„Tunnelvortriebsmaschine“ – Versionsunterschied
[ungesichtete Version] | [ungesichtete Version] |
K Ferutsch verschob die Seite Tunnelbohrmaschine nach Tunnelvortriebsmaschine und überschrieb dabei eine Weiterleitung: korrekte Bezeichnung: Verschiebung auf den Oberbegriff für diese Art Maschinen, gemäß Diskussion. Der Artikel wurde grundlegend überarbeitet, Änderungen werden im Anschluss eingebaut |
Artikel grundlegend überarbeitet gemäß Diskussion |
||
Zeile 1: | Zeile 1: | ||
[[Datei: |
[[Datei:A déli pajzs a keresztezőkamrában.jpg|mini|Tunnelvortriebsmaschine beim Bau des [[Eurotunnel|Eurotunnels]]]] |
||
'''Tunnelvortriebsmaschinen''' (kurz ''TVM'') kommen beim Bau von [[Tunnel]]n bzw. [[Stollen (Tunnelbau)|Stollen]] zum Einsatz, insbesondere dem Bau von [[Straßentunnel|Straßen-]] und [[Eisenbahntunnel|Bahntunneln]]. Der Tunnelvortieb oder kurz [[Streckenvortrieb|Vortrieb]] bezeichnet hierbei das Erweitern des Tunnels ausgehend von seinem vorderen Ende (sogenannte [[Ortsbrust|Orstbrust]]). |
|||
[[Datei:TBM City-Tunnel Leipzig - S326.jpg|mini|Tunnelbohrmaschine beim Auffahren ([[City-Tunnel Leipzig|City-Tunnels Leipzig]]; 2007)]] |
|||
[[Datei:Bohrkopf.jpg|mini|12-Meter-Bohrkopf ([[Pfändertunnel]]-Weströhre; 2008)]] |
|||
Verschiedene Arbeiten im [[Tunnelbau]] können mit einer TVM [[Automatisierung|automatisiert]] werden. Insbesondere verfügt eine derartige Maschine über Vorrichtungen zum [[Abbau (Bergbau)|Abbau]] des im Wege befindlichen Materials ([[Gestein]] oder [[Erdreich|Erdreich)]]. Eine weitere Herausforderung im Tunnelbau besteht oftmals darin, den neu geschaffenen Hohlraum unmittelbar gegen ein Eindringen des umgebenden Materials zu sichern. Als temporäre Abstützung verfügen viele TVM daher über einen Schild, auch Schildmantel genannt (siehe [[Schildvortrieb]]). Weiterhin kann auch der dauerhafte [[Grubenausbau|Ausbau]] des Tunnels mithilfe der TVM erfolgen. |
|||
[[Datei:TBM S-210 Alptransit Faido East.jpg|mini|Kopf der S-210, die die östliche Röhre des Gotthard-Basistunnels zwischen Bodio und Faido bohrte (Schneidrollen bereits entfernt; 2006)]] |
|||
[[Datei:Zürich - Oerlikon - Tunnelbohrmaschine IMG 0002.JPG|mini|Bohrmaschine für den Rettungsstollen des [[Weinbergtunnel]]s in Zürich vor dem Einsatz, August 2008]] |
|||
Die Anforderungen an eine TVM können hierbei je nach Bauprojekt sehr verschieden sein. Insbesondere bestimmt die Art des umgebenden Materials, welche Abbauwerkzeuge geeignet sind und welche Abstützungs- und Ausbaumaßnahmen erforderlich werden. Dementsprechend wird eine TVM in der Regel für einen spezifischen Tunnel individuell angefertigt und vor Ort zusammengesetzt. Ein Transport am Stück ist aufgrund der Größe häufig nicht möglich. |
|||
Für das unterirdische Verlegen von [[Leitungsnetz|Leitungen]] aller Art existieren weitere Arten von Vortriebsmaschinen und -techniken mit kleineren Querschnitten. Diese werden unter dem Begriff [[Rohrvortrieb]] zusammengefasst<ref name=":1" />, siehe dort. |
|||
== Arten von Tunnelvortriebsmaschinen == |
|||
Entsprechend der unterschiedlichen Aufgaben und Anforderungen werden verschiedene Bauformen definiert. Hierbei werden im Wesentlichen die ''Tunnelbohrmaschine'' (TBM) und die ''Schildmaschine'' (SM) unterschieden<ref name="DAUB">[https://www.daub-ita.de/fileadmin/documents/daub/withdrawn/2010-11_DAUB_Empfehlung_zur_Auswahl_von_Tunnelvortriebsmaschinen.pdf Empfehlung zur Auswahl von Tunnelvortriebsmaschinen], Deutscher Ausschuss für unterirdisches Bauen (DAUB), 2010 (Abgerufen am 23. Januar 2024)</ref>. |
|||
