal abgefahrene Wege gespeichert werden, was als Teach-in bezeichnet wird.[107]
- 3.2.1.6.3 Beim kinematischen Formdrehen wird die Vorschubbewegung über ein mechanisches Getriebe gesteuert.[108] Diese Variante wurde vor Entwicklung der CNC-Steuerung (computerized numerical control) zur Erzeugung von Kugelköpfen genutzt.[109]
- 3.2.1.6.4 Beim NC-Formdrehen werden die beiden Vorschubachsen (längs und quer zur Drehachse) durch zwei separate Motoren angetrieben, die durch eine numerische Steuerung (engl. numerical control, NC) gesteuert werden. Heute wird meist die Variante der CNC-Steuerung eingesetzt. Diese Variante zählt spätestens seit den 1980ern zum Stand der Technik.[110][111]
-
Nachformdrehen
-
NC-Formdrehen
-
Ein Koppelgetriebe. Im Punkt E könnte ein Werkzeug angebracht werden.
-
Unrunddrehen
Eine in der DIN 8589 nicht genannte Variante des Formdrehens ist das Unrunddrehen, mit dem beispielsweise ein Unrund oder ein Sechskant für Schrauben oder Muttern erzeugt werden kann. Das Werkzeug bewegt sich dabei periodisch und an die Werkstückumdrehung gekoppelt auf das Werkstück zu und wieder weg.[112][113][114] Ein weiteres Unrunddrehverfahren, welches keine hochdynamischen linearen Werkzeugbewegungen benötigt, nutzt zwei gekoppelte Spindeln für eine wirtschaftliche Bearbeitung von unrunden Konturen.[115] Als Beispiel sei das von vielen Werkzeugmaschinen Herstellern, als Polygondrehen bezeichnete Verfahren, zum herstellen von Mehrkanten genannt. Zum Unrunddrehen zählt auch das Ovaldrehen, das in vorindustrieller Zeit häufig im Kunsthandwerk eingesetzt wurde.
Innen- und Außendrehen[Bearbeiten | Quelltext bearbeiten]
Je nachdem, wie die Bearbeitungsstelle am Werkstück liegt, spricht man von Außendrehen oder Innendrehen. Beim Außendrehen werden die Außenflächen bearbeitet, beim Innendrehen Flächen, die in einer Bohrung liegen. Die englische Bezeichnung turning bezieht sich üblicherweise nur auf das Außendrehen; das Innendrehen wird als boring bezeichnet.
Das Innendrehen weist gegenüber dem konventionellen Außendrehen einige Besonderheiten auf. Während die zu bearbeitende Fläche bei der Außenbearbeitung vom Werkzeug weggebogen ist, ist sie bei der Innenbearbeitung zu ihm hingebogen. Daraus resultiert ein größerer Scherwinkel, aus dem eine größere Zerspankraft folgt. Da die verwendeten Werkzeuge meist sehr lang und auskragend sind, kommt es dabei leichter zu Schwingungen und Durchbiegungen. Dies führt zu schlechteren Oberflächenqualitäten und Maßgenauigkeiten. Der Abtransport der Späne ist ebenfalls problematisch. Normalerweise wird er mit dem Kühlschmiermittel, das unter hohem Druck in die Bohrung eingebracht wird, herausgespült. Das BTA-Bohren verwendet eine ähnliche Technik zum Spanabtransport.[116]
Schruppen und Schlichten[Bearbeiten | Quelltext bearbeiten]
Wie bei den anderen spanenden Fertigungsverfahren, kann man auch beim Drehen zwischen dem Schruppen (Grobbearbeitung) und einem Schlichten (Feinbearbeitung) unterscheiden. Beim Schruppen wird deutlich mehr Volumen pro Zeit als beim Schlichten zerspant und folglich mit hohen Schnitttiefen und Vorschüben gearbeitet. Die Bearbeitungskräfte sind dabei hoch, die erreichte Genauigkeit und Oberflächenqualität spielen eine untergeordnete Rolle. Das Drehteil wird hierbei annähernd auf Maß gebracht. Beim anschließenden Schlichten dagegen wird das gewünschte Maß des Fertigteils erreicht. Die Bearbeitungskräfte sind geringer, da die Vorschübe und Schnitttiefen geringer sind. Die Anforderungen an Maßhaltigkeit und Oberflächenqualität sind jedoch höher.[117]
-
Schruppen von Aluminium
-
Schlichten (Man beachte die veränderte Spanform und -dicke)
Kegeldrehen[Bearbeiten | Quelltext bearbeiten]
Beim Kegeldrehen werden Formen erzeugt, die denen eines Kegels oder Kegelstumpfes entsprechen. Häufig wird es zur Herstellung konischer Wellen angewandt. Neben dem allgemeinen Formdrehen gibt es zwei Möglichkeiten, die Form durch Längsdrehen zu erzeugen: Schrägstellen des Oberschlittens am Werkzeughalter der Maschine und seitliches Versetzen des Reitstocks beim Drehen zwischen Spitzen.
Das Schrägstellen des Oberschlittens geschieht zunächst grob mittels einer Skala. Die Feineinstellung erfolgt dann mit Lehrkegeln und Messuhr. Diese Variante wird eingesetzt für kurze Kegel mit großem Öffnungswinkel.
Wenn der Reitstock seitlich versetzt wird, steht das gesamte Werkstück schräg zu den Vorschubachsen des Werkzeughalters. Wenn dieser wie beim gewöhnlichen Längsdrehen bewegt wird, entsteht automatisch ein Kegel.[118]
Hartdrehen[Bearbeiten | Quelltext bearbeiten]
Das Hartdrehen ist eine Variante der Hartzerspanung, mit der auch Werkstoffe mit einer Härte von mehr als 54 HRC bearbeitet werden können. Traditionell war dies nur durch Schleifen und Läppen möglich. Durch die Entwicklung sogenannter superharter Schneidstoffe (Werkzeugwerkstoffe) wie kubischem Bornitrid wurde es möglich, derart harte Werkstoffe auch durch Drehen, Bohren oder Fräsen zu bearbeiten, was zu zahlreichen Vorteilen führt. Das Hartdrehen ist grundsätzlich auch mit Siliziumnitrid-Schneidkeramik und beschichtetem Hartmetall möglich, die Werkzeuge verschleißen jedoch schneller.
Die Werkstücke können direkt im gehärteten Zustand bearbeitet werden. Damit entfallen sowohl das Weichglühen als auch das Schleifen, was zu kürzeren Durchlaufzeiten führt. Außerdem kann auf die teuren Schleifmaschinen verzichtet werden, indem die Bearbeitung auf den günstigeren Drehmaschinen stattfindet. Des Weiteren ist Hartdrehen wirtschaftlicher, da pro Zeit ein größeres Werkstoffvolumen entfernt werden kann (größeres Zeitspanvolumen). Da beim Hartdrehen die Werkstückform durch die Bewegung des Werkzeuges gesteuert wird, ist es auch flexibler als das Schleifen, bei dem die Werkstückform meist teilweise im Werkzeug enthalten ist. Wegen der größeren Spanungsdicke benötigt das Hartdrehen weniger Energie und lässt sich ohne oder mit nur wenig Kühlschmierstoff einsetzen, was als Trockenbearbeitung beziehungsweise Minimalmengenkühlschmierung bezeichnet wird. Das Hartdrehen wird bei komplizierteren Formen angewandt, wogegen lange gerade Wellen wirtschaftlicher durch Schleifen zu bearbeiten sind, weil die breiteren Schleifscheiben in diesem Fall kürzere Bearbeitungszeiten aufweisen.
Typische Werte beim Hartdrehen sind Schnitttiefen von ap = 0,01 mm bis 0,3 mm, Vorschübe von f = 0,01 mm bis 0,14 mm und Schnittgeschwindigkeiten von vc = 120 m/min bis 220 m/min. Sie liegen somit alle deutlich unter denen des konventionellen Drehens. Anwendungsfelder für das Hartdrehen sind Lagersitze von Wellen und Rädern, Wälzlagerringe und Walzen.[119]
HSC-Drehen[Bearbeiten | Quelltext bearbeiten]
Das Hochgeschwindigkeitsdrehen oder kurz HSC-Drehen (von High Speed Cutting = Hochgeschwindigkeitszerspanung) ist eine Variante des Drehens mit besonders hohen Schnittgeschwindigkeiten. Eine klare Abgrenzung gibt es nicht, im Falle von Stahl wird bei Schnittgeschwindigkeiten ab 500 m/min von HSC-Drehen gesprochen, bei Aluminium erst ab 2000 m/min. Höhere Schnittgeschwindigkeiten wirken sich günstig auf die Produktivität aus. Sie führen zudem zu abnehmenden Schnittkräften, weshalb sich die Hochgeschwindigkeitsbearbeitung auch für filigrane Bauteile eignet. Beim Drehen führen die hohen Drehzahlen zu hohen Fliehkräften, was besondere Maschinen erfordert. Außerdem müssen speziell darauf ausgelegte Spannmittel genutzt werden. Mit den meisten am Markt erhältlichen Maschinen (Stand 2014) sind nur die geringeren Schnittgeschwindigkeiten des HSC-Drehens erreichbar. Wegen der hohen Drehzahlen geht von wegfliegenden Teilen wie zum Beispiel Spänen eine deutlich erhöhte Gefährdung für Menschen und Maschinen aus, was besondere Sicherheitsvorkehrungen erfordert.[120]
Fein- und Präzisionsdrehen[Bearbeiten | Quelltext bearbeiten]
Nach der erreichbaren Genauigkeiten wird das Drehen eingeteilt in „konventionelles Drehen“ (manchmal auch im Sinne von „Drehen ohne NC-Steuerung“), Feindrehen oder Präzisonsdrehen mit erreichbaren ISO-Toleranzen von IT6 bis IT7, Hochpräzisionsdrehen (IT6 bis IT2) und Ultrapräzisionsdrehen (IT1 bis IT01). Der Vorschub wird dabei reduziert: Beim Präzisionsdrehen beträgt er etwa 100 µm pro Umdrehung, beim Hochpräzisionsdrehen 10 µm und bei der Ultrapräzisionsbearbeitung nur wenige Mikrometer. Die Herstellung optischer Geräte und Instrumente (vor allem Linsen und Spiegel) gilt als Triebkraft für die Verbesserung der Genauigkeiten. Für die Ultrapräzisonsbearbeitung sind Diamantwerkzeuge typisch, wegen ihres geringen Verschleißes. Genutzt werden spezielle Ultrapräzisionsdrehmaschinen. Diese erreichen durch besondere konstruktive Maßnahmen hohe Wiederholgenauigkeiten. Dazu zählen eine Hauptspindel mit hoher Steifheit, hydrostatische oder hydrodynamische Lagerung der Spindel, besondere Fundamente und Dämpfungssysteme zur Schwingungsreduzierung.
Als Werkstoffe gelten für das Präzisionsdrehen Stahl und Nichteisenmetalle als besonders geeignet. Beim Ultrapräzisonsdrehen werden NE-Metalle, plastische und monokristalline Werkstoffe bearbeitet. Das Präzisionsdrehen wird auch in Form des Hartdrehens eingesetzt für gehärtete Werkstoffe als Ersatz für das Schleifen. Die Präzisionsvarianten des Drehens werden genutzt für Werkstücke aus der Feinmechanik, Automobilindustrie, Optik, Medizintechnik, Kunststoff- und Leichtmetallbearbeitung, Elektrotechnik, für Uhren und die Schmuckherstellung. Es können asphärische Linsen und sogar nicht-rotationssymmetrische Linsen hergestellt werden. Für Letztere werden besonders dynamische Vorschubantriebe benötigt, die meist als Lineardirektantrieb ausgeführt sind. Bauteile aus gehärtetem Stahl sind Pumpenkolben, Synchronringe, Einspritzdüsen, Lagerbuchsen, Normalien, Hydraulikkolben, Getriebewellen und Kugellagerkomponenten. Aus Leichtmetallen werden Gehäuse für Benzinpumpen, Wasserpumpen und Zündverteiler gefertigt sowie Lagerdeckel für Schrittmotoren, Flansche für Elektromotoren, Radnaben und Computerteile. Für die Feinmechanik werden optische Fassungen gefertigt sowie Linsengehäuse, Mikroskopkomponenten, Kopierwalzen, Fotobauteile, Videokopftrommeln und Festplattenteile. Aus Kunststoff werden Gehäuse für Stifte, Dichtungen, Lagerkäfige und Wasserzählergehäuse hergestellt.[121]
Spanbildung[Bearbeiten | Quelltext bearbeiten]

Die Entstehung der Späne ist für das Drehen besonders gut erforscht. Zu Beginn der Bearbeitung wird der Werkstoff durch das Werkzeug angestaucht, bis die Festigkeit überschritten ist. Bei harten, spröden Werkstoffen wie Gusseisen oder Keramiken bilden sich Risse, die sich ausbreiten, bis sich Brocken vom Werkstück lösen und der Vorgang erneut beginnt. Die meisten Metalle, insbesondere Stahl, sind duktil, sie lassen sich verformen. Es bildet sich ein langer Span aus, der über das Werkzeug abläuft. Die Spanbildung ist kontinuierlich, was zu geringen Schwankungen der Schnittkraft und somit zu langen Standzeiten führt. Die Späne können sich jedoch verfangen und Mensch und Maschine gefährden. Um dies zu vermeiden, werden sogenannte Spanbrecher genutzt. Dies sind Kanten an den Werkzeugen, gegen die die Späne laufen und brechen. Die Länge der Späne hängt von zahlreichen Einflüssen ab. Die beiden wichtigsten sind der Werkstoff und der Vorschub. Mit steigendem Vorschub werden die Späne kürzer und somit günstiger.[122]
Werkzeuge und Schneidstoffe[Bearbeiten | Quelltext bearbeiten]

Die Werkzeuge beim Drehen werden meist als Drehmeißel bezeichnet. Manchmal werden damit jedoch nur Werkzeuge bezeichnet, die vollständig aus Schnellarbeitsstahl bestehen oder eine aufgelötete Schneide aus dem teureren, aber härteren und verschleißfesteren Hartmetall haben. Wenn die Schneiden verschlissen sind, werden sie nachgeschliffen. In der industriellen Praxis werden heute jedoch meist Klemmhalter genutzt, in denen eine Wendeschneidplatte als Schneide fungiert. Ist die Kante der Platte verschlissen, wird jene gedreht oder gewendet, um neue Kanten zu nutzen, und schließlich durch eine neue Platte ersetzt. Nachgeschliffen werden die Platten nicht mehr.
Es gibt spezielle Werkzeuge für Außen- oder Innenbearbeitung, Schruppen und Schlichten, Profilwerkzeuge, die eine zu erzeugende Werkstückform als Negativ enthalten (darunter Werkzeuge zum Gewindedrehen), sowie Ein- und Abstechwerkzeuge und Kopierdrehmeißel, die sich für das Nachform- oder NC-Drehen eignen.