* '''Tunnelbohrmaschinen''' verfügen über einen Bohrkopf am vorderen Ende. Sie werden in der Regel, aber nicht ausschließlich, im [[Locker-, Halbfest- und Festgestein|Festgestein]] eingesetzt<ref name=":1">{{Literatur |Autor=Ulrich Maidl, Bernhard Maidl |Titel=Maschineller Tunnelbau mit Tunnelvortriebsmaschinen und Rohrvortrieb |Sammelwerk=Handbuch für Bauingenieure: Technik, Organisation und Wirtschaftlichkeit |Verlag=Springer Fachmedien |Ort=Wiesbaden |Datum=2020 |Reihe=Handbuch für Bauingenieure |ISBN=978-3-658-21749-5 |DOI=10.1007/978-3-658-21749-5_32-4 |Seiten=1–74 }}</ref>. Durch die hohe Standfestigkeit des Gebirges bei festem Gestein kann hierbei oftmals auf einen Schild verzichtet werden (''offene'' ''TBM''), dennoch gibt es auch TBM mit Schild. |
|||
* '''Schildmaschinen''' finden überwiegend im Lockergestein Anwendung und verfügen über einen Schild zur Stützung des umgebenden Materials. Beim Abbau unterscheidet man ''vollflächig'' (SM-V), mittels eines rotierenden Schneidrads, und ''teilflächig'' (SM-T), mittels [[Bagger]] oder [[Teilschnittmaschine|Fräse]], siehe den Unterabschnitt [[Benutzer:Ferutsch/Tunnelvortriebsmaschine#Materialabtrag|Abbau]]. |
|||
Die Schildmaschinen werden außerdem dahingehend unterschieden, ob und mit welchem Verfahren zusätzlich zur späteren Außenwand auch die Ortsbrust des Tunnels gestützt wird. Dies erfolgt beispielsweise mechanisch oder mittels Flüssigkeits- oder Druckluftstützung. |
|||
{{Stammbaum/Start |style=margin:1em;}} |
|||
{{Stammbaum|boxstyle=background:#ff6;| | | AAA | | |AAA=Tunnelvortriebsmaschinen<br />TVM}} |
|||
{{Stammbaum | |,|-|^|-|.| |}} |
|||
{{Stammbaum | |!| | | |!| | }} |
|||
{{Stammbaum | BBB | | CCC ||BBB=Tunnelbohrmaschinen<br />TBM<br />[[Datei:TBM S-210 Alptransit Gotthard Modell 1.jpg|rahmenlos|150px]] |CCC=Schildmaschinen<br />SM }}{{Stammbaum | | | | | |!| | | | | }} |
|||
{{Stammbaum | | | |,|-|^|-|.| | | | | |}} |
|||
{{Stammbaum | | | FFF | | GGG | | | | |FFF=Schildmaschinen mit Vollschnittabbau<br />SM-V<br />[[Datei:Herrenknecht Tunnelbohrmaschine Modell 4.JPG|rahmenlos|150px]] |GGG=Schildmaschinen mit teilflächigem Abbau<br />SM-T<br />[[Datei:OFS 04res.jpg|rahmenlos|150px]]}} |
|||
{{Stammbaum/Ende}} |
|||
== Aufbau und Komponenten == |
|||
Der Aufbau einer TVM basiert auf der zeitlichen und räumlichen Abfolge der einzelnen Arbeitsschritte im Tunnelbau. An der Spitze einer TVM (unmittelbar vor der [[Ortsbrust]]) befindet sich die Vorrichtung, mit welcher zunächst das im Wege befindliche Material abgebaut wird. Dahinter befindet sich, wenn vorhanden, der Schildmantel, welcher das umgebende Material temporär abstützt, sowie die Vorschubeinrichtung. Abschließend folgt der dauerhafte Ausbau mit den dafür vorgesehenen Vorrichtungen. Der Abtransport des abgebauten Materials erfolgt parallel durch den vorderen Teil hindurch. Im hinteren bereich (''Nachläufer'') der Maschine befinden sich Hilfs- und Versorgungseinrichtungen sowie Anlagen für Anlieferung und Abtransport. Im Folgenden werden die einzelnen Komponenten nach ihren Aufgaben unterteilt und erläutert. |
|||
=== Abbau === |
|||
[[Datei:ST U-Link TBM Cutterhead closeup (5501360328).jpg|mini|Schneidrad mit Rollenmeißeln und Schälmessern]] |
|||
Am vorderen Ende einer TVM, unmittelbar an der Ortsbrust, wird das im Wege befindliche Material abgetragen und den Vorrichtungen zum Abtransport zugeführt. Je nach Beschaffenheit des Gebirges bzw. Baugrunds sind unterschiedliche Abbauverfahren und Werkzeuge geeignet. Man unterscheidet zwischen vollflächigem und teilflächigem Abbau. |
|||
Beim ''vollflächigen'' ''Abbau'' kommt eine rotierende Scheibe zum Einsatz, welche die Querschnittsfläche des Tunnels voll ausfüllt. Dieser sogenannte ''Werkzeug''- oder ''Meißelträger'' ist mit den Abbauwerkzeugen bestückt, in der Regel [[Rollenmeißel]] (auch ''Schneidrollen'' oder ''Disken'' genannt) oder ''Schälmesser''. Zusätzlich kommen sogenannte ''Räumer'' in Form abgeschrägter Bleche sowie weitere Trichterförmige Vorrichtungen zum Einsatz, um das Ausbruchsmaterial abzuführen. Dieser Aufbau wird im Festgestein insgesamt als ''Bohrkopf'', im Lockergestein als ''Schneidrad'' bezeichnet<ref name="DAUB" />. Zum Tunnelvortrieb wird er mittels [[Elektromotor|Elektromotoren]] in Rotation versetzt und mit hohem Druck gegen die Ortsbrust gepresst. Bei diesem Verfahren können nur runde Tunnelquerschnitte realisiert werden. |
|||
Beim ''teilflächigen'' ''Abbau'' kommen andere im Erd-und Bergbau zu diesem Zweck verwendete Geräte zum Einsatz. Dies sind insbesondere [[Teilschnittmaschine]]n oder [[Bagger]], letztere beispielsweise mit einem [[Reißzahn (Baumaschine)|Reißzahn]] als [[Anbaugerät (Baumaschine)|Anbaugerät]]. |
|||
=== Sicherung des Hohlraums === |
|||
Eine wesentliche Aufgabe im Tunnelbau besteht darin, den Tunnelhohlraum offen zu halten und einen Einsturz oder das Eindringen von [[Grundwasser]] zu verhindern. Dies betrifft die Ortsbrust und die seitliche Außenfläche des Tunnelhohlraums, die sogenannte ''Ausbruchslaibung''. Ein wichtiger zu berücksichtigender Parameter ist hierbei die Standfestigkeit bzw. Standzeit des umgebenden Materials. Sie beschreibt dessen Fähigkeit, einen bestimmten Zeitraum um einen nicht unterstützten Hohlraum ohne Zerstörung stehen zu bleiben<ref>{{Literatur |Autor=Walter Bischoff, Heinz Bramann |Titel=Das kleine Bergbaulexikon |Verlag=Verlag Glückauf |Ort=Essen |Datum=1998 |ISBN=978-3-7739-0501-7}}</ref>. |
|||
Im fertigen Zustand des Tunnels wird die Ausbruchslaibung durch den [[Grubenausbau|Ausbau]] dauerhaft gesichert bzw. abgestützt. Während dem Bau des Tunnels ergibt sich jedoch im Bereich der Ortsbrust und unmittelbar dahinter ein Bereich ohne eine derartige Stützung. Bei Tunneln im Festgestein kann die Standfestigkeit ausreichend sein, um diesen Bereich ungestützt zu lassen. Dies ist der Einsatzbereich von Tunnelbohrmaschinen ohne Schild. Reicht die Standfestigkeit jedoch nicht aus oder tritt zu viel Grundwasser zu, so werden zusätzliche Abstützungsmaßnahmen erforderlich. |
|||
==== Schildmantel ==== |
|||
[[Datei:Yucca Mountain TBM.jpg|mini|Schildmantel]] |
|||
Zur Stützung der Ausbruchslaibung kommt ein ''Schildmantel'' oder kurz ''Schild'' zum Einsatz. Es handelt sich dabei um eine röhrenartige Stahlkonstruktion, welche die Maschine nach außen hin abschließt. Im Schutze des Schildes findet dann der Ausbau statt, sodass am hinteren Ende des Schildes kein ungestützter Bereich mehr verbleibt. Der Radius des Bohrkopfes bzw. Schneidrads kann hierbei größer sein als der des Schildes (''Überschnitt''). Dies dient einer Verbesserung der Kurvenfahrt sowie einer Entspannung des umgebenden Materials, was auch zu einer geringeren [[Reibung|Mantelreibung]] am Schild führt<ref name="DAUB" />. Als weiterentwickelte Bauform gibt es sogenannte ''Doppelschild-'' oder ''Teleskopschildmaschinen,'' bei denen zwei Schilde zum Einsatz kommen. Die Vorrichtungen für Vorschub und Ausbau liegen hierbei im inneren, hinteren Schildmantel, auf dem teleskopartig axial beweglich ein äußerer, vorderer, die Bohreinheit umschließender Schildmantel fahrbar ist. Dadurch kann eine hohe Vortriebsgeschwindigkeit erreicht werden<ref>[https://www.herrenknecht.com/de/produkte/kernprodukte/tunnelling/doppelschild-tbm.html ''Doppelschild-TBM – Kontinuierlicher Vortrieb mit Höchstgeschwindigkeit.''] Webpräsenz der Herrenknecht AG, abgerufen am 14. September 2018</ref>. |