-
Drehmeißel aus HSS oder Hartmetall
-
Klemmhalter für Wendeschneidplatten
-
Wendeschneidplatten
Die Werkstoffe, aus denen die Schneiden bestehen, werden in der Zerspantechnik als Schneidstoff bezeichnet. Industrieller Standard ist das Hartmetall, mit dem höhere Schnittgeschwindigkeiten und somit niedrigere Bearbeitungszeiten möglich sind als mit dem herkömmlichen Schnellarbeitsstahl (HSS). Beim Drehen kann jedoch grundsätzlich die gesamte Palette der bekannten Schneidstoffe zum Einsatz kommen. Für Werkstoffe, die nur schwer zerspanbar sind, kommen auch Schneidkeramiken und kubisches Bornitrid zum Einsatz. Werkzeuge aus Diamant eignen sich wegen der hohen Verschleißfestigkeit und der erreichbaren Genauigkeiten vor allem für die Bearbeitung von Aluminiumlegierungen und Kupferlegierungen. Für Stahl sind sie jedoch ungeeignet, da sie sich bei den hohen auftretenden Temperaturen in Graphit umwandeln.[123]
Maschinen[Bearbeiten | Quelltext bearbeiten]

Die zum Drehen geeigneten Maschinen sind hauptsächlich Drehmaschinen sowie Bearbeitungszentren, die sich sowohl zum Drehen als auch zum Fräsen eignen. Etwa ein Drittel des Produktionswertes der spanenden Werkzeugmaschinen entfällt auf Drehmaschinen. Sie werden zwingend für das Drehen benötigt – eine manuelle Variante wie beim Bohren, Sägen oder Schleifen gibt es nicht. Die Drehmaschine ist die wohl variantenreichste Werkzeugmaschine: Es gibt sie in zahlreichen Automatisierungsgraden, Größen und verschiedenen konstruktiven Konzepten. Manche sind speziell für ein eng umrissenes Werkstückspektrum ausgelegt, wie die Walzendrehmaschine (zur Herstellung von Walzen für Walzwerke), Radsatzdrehmaschinen für die Räder von Schienenfahrzeugen oder die Kurbelwellendrehmaschine.
Drehmaschinen bestehen aus mehreren Komponenten: einem Antrieb, Führungen und Lagerungen, die die Bewegung der Werkzeuge und Werkstücke ermöglichen, sowie der Steuerung und dem Gestell, an dem sämtliche Komponenten befestigt sind. Dazu zählt auch der Werkzeugschlitten, in dem das Werkzeug festgespannt ist, der üblicherweise über einen eigenen Antrieb verfügt. Als Zusatzeinrichtungen gibt es zum Abstützen langer Werkstücke Lünetten und den Reitstock.
Die einfachste Form der Drehmaschine ist die Universaldrehmaschine. Mit ihr sind fast sämtliche Drehverfahren möglich, einschließlich des Ein- und Abstechens und des Gewindedrehens. Sie eignet sich für eine große Bandbreite an Werkstückgrößen und -formen, ist aber nur wenig produktiv und eignet sich daher nur für Einzelteile und Kleinserien. Universalmaschinen machen den Großteil aller Drehmaschinen aus und finden sich insbesondere in Reparaturwerkstätten. Die CNC-Drehmaschine verfügt über eine CNC-Steuerung, die das Werkzeug auf programmierte Bahnen lenkt, somit für kleinere und mittelgroße Serien geeignet ist und auch die Fertigung komplizierter Formen ermöglicht. Wenn zusätzlich statt des Werkzeugschlittens ein Werkzeugrevolver vorhanden ist, in dem mehrere Werkzeuge eingespannt sind, spricht man von Drehzentren. Bei ihnen sind die Werkzeugwechselzeiten deutlich geringer, weshalb sie auch für mittlere bis große Serien von Werkstücken geeignet sind. Drehautomaten eignen sich für die Großserien- und Massenfertigung, da sie über mehrere Werkzeugschlitten oder -revolver verfügen, die gleichzeitig im Eingriff sind. Sie sind somit besonders produktiv, das Umrüsten auf ein anderes Produkt dauert jedoch relativ lange.
Für besonders große und schwere Werkstücke gibt es sogenannte Karusselldrehmaschinen. Für die Präzisionsbearbeitung von Teilen für die Feinmechanik gibt es Feindrehmaschinen. Für das Hochgeschwindigkeitsdrehen existieren spezielle Maschinen, die für die hohen Fliehkräfte ausgelegt sind.[124]
Spannmittel[Bearbeiten | Quelltext bearbeiten]
Allgemein dienen Spannmittel dazu, Werkzeuge oder Werkstücke während der Bearbeitung zu fixieren. Aus der Besonderheit des Drehens mit seinen meist rotierenden, runden Werkstücken statt der meist stehenden, prismatischen Werkstücke ergeben sich einige Besonderheiten bei den Spannmitteln.
Die Werkzeuge selbst müssen in der Drehmaschine eingespannt werden. Dafür wurden verschiedene Schnittstellen entwickelt. Die Schäfte der Drehmeißel können entweder rund oder eckig sein. Sie können direkt in den Werkzeugschlitten eingespannt werden oder in einen Werkzeugspeicher, der mehrere Werkzeuge enthält und schnell das Bearbeitungswerkzeug austauschen kann. Zum Festspannen beim automatischen Werkzeugwechsel dient ein Hydrauliksystem.[125]
Für die Werkstücke gibt es zahlreiche Spannmittel, die speziell für Drehteile ausgelegt sind. Durch die Rotation der Drehteile ergeben sich insbesondere bei hohen Drehzahlen Fliehkräfte, die die sichere Einspannung der Werkstücke gefährden. Standard-Spannmittel beim Drehen sind die Spannfutter. Diese eignen sich allgemein für rotierende Teile und werden neben dem Drehen (Drehfutter) auch beim Bohren oder Fräsen genutzt (Bohr- bzw. Fräsfutter). Sie bestehen aus zwei bis acht Spannbacken, die am Umfang des Werkstücks verteilt die Spannkräfte aufbringen. Bei Spannfuttern werden sämtliche Spannbacken gleichzeitig bewegt. Sie eignen sich für hohle und massive Werkstücke, die hier auch als Futterteil bezeichnet werden. Drehfutter werden entweder manuell (Handspannfutter) oder hydraulisch, elektrisch oder pneumatisch betätigt (Kraftspannfutter). Den Spannfuttern ähnlich sind die Planscheiben, bei denen sich die Spannbacken einzeln verschieben lassen. Das Einspannen dauert somit länger, sie eignen sich jedoch auch für nicht kreisrunde Werkstücke. Für dünnwandige, hohle Drehteile, die sich auf Spannfuttern verformen würden, eignen sich Spanndorne. Diese bringen die Spannkraft auf der gesamten Innenfläche gleichmäßig auf. Spannzangen eignen sich für Drehteile mit kleinerem Durchmesser in der automatisierten Fertigung, beispielsweise auf Drehautomaten. Die Rüstzeiten sind sehr niedrig, allerdings auch die Spannkräfte, sodass sie sich nicht für große Drehzahlen eignen. Außerdem liegt der Spannbereich einer Spannzange nur bei etwa 0,3 mm im Durchmesser; nur Werkstücke, deren Größe innerhalb dieses Bereichs liegt, können gespannt werden. Sollen Werkstücke unterschiedlichster Größe bearbeitet werden, werden dafür folglich eine Vielzahl unterschiedlich großer Spannzangen benötigt.
-
Drehfutter mit sechs Backen
-
Segmentspanndorn
-
Verschiedene Spannzangen
-
Zentrierspitzen
Drehfutter, Planscheiben, Spanndorne und -zangen spannen die Drehteile auf dem Umfang. Für längere Werkstücke eignen sich Stirnmitnehmer, Zentrierspitzen und Drehgreifer. Diese spannen auf den Stirnflächen der Werkstücke. Damit wird einerseits die gesamte Länge der Werkstücke für die Bearbeitung zugänglich, wodurch das Umspannen für die Rückseitenbearbeitung entfallen kann, was auch die Rundlaufgenauigkeit erhöht. Andererseits werden die beiden Enden der Werkstücke abgestützt, sodass sie sich weniger verbiegen. Besonders lange Werkstücke werden mittig zusätzlich mit einer Lünette abgestützt.[126][127]
Drehparameter[Bearbeiten | Quelltext bearbeiten]
Die Verfahrensparameter sind die Schnittgeschwindigkeit in m/min, der Vorschub in mm/U, die Schnitttiefe (auch Zustellung genannt) und die verschiedenen Winkel und Radien an der Schneide des Drehmeißels. Bei gegebenen Werkstückdurchmesser ergibt sich die Schnittgeschwindigkeit aus der Drehzahl. Bei CNC-Drehmaschinen lässt sich die Schnittgeschwindigkeit einstellen, woraus die Steuerung die nötige Drehzahl berechnet.[128] Darüber hinaus können bei CNC-Steuerungen Programme für einander ähnliche Werkstücke mittels Variablen- und Parameterprogrammierung erstellt werden.
Die Verfahrensparameter führen während der Bearbeitung zu einer bestimmten Zerspankraft und Temperatur am Werkzeug, einem Leistungsumsatz, Schwingungen und akustischen Emissionen (Lärm) und Spanformen. Nach der Bearbeitung machen sie sich am Werkstück bemerkbar als erreichte Maße und Oberflächenqualitäten sowie als Werkzeugverschleiß und als entstandene Kosten. Die wichtigsten Prozessparameter sind, wie bei den meisten Verfahren der Zerspantechnik, der Vorschub, die Schnitttiefe und die Schnittgeschwindigkeit.
In der Fertigungstechnik gilt grundsätzlich, dass die vom Konstrukteur verlangten Spezifikationen (Maße, Rauheiten etc.) möglichst wirtschaftlich zu erreichen sind. Da mit der Genauigkeit auch die Kosten zunehmen, gilt: Die Bearbeitung sollte nur so genau sein wie nötig. Eine wichtige technische Produktivitätskennzahl ist das Zeitspanvolumen , das pro Zeitspanne abgetrennte Werkstoffvolumen. Es lässt sich berechnen aus der Schnittgeschwindigkeit , dem Vorschub und der Schnitttiefe zu
- .
Die Werte sollten also möglichst groß sein. Die einzelnen Werte sind aber nach oben technisch begrenzt, da sie zu höherem Verschleiß sowie zu höheren Kräften und Temperaturen führen, teils auch zu geringeren möglichen Genauigkeiten.[129][130]
Schnittgeschwindigkeit und Drehzahl[Bearbeiten | Quelltext bearbeiten]
Die Wahl der Schnittgeschwindigkeit ist von verschiedenen Faktoren abhängig. Diese sind der Werkstoff des Werkstücks, der Werkstoff des Werkzeugs (Schneidstoff), das Bearbeitungsverfahren (Schruppen, Schlichten, Feinschlichten), das Drehverfahren, die geforderte Oberflächengüte des Werkstücks und der Kühlschmierstoff. Die Drehzahl ist abhängig von Schnittgeschwindigkeit und Durchmesser des Werkstücks und mit der Formel errechenbar.
Eine Erhöhung der Schnittgeschwindigkeit erhöht das Zeitspanvolumen. Sie ist aber bei gegebenem Schneidstoff auch die Haupteinflussgröße auf den Werkzeugverschleiß (siehe Verschleiß (Spanen)). Im Allgemeinen ist der Verschleiß umso größer, je höher die Schnittgeschwindigkeit ist. Bei niedrigen Geschwindigkeiten kann es zur Aufbauschneidenbildung kommen. Dabei bleibt ein Teil des Spanes auf der Schneide kleben, was zu erhöhtem Verschleiß und geringen Oberflächenqualitäten führt. Eine Erhöhung der Schnittgeschwindigkeit führt auch zu langsam fallenden Schnittkräften, was beim Hochgeschwindigkeitsdrehen genutzt wird. Die realisierbaren Schnittgeschwindigkeiten fallen meist umso höher aus, je verschleißfester der verwendete Schneidstoff ist.
Richtwerte für die Schnittgeschwindigkeit sind Tabellenbüchern oder den Datenblättern der Drehwerkzeuge zu entnehmen. Eine Optimierung kann mit der Taylor-Geraden erreicht werden.[131]
Vorschub und Schnitttiefe[Bearbeiten | Quelltext bearbeiten]

Der Vorschub f wird in Millimeter pro Umdrehung angegeben. Er sollte beim Schruppen aus wirtschaftlichen Gründen so groß wie möglich eingestellt werden. Eine Erhöhung des Vorschubs erhöht auch die Zerspankraft, die auf das Werkzeug wirkt. Diese kann zu Schwingungen führen und damit zu abnehmenden Genauigkeiten. Eine höhere Kraft führt auch zu einem höheren Leistungsbedarf (Leistung = Kraft × Geschwindigkeit). Da die Leistung des Antriebes begrenzt ist, sind bei gegebener Schnittgeschwindigkeit auch der Vorschub und die Schnitttiefe begrenzt. Für Letztere gilt das gleiche wie für den Vorschub, eine Verdopplung des Vorschubes erhöht die Schnittkraft um weniger als das Doppelte, bei der Schnitttiefe verdoppelt sie sich. Einen mathematischen Zusammenhang bietet die Kienzle-Formel. Beim Schlichten (Fertigdrehen) wird zu Gunsten einer höheren Oberflächenqualität der Vorschub gegenüber dem Schruppvorgang vermindert und die Schnittgeschwindigkeit erhöht. Je geringer der Spitzenradius des Drehwerkzeugs ist, desto geringer muss die Vorschubgeschwindigkeit für eine gleichbleibende Oberflächengüte eingestellt werden. Die Rauheit liegt theoretisch bei
- .
Daneben ist eine Mindestspanungsdicke zu erreichen, die vom Vorschub abhängt. Das Verhältnis von Mindestspanungsdicke zu Schneidkantenradius beträgt beim Drehen zwischen 0,25 und 1,125.[132]
Die Schnitttiefe ist beim Runddrehen von der Zustellung des Drehwerkzeuges, beim Einstechdrehen von der Breite der Schneide abhängig. Die Schnitttiefe sollte bei der Schruppbearbeitung mindestens der Größe des Schneidplattenradius entsprechen. Eine geringere Schnitttiefe führt zu einem höheren Verschleiß der Werkzeugschneide im Bereich des Schneidplattenradius. In der Praxis beträgt das Verhältnis der Schnitttiefe zum Vorschub etwa 10:1, kann jedoch je nach Spindelleistung, Spannsituation des Bauteils, Werkstoff, Werkzeuggeometrie und Schneidstoff davon abweichen. Beim Schlichten entspricht die Schnitttiefe der Hälfte des Aufmaßes.[133]
Winkel und Radien an der Werkzeugschneide[Bearbeiten | Quelltext bearbeiten]

An den Schneiden der Zerspanungswerkzeuge gibt es zahlreiche Winkel und Radien, die vor allem die Verteilung und Richtung der Zerspankraft und den Verschleiß beeinflussen. Die Radien beeinflussen außerdem noch die erreichbare Genauigkeit.[134]
Richtwerte[Bearbeiten | Quelltext bearbeiten]
Richtwerte sind in Tabellen aufgeführte Werte, die eine Orientierung erlauben, in welchen Bereichen mit wirtschaftlichen Verfahrensparametern zu rechnen ist. Die folgende Tabelle gibt einen groben Überblick über die in der Praxis genutzten Werte und gilt für das Schruppen. Beim Schlichten werden geringere Schnitttiefen und Vorschübe genutzt und etwas höhere Schnittgeschwindigkeiten sowie andere Schneidstoffsorten. Gut zu erkennen ist, dass die realisierbaren Schnittgeschwindigkeiten umso höher ausfallen, je verschleißfester der Schneidstoff und je geringer die Festigkeit des Werkstoffes ist. (Die Festigkeit von Aluminiumlegierungen ist am geringsten, die von legiertem Stahl am höchsten). Die tatsächlich realisierbaren Werte hängen von der Legierung ab. Zu den hohen Schnittgeschwindigkeiten einer Zeile gehören die niedrigen Vorschübe und Schnitttiefen.[135]
Werkstückwerkstoff | Schnitttiefe ap [mm] |
Vorschub f [mm/U] |
Schneidstoff | Schnittgeschwindigkeit vc [m/min] |
---|---|---|---|---|
Unlegierter Stahl | 2 bis 8 | 0,3 bis 0,6 | beschichtetes Hartmetall | 100 bis 200 |
Legierter Stahl | 2 bis 6 2 bis 10 1,5 bis 6 |
0,3 bis 0,6 0,2 bis 1 0,3 bis 0,45 |
Hartmetall (unbeschichtet) beschichtetes Hartmetall Schneidkeramik |
60 bis 120 120 bis 300 150 bis 700 |
Gusseisen (Grauguss) | 2 bis 6 2 bis 8 2 bis 6 1,5 bis 6 1,5 bis 8 |
0,3 bis 0,6 | Hartmetall (unbeschichtet) beschichtetes Hartmetall beschichtete Cermets Aluminiumoxid-Schneidkeramik Siliciumnitrid-Schneidkeramik |
60 bis 100 100 bis 250 200 bis 300 100 bis 400 200 bis 800 |
Aluminiumlegierungen | 2 bis 6 2 bis 8 1 bis 5 0,5 bis 3 |
0,3 bis 0,6 0,3 bis 0,6 0,1 bis 0,4 0,1 bis 0,2 |
Hartmetall beschichtetes Hartmetall beschichtete Cermets Polykristalliner Diamant |
150 bis 1500 200 bis 2000 220 bis 2200 400 bis 3000 |
Fehler[Bearbeiten | Quelltext bearbeiten]
Beim Drehen können verschiedene Fehler auftreten, die die Werkzeuge oder die Werkstücke betreffen. In der Fachliteratur existieren ausführliche Tabellen mit möglichen Fehlern, deren Ursachen und Abhilfen.
Ein zu hoher Werkzeugverschleiß beispielsweise entsteht meist durch überhöhte Verfahrensparameter für die verwendeten Werkzeuge. Abhilfe schaffen die Verminderung der Parameter oder die Verwendung verschleißfesterer Werkzeuge.
Kammrisse am Werkzeug sind eine Verschleißform, die durch schnelle Temperaturwechsel entsteht. Abhilfe kann eine Verbesserung der Kühlschmiermittelzufuhr sein (mehr oder gezielter) oder das Abstellen des Kühlschmiermittels beim unterbrochenen Schnitt (Trockenbearbeitung), denn auch durch verringerte Kühlung können schnelle Temperaturwechsel vermieden werden.
Geringe Maßgenauigkeiten am Werkstück können durch verschlissene Werkzeuge entstehen, Kratzer am Werkstück durch Späne oder durch Oxidationsverschleiß an der Nebenschneide. Hohe Rauheit am Werkstück entsteht durch hohe Vorschübe oder geringe Spitzenradien am Werkzeug.[136]
Berechnung[Bearbeiten | Quelltext bearbeiten]
Mit den folgenden Gleichungen können die beim Drehen auftretenden Kräfte, Leistungen und die Bearbeitungszeit berechnet werden. Diese Werte werden für die Arbeitsvorbereitung und die Konstruktion der Drehmaschinen benötigt.
Kräfte und Leistungen[Bearbeiten | Quelltext bearbeiten]
Zur Berechnung der Schnittkraft eignet sich beim Drehen die experimentell ermittelte Kienzle-Formel. Für andere Fertigungsverfahren wird sie je nach Verfahren mit einem Korrekturfaktor multipliziert. In Kenntnis der Schnittkraft kann überprüft werden, ob die geplanten Verfahrensparameter auf einer vorhandenen Maschine realisiert werden können, wie groß die Durchbiegung der Werkzeuge ausfällt oder, bei der Konstruktion der Maschinen, wie groß das Drehmoment des Antriebes ausfallen muss beziehungsweise wie stark die Werkzeuge ausgelegt sein müssen.
Die Leistung ergibt sich als Produkt aus der Geschwindigkeit und der Kraft. Die Schnittleistung, die näherungsweise der Gesamtleistung entspricht, ergibt sich als Produkt aus Schnittgeschwindigkeit und Schnittkraft. Mit der Leistung kann ebenfalls überprüft werden, ob die geplanten Verfahrensparameter auf vorhandenen Maschinen realisiert werden können oder wie groß die Leistung der zu konstruierenden Maschinen sein muss.[137]
Hauptzeit[Bearbeiten | Quelltext bearbeiten]
Die Hauptzeit beim Drehen ist die Zeit, während der Späne fallen. Sie lässt sich berechnen. Die Nebenzeit dagegen, während derer Werkzeuge oder Werkstücke gewechselt werden sowie die Werkzeuge verschiedene Verfahrbewegungen durchführen, ohne Späne abzutrennen, hängt von der Maschine ab. In der industriellen Praxis wird die Hauptzeit von CAP-Systemen berechnet, geschätzt oder durch Zeitermittlung (Stoppuhr) bestimmt. Sie wird benötigt für die Kalkulation (Berechnung der entstehenden Kosten), die Maschinenbelegungszeit und die erforderliche Anzahl Maschinen, um eine bestimmte Produktionsmenge innerhalb der gewünschten Zeit fertigen zu können.[138]
Wenn die Verfahrensparameter während der gesamten Bearbeitung konstant sind, ergibt sich die Hauptzeit aus dem abzutrennenden Werkstoffvolumen und dem Zeitspanvolumen zu
Beim Längsdrehen kann die Zeit auch berechnet werden mit
Dabei sind:
- = Anzahl der Schnitte
- = größter Durchmesser
- = Weglänge, den das Werkzeug zurücklegen muss (Werkstücklänge + Bearbeitungszugaben + An- und Überlaufwege für das Werkzeug).
- = Vorschub
- = Schnittgeschwindigkeit
Siehe auch[Bearbeiten | Quelltext bearbeiten]
- Drehräumen – Verfahrenskombination aus Drehen und Räumen
- Liste der spanenden Fertigungsverfahren – Übersicht mit Definitionen sowie zugehörigen Maschinen, Werkzeugen und erreichbaren Genauigkeiten
Literatur[Bearbeiten | Quelltext bearbeiten]
- Internationale Akademie für Produktionstechnik (Hrsg.): Wörterbuch der Fertigungstechnik – Band 2: Trennende Verfahren. 2. Auflage. Springer, 2004, ISBN 3-540-20540-3.
- Uwe Heisel, Fritz Klocke, Eckart Uhlmann, Günter Spur: Handbuch Spanen. 2. Auflage. Hanser, München 2014, ISBN 978-3-446-42826-3.
- Wilfried König, Fritz Klocke: Fertigungsverfahren 1: Drehen, Fräsen, Bohren. 8. Auflage. Springer, Berlin 2008, ISBN 978-3-540-23458-6.
- Berend Denkena, Hans Kurt Tönshoff: Spanen – Grundlagen. 3. Auflage. Springer, Berlin 2011. ISBN 978-3-642-19771-0.
- Heinz Tschätsch: Praxis der Zerspantechnik. Verfahren, Werkzeuge, Berechnung. 11. Auflage. Springer Vieweg, Wiesbaden 2014, ISBN 978-3-658-04922-5.
- Eberhard Pauksch: Zerspantechnik. 12. Auflage. Springer Vieweg, Wiesbaden 2008, ISBN 978-3-8348-0279-8.
- Herbert Schönherr: Spanende Fertigung. Oldenbourg, Berlin 2002, ISBN 978-3-486-25045-9.
- Werner Degner, Hans Lutze, Erhard Smejkal: Spanende Formung. 17. Auflage. Hanser, München 2015, ISBN 978-3-446-44544-4.
- Christian Gottlöber: Zerspanung von Holz und Holzwerkstoffen: Grundlagen – Systematik – Modellierung – Prozessgestaltung. Hanser, München 2014, ISBN 978-3-446-44003-6.
Weblinks[Bearbeiten | Quelltext bearbeiten]
Einzelnachweise[Bearbeiten | Quelltext bearbeiten]
- ↑ Herbert Schönherr: Spanende Fertigung. Oldenbourg, 2002, S. 67.
- ↑ Industrielle Fertigung – Fertigungsverfahren, Mess- und Prüftechnik. Verlag Europa-Lehrmittel, 5. Auflage, 2011, S. 231.
- ↑ Heinz Tschätsch: Praxis der Zerspantechnik. Verfahren, Werkzeuge, Berechnung. 11. Auflage, Springer Vieweg, Wiesbaden 2014, S. 41.
- ↑ Zitiert nach: Uwe Heisel, Fritz Klocke, Eckart Uhlmann, Günter Spur (Hrsg.): Handbuch Spanen. 2. Auflage, Hanser, München 2014, S. 150.
- ↑ Uwe Heisel, Fritz Klocke, Eckart Uhlmann, Günter Spur (Hrsg.): Handbuch Spanen. 2. Auflage, Hanser, München 2014, S. 150.
- ↑ Reinhard Koether, Wolfgang Rau: Fertigungstechnik für Wirtschaftsingenieure. Hanser, 4. Auflage, 2012, S. 146.
- ↑ Fritz Klocke, Wilfried König: Fertigungsverfahren Band 1: Drehen, Fräsen, Bohren. Springer, 8. Auflage, 2008, S. 417.
- ↑ Metalltechnik Fachbildung. Verlag Europa-Lehrmittel, Nourney, 2. Auflage, 1993, S. 80.
- ↑ Alfred Herbert Fritz, Günter Schulze (Hrsg.): Fertigungstechnik. Springer, 9. Auflage, 2010, S. 289.
- ↑ Liang, Shih: Analysis of Machining and Machine Tools. Springer, 2016, S. 4.
Vgl. auch en:Turning und en:Boring (manufacturing). - ↑ Trent, Wright: Metal Cutting. Butterworth Heinemann, 2000, 4. Auflage, S. 9, 12 f.
- ↑ Günter Spur: Produktionstechnik im Wandel. Carl Hanser, München/Wien 1979, S. 36.
- ↑ Günter Spur: Produktionstechnik im Wandel. Carl Hanser, München/Wien 1979, S. 42, 45 f.
- ↑ Günter Spur: Produktionstechnik im Wandel. Carl Hanser, München/Wien 1979, S. 168, 286.
- ↑ Brian Clifford: A brief history of woodturning. In: The Woodturner’s Workshop. Abgerufen am 26. November 2023 (englisch).
- ↑ Gustave Lefèbvre: Le tombeau de Petosiris, Troisième partie: vocabulaire et planches. Institut Français, Kairo 1923, planche X, S. 423 (unten links)archive.org.
- ↑ Günter Spur: Produktionstechnik im Wandel. Carl Hanser, München/Wien 1979, S. 25, 39.
- ↑ Günter Spur: Produktionstechnik im Wandel. Carl Hanser, München/Wien 1979, S. 39.
- ↑ Günter Spur: Produktionstechnik im Wandel. Carl Hanser, München/Wien 1979, S. 39.
- ↑ Günter Spur: Produktionstechnik im Wandel. Carl Hanser, München/Wien 1979, S. 25, 39.
- ↑ Günter Spur: Vom Wandel der industriellen Welt durch Werkzeugmaschinen. Carl Hanser, München/Wien 1991, S. 46.
- ↑ a b c Günter Spur: Vom Wandel der industriellen Welt durch Werkzeugmaschinen. Carl Hanser, München/Wien 1991, S. 46, 62, 66, 91, 115 f., 146, 201, 291, 308, 427.
Günter Spur: Produktionstechnik im Wandel. Carl Hanser, München/Wien 1979, S. 39, 56, 82. - ↑ Franz Reber: Des Vitruvius Zehn Bücher über Architektur. Kraiss & Hoffmann, Stuttgart 1865, S. 347.
- ↑ Roger B. Ulrich: Roman Woodworking. Yale Univ. Press, London 2007, S. 39.
- ↑ Günter Spur: Produktionstechnik im Wandel. Carl Hanser, München/Wien 1979, S. 45.
- ↑ Bibliothèque nationale de France, Département des manuscrits, Latin 11560 online, fol. 84r, links oben.
- ↑ Günter Spur: Vom Wandel der industriellen Welt durch Werkzeugmaschinen. Carl Hanser, München/Wien 1991, S. 91–93.
- ↑ Günter Spur: Produktionstechnik im Wandel. Carl Hanser, München/Wien 1979, S. 81–83.
- ↑ Wolfgang König (Hrsg.): Propyläen Technikgeschichte. Band 3. Propyläen, Berlin 1997, S. 194.
- ↑ Günter Spur: Vom Wandel der industriellen Welt durch Werkzeugmaschinen. Carl Hanser, München/Wien 1991, S. 115 f.
- ↑ Ganzes Werk als PDF: ETH-Bibliothek Zürich abgerufen am 26. Feb. 2017.
- ↑ Charles Plumier: L’art de tourner ou de faire en perfection toutes sortes d’ouvrages au tour. Dans lequel outre les principes & les élémens du tour qu’on y enseigne méthodiquement pour tourner tant le bois, l’ivoire &c, que le fer & les autres métaux, […]. A Paris. Chez Pierre Aubouin, Pierre Ribou & Claude Jombert, 1706, Préface, S. 3.
- ↑ Günter Spur: Vom Wandel der industriellen Welt durch Werkzeugmaschinen. Carl Hanser, München/Wien 1991, S. 116.
- ↑ Günter Spur: Vom Wandel der industriellen Welt durch Werkzeugmaschinen. Carl Hanser, München/Wien 1991, S. 116 f.
- ↑ Christoph Weigel: Abbildung Der Gemein-Nützlichen Haupt-Stände […]. Regensburg 1698, S. 441–442. PDF in LSUB Dresden online, abgerufen am 28. Feb. 2017.
- ↑ Johann Heinrich Moritz von Poppe: Geschichte aller Erfindungen und Entdeckungen im Bereiche der Gewerbe, Künste und Wissenschaften. Hoffmansche Verlagsbuchhandlung, Stuttgart 1837, S. 250, § 255.
- ↑ Nasmyth: Remarks on the introduction of the slide principle in tools and machines employed in de produce. In: Appendix B von Robert Buchanan: Practical Essays on mill work and other machinery, mechanical and descriptive. J. Weale, London 1841.
- ↑ Wolfgang König (Hrsg.): Propyläen Technikgeschichte. Band 3. Propyläen, Berlin 1997, S. 145.
- ↑ Lothar Gall (Hrsg.): Enzyklopädie Deutscher Geschichte – Band 79. Christian Kleinschmidt: Technik und Wirtschaft im 19. und 20. Jahrhundert. Oldenbourg, 2007, S. 8 f.
- ↑ Günter Spur: Vom Wandel der industriellen Welt durch Werkzeugmaschinen. Carl Hanser, München/Wien 1991, S. 146.
- ↑ Günter Spur: Vom Wandel der industriellen Welt durch Werkzeugmaschinen. Carl Hanser, München/Wien 1991, S. 151 f.
- ↑ Wolfgang König (Hrsg.): Propyläen Technikgeschichte. Band 3. Propyläen, Berlin 1997, S. 196.
- ↑ Wolfgang König (Hrsg.): Propyläen Technikgeschichte. Band 3. Propyläen, Berlin 1997, S. 319.
- ↑ Günter Spur: Vom Wandel der industriellen Welt durch Werkzeugmaschinen. Carl Hanser, München/Wien 1991, S. 282, 285, 291–295.
- ↑ Kief, Roschiwal: NC/CNC Handbuch 2007/2008. Hanser, 2007, S. 156–159.
- ↑ Schönherr: Spanende Fertigung. Oldenbourg, 2002, S. 67.
- ↑ Alfred Herbert Fritz, Günter Schulze (Hrsg.): Fertigungstechnik. Springer, 9. Auflage, 2010, S. 311.
- ↑ Günter Spur: Vom Wandel der industriellen Welt durch Werkzeugmaschinen. Carl Hanser, München/Wien 1991, S. 147.
- ↑ Uwe Heisel, Fritz Klocke, Eckart Uhlmann, Günter Spur (Hrsg.): Handbuch Spanen. 2. Auflage, Hanser, München 2014, S. 277.
- ↑ Schönherr: Spanende Fertigung. Oldenbourg, 2002, S. 67, 74.
- ↑ Fritz, Schulze: Fertigungstechnik. 11. Auflage, S. 4.
- ↑ Heisel, Klocke, Uhlmann, Spur: Handbuch Spanen. Hanser, 2014, S. 13, 157, 217, 262, 267.
- ↑ Heinz Tschätsch: Praxis der Zerspantechnik. Vieweg, 7. Auflage, S. 49 f.
- ↑ Uwe Heisel, Fritz Klocke, Eckart Uhlmann, Günter Spur (Hrsg.): Handbuch Spanen. 2. Auflage, Hanser, München 2014, S. 159.
- ↑ Uwe Heisel, Fritz Klocke, Eckart Uhlmann, Günter Spur (Hrsg.): Handbuch Spanen. 2. Auflage, Hanser, München 2014, S. 151.
- ↑ Herbert Schönherr: Spanende Fertigung. Oldenbourg, 2002, S. 68.
- ↑ Heinz Tschätsch: Praxis der Zerspantechnik. Vieweg, 7. Auflage, 2005, S. 40.
- ↑ Fritz Klocke, Wilfried König: Fertigungsverfahren Band 1: Drehen, Fräsen, Bohren. Springer, 8. Auflage, 2008, S. 419 f.
- ↑ Uwe Heisel, Fritz Klocke, Eckart Uhlmann, Günter Spur: Handbuch Spanen. 2. Auflage, Hanser, München 2014. S. 150 f.
- ↑ Heinz Tschätsch: Praxis der Zerspantechnik. Vieweg, 7. Auflage, 2005, S. 42.
- ↑ Herbert Schönherr: Spanende Fertigung. Oldenbourg, 2002, S. 68 f.
- ↑ Uwe Heisel, Fritz Klocke, Eckart Uhlmann, Günter Spur (Hrsg.): Handbuch Spanen. 2. Auflage, Hanser, München 2014, S. 151.
- ↑ Fritz Klocke, Wilfried König: Fertigungsverfahren Band 1: Drehen, Fräsen, Bohren. Springer, 8. Auflage, 2008, S. 420 f.
- ↑ Herbert Schönherr: Spanende Fertigung. Oldenbourg, 2002, S. 71.
- ↑ Uwe Heisel, Fritz Klocke, Eckart Uhlmann, Günter Spur (Hrsg.): Handbuch Spanen. 2. Auflage, Hanser, München 2014, S. 151.
- ↑ Uwe Heisel, Fritz Klocke, Eckart Uhlmann, Günter Spur (Hrsg.): Handbuch Spanen. 2. Auflage, Hanser, München 2014, S. 151.
- ↑ Herbert Schönherr: Spanende Fertigung. Oldenbourg, 2002, S. 70.
- ↑ Fritz Klocke, Wilfried König: Fertigungsverfahren Band 1: Drehen, Fräsen, Bohren. Springer, 8. Auflage, 2008, S. 291.
- ↑ Fritz Klocke, Wilfried König: Fertigungsverfahren Band 1: Drehen, Fräsen, Bohren. Springer, 8. Auflage, 2008, S. 420 f.
- ↑ Uwe Heisel, Fritz Klocke, Eckart Uhlmann, Günter Spur (Hrsg.): Handbuch Spanen. 2. Auflage, Hanser, München 2014, S. 151.
- ↑ Fritz Klocke, Wilfried König: Fertigungsverfahren Band 1: Drehen, Fräsen, Bohren. Springer, 8. Auflage, 2008, S. 291.
- ↑ Herbert Schönherr: Spanende Fertigung. Oldenbourg, 2002, S. 69 f.
- ↑ Herbert Schönherr: Spanende Fertigung. Oldenbourg, 2002, S. 70.
- ↑ Alfred Herbert Fritz, Günter Schulze (Hrsg.): Fertigungstechnik. Springer, 9. Auflage, 2010, S. 291.
- ↑ Uwe Heisel, Fritz Klocke, Eckart Uhlmann, Günter Spur (Hrsg.): Handbuch Spanen. 2. Auflage, Hanser, München 2014, 151.
- ↑ Uwe Heisel, Fritz Klocke, Eckart Uhlmann, Günter Spur (Hrsg.): Handbuch Spanen. 2. Auflage, Hanser, München 2014, S. 152.
- ↑ Fritz Klocke, Wilfried König: Fertigungsverfahren Band 1: Drehen, Fräsen, Bohren. Springer, 8. Auflage, 2008, S. 291.
- ↑ Uwe Heisel, Fritz Klocke, Eckart Uhlmann, Günter Spur (Hrsg.): Handbuch Spanen. 2. Auflage, Hanser, München 2014, S. 152.
- ↑ Herbert Schönherr: Spanende Fertigung. Oldenbourg, 2002, S. 71.
- ↑ Fritz Klocke, Wilfried König: Fertigungsverfahren Band 1: Drehen, Fräsen, Bohren. Springer, 8. Auflage, 2008, S. 421 f.
- ↑ Fritz Klocke, Wilfried König: Fertigungsverfahren Band 1: Drehen, Fräsen, Bohren. Springer, 8. Auflage, 2008, S. 291 f.
- ↑ Heinz Tschätsch: Praxis der Zerspantechnik. Verfahren, Werkzeuge, Berechnung. 11. Auflage, Springer Vieweg, Wiesbaden 2014, S. 47 f.
- ↑ Uwe Heisel, Fritz Klocke, Eckart Uhlmann, Günter Spur (Hrsg.): Handbuch Spanen. 2. Auflage, Hanser, München 2014, S. 152.
- ↑ Fritz Klocke, Wilfried König: Fertigungsverfahren Band 1: Drehen, Fräsen, Bohren. Springer, 8. Auflage, 2008, S. 422.
- ↑ Fritz Klocke, Wilfried König: Fertigungsverfahren Band 1: Drehen, Fräsen, Bohren. Springer, 8. Auflage, 2008, S. 292.
- ↑ Uwe Heisel, Fritz Klocke, Eckart Uhlmann, Günter Spur (Hrsg.): Handbuch Spanen. 2. Auflage, Hanser, München 2014, S. 152.
- ↑ Herbert Schönherr: Spanende Fertigung. Oldenbourg, 2002, S. 71.
- ↑ Alfred Herbert Fritz, Günter Schulze (Hrsg.): Fertigungstechnik. Springer, 9. Auflage, 2010, S. 292.
- ↑ Fritz Klocke, Wilfried König: Fertigungsverfahren Band 1: Drehen, Fräsen, Bohren. Springer, 8. Auflage, 2008, S. 422.
- ↑ Uwe Heisel, Fritz Klocke, Eckart Uhlmann, Günter Spur (Hrsg.): Handbuch Spanen. 2. Auflage, Hanser, München 2014, S. 152.
- ↑ Uwe Heisel, Fritz Klocke, Eckart Uhlmann, Günter Spur (Hrsg.): Handbuch Spanen. 2. Auflage, Hanser, München 2014, S. 152.
- ↑ Uwe Heisel, Fritz Klocke, Eckart Uhlmann, Günter Spur (Hrsg.): Handbuch Spanen. 2. Auflage, Hanser, München 2014, S. 152.
- ↑ Herbert Schönherr: Spanende Fertigung. Oldenbourg, 2002, S. 72.
- ↑ Fritz Klocke, Wilfried König: Fertigungsverfahren Band 1: Drehen, Fräsen, Bohren. Springer, 8. Auflage, 2008, S. 423.
- ↑ Uwe Heisel, Fritz Klocke, Eckart Uhlmann, Günter Spur (Hrsg.): Handbuch Spanen. 2. Auflage, Hanser, München 2014, S. 152.
- ↑ Uwe Heisel, Fritz Klocke, Eckart Uhlmann, Günter Spur (Hrsg.): Handbuch Spanen. 2. Auflage, Hanser, München 2014, S. 152.
- ↑ Uwe Heisel, Fritz Klocke, Eckart Uhlmann, Günter Spur (Hrsg.): Handbuch Spanen. 2. Auflage, Hanser, München 2014, S. 152.
- ↑ Uwe Heisel, Fritz Klocke, Eckart Uhlmann, Günter Spur (Hrsg.): Handbuch Spanen. 2. Auflage, Hanser, München 2014, S. 152.
- ↑ Fritz Klocke, Wilfried König: Fertigungsverfahren Band 1: Drehen, Fräsen, Bohren. Springer, 8. Auflage, 2008, S. 423.
- ↑ Alfred Herbert Fritz, Günter Schulze (Hrsg.): Fertigungstechnik. Springer, 9. Auflage, 2010, S. 292.
- ↑ Uwe Heisel, Fritz Klocke, Eckart Uhlmann, Günter Spur (Hrsg.): Handbuch Spanen. 2. Auflage, Hanser, München 2014, S. 152.
- ↑ Uwe Heisel, Fritz Klocke, Eckart Uhlmann, Günter Spur (Hrsg.): Handbuch Spanen. 2. Auflage, Hanser, München 2014, S. 152.
- ↑ Fritz Klocke, Wilfried König: Fertigungsverfahren Band 1: Drehen, Fräsen, Bohren. Springer, 8. Auflage, 2008, S. 292.
- ↑ Uwe Heisel, Fritz Klocke, Eckart Uhlmann, Günter Spur (Hrsg.): Handbuch Spanen. 2. Auflage, Hanser, München 2014, S. 153.
- ↑ Alfred Herbert Fritz, Günter Schulze (Hrsg.): Fertigungstechnik. Springer, 9. Auflage, 2010, S. 292.
- ↑ Uwe Heisel, Fritz Klocke, Eckart Uhlmann, Günter Spur (Hrsg.): Handbuch Spanen. 2. Auflage, Hanser, München 2014, S. 153.
- ↑ Fritz Klocke, Wilfried König: Fertigungsverfahren Band 1: Drehen, Fräsen, Bohren. Springer, 8. Auflage, 2008, S. 424.
- ↑ Uwe Heisel, Fritz Klocke, Eckart Uhlmann, Günter Spur (Hrsg.): Handbuch Spanen. 2. Auflage, Hanser, München 2014, S. 153.
- ↑ Fritz Klocke, Wilfried König: Fertigungsverfahren Band 1: Drehen, Fräsen, Bohren. Springer, 8. Auflage, 2008, S. 424.
- ↑ Uwe Heisel, Fritz Klocke, Eckart Uhlmann, Günter Spur (Hrsg.): Handbuch Spanen. 2. Auflage, Hanser, München 2014, S. 153.
- ↑ Fritz Klocke, Wilfried König: Fertigungsverfahren Band 1: Drehen, Fräsen, Bohren. Springer, 8. Auflage, 2008, S. 424.
- ↑ Herbert Schönherr: Spanende Fertigung. Oldenbourg, 2002, S. 72.
- ↑ Fritz Klocke, Wilfried König: Fertigungsverfahren Band 1: Drehen, Fräsen, Bohren. Springer, 8. Auflage, 2008, S. 424.
- ↑ Uwe Heisel, Fritz Klocke, Eckart Uhlmann, Günter Spur (Hrsg.): Handbuch Spanen. 2. Auflage, Hanser, München 2014, S. 153.
- ↑ Unrunddrehverfahren ICTT. Abgerufen am 8. Februar 2021.
- ↑ Herbert Schönherr: Spanende Fertigung. Oldenbourg, 2002, S. 91.
- ↑ Herbert Schönherr: Spanende Fertigung. Oldenbourg, 2002, S. 116 f.
- ↑ Heinz Tschätsch: Praxis der Zerspantechnik. Verfahren, Werkzeuge, Berechnung. 11. Auflage, Springer Vieweg, Wiesbaden 2014, S. 43 f.
- ↑ Herbert Schönherr: Spanende Fertigung. Oldenbourg, 2002, S. 127 f.
- ↑ Uwe Heisel, Fritz Klocke, Eckart Uhlmann, Günter Spur (Hrsg.): Handbuch Spanen. 2. Auflage, Hanser, München 2014, S. 285–288.
- ↑ Uwe Heisel, Fritz Klocke, Eckart Uhlmann, Günter Spur (Hrsg.): Handbuch Spanen. 2. Auflage, Hanser, München 2014, S. 275–278.
- ↑ Fritz Klocke, Wilfried König: Fertigungsverfahren Band 1: Drehen, Fräsen, Bohren. Springer, 8. Auflage, 2008, S. 50 f.
- ↑ Heisel, Klocke, Uhlmann, Spur: Handbuch Spanen. Hanser, 2014, S. 164–176.
- ↑ Heisel, Klocke, Uhlmann, Spur: Handbuch Spanen. Hanser, 2014, S. 154–158.
- ↑ Herbert Schönherr: Spanende Fertigung. Oldenbourg, 2002, S. 99 f.
- ↑ Heisel, Klocke, Uhlmann, Spur: Handbuch Spanen. Hanser, 2014, S. 183–194.
- ↑ Herbert Schönherr: Spanende Fertigung. Oldenbourg, 2002, S. 102–109.
- ↑ Europa-Lehrmittel (Hrsg.): Industrielle Fertigung – Fertigungsverfahren, Mess- und Prüfmittel. 2011, S. 232–238.
- ↑ Europa-Lehrmittel (Hrsg.): Industrielle Fertigung – Fertigungsverfahren, Mess- und Prüfmittel. 2011, S. 232–238.
- ↑ Fritz Klocke, Wilfried König: Fertigungsverfahren 1 – Drehen, Fräsen, Bohren. Springer, 8. Auflage, 2008, S. 371–383.
- ↑ Herbert Schönherr: Spanende Fertigung. Oldenbourg, 2002, S. 116 f.
- ↑ Fritz Klocke, Wilfried König: Fertigungsverfahren 1 – Drehen, Fräsen, Bohren. Springer, 8. Auflage, 2008, S. 372.
- ↑ Herbert Schönherr: Spanende Fertigung. Oldenbourg, 2002, S. 116 f.
- ↑ Herbert Schönherr: Spanende Fertigung. Oldenbourg, 2002, S. 77–80.
- ↑ Schönherr: Spanende Fertigung. Oldenbourg, 2002, S. 117.
- ↑ Schönherr: Spanende Fertigung. Oldenbourg, 2002, S. 142 f.
- ↑ Schönherr: Spanende Fertigung. Oldenbourg, 2002, S. 130 f.
- ↑ Schönherr: Spanende Fertigung. Oldenbourg, 2002, S. 132 f.