|||
{{Siehe auch|Schildvortrieb}} |
|||
==== Ortsbruststützung ==== |
|||
Eine '''Tunnelbohrmaschine''' ('''TBM''') ist eine Maschine, die zur [[Streckenauffahrung|Auffahrung]] von [[Tunnel]]n eingesetzt wird. Sie eignet sich insbesondere für hartes [[Gestein]], aber auch für den [[Tunnelbau]] in lockerem Fels, der für den Vortrieb mittels konventionellem [[Sprengvortrieb]] ungeeignet ist. Tunnelbohrmaschinen gehören, ebenso wie auch die [[Schildvortrieb|Schildmaschinen]] (SM), zu den ''Tunnelvortriebsmaschinen'' (''TVM'')<ref>[https://www.daub-ita.de/fileadmin/documents/daub/withdrawn/2010-11_DAUB_Empfehlung_zur_Auswahl_von_Tunnelvortriebsmaschinen.pdf Empfehlung zur Auswahl von Tunnelvortriebsmaschinen], Deutscher Ausschuss für unterirdisches Bauen (DAUB), 2010, S. 11 und Anlage 1 (Abgerufen am 23. Januar 2024)</ref>. |
|||
[[Datei:Hallandsåstunneln TBM model - 02.jpg|mini|Kombinationsschildmaschine (Multi-Mode-TBM der Firma Herrenknecht<ref>{{Internetquelle |url=https://www.herrenknecht.com/de/services/vortrieb/hallandsaastunnel/ |titel=Hallandsåstunnel - Herrenknecht AG |abruf=2024-03-09}}</ref>)]] |
|||
Für eine zusätzliche Stützung der Ortsbrust gibt es verschiedene Möglichkeiten<ref name="DAUB" />: |
|||
* Flüssigkeitsstützung, beispielsweise mit [[Bentonit]]-Suspension |
|||
== Aufbau und Typen == |
|||
* Erddruckstützung, hierbei wird ein Brei aus abgebautem Boden als Stützmedium verwendet, siehe [[Flüssigboden]] |
|||
{{Überarbeiten|2=Dieser Artikel|grund=ÖVBB-Richtline führt andere Einteilung auf. Näheres ist auf der [[Diskussion:Tunnelbohrmaschine#TBM vs. TVM & weitere Einteilung von Tunnelvortriebsmachinen|Diskussionsseite]] angegeben.}} |
|||
* [[Druckluft]]<nowiki/>stützung |
|||
* Mechanische Stützung mittels Brustplatten (insbesondere beim teilflächigen Abbau) |
|||
Bei sogenannten ''Kombinationsschildmaschinen'' (KSM) kann das Verfahren der Ortsbruststützung gewechselt werden, um sich an unterschiedliche Baugrundverhältnisse entlang der [[Trasse (Verkehrsweg)|Trasse]] anszupassen. |
|||
==== Verfestigung ==== |
|||
Wichtigster Teil einer TBM ist der [[Bohrmeißel|Bohrkopf]]; er hat einen Durchmesser von bis zu 17,60 Metern<ref name=":0" /> und besteht aus einem Meißelträger mit rotierenden [[Rollenmeißel]]n, der ausgebrochenes Gestein nach hinten befördert<ref>[https://www.tunneltalk.com/Discussion-Forum-Mega-TBMs.php Tracking the world's mega-TBMs], TunnelTalk</ref>. Die Einrichtung im hinteren Teil des Bohrkopfes hat bei großen Durchmessern eine Länge von bis zu 200 Metern mit Hilfseinrichtungen. |
|||
In manchen Fällen werden bereits vor dem Abbau am Gestein oder Erdreich Maßnahmen durchgeführt, welche der [[Bodenverfestigung|Verfestigung]] dienen. Dadurch kann der notwendige Aufwand zur Abstützung während des Abuaus verringert werden. Mit Hilfe einer Schaumanlage, die mit Tensiden und Wasser unter Druck Schaum erzeugt, kann im weichen Untergrund die Ortsbrust derart verfestigt werden, dass Sandböden wie tonige Böden abgebohrt werden können. In schlammigem Boden kann die Umgebung mit [[Flüssigstickstoff]] vereist werden ([[Bodenvereisung]]). Im Festgestein wird bei sogenannten ''Erweiterungstunnelbohrmaschinen'' im Vorfeld zunächst ein Pilotstollen erstellt. Von diesem aus können [[Störzone|Störzonen]] im Gestein ertüchtigt und so die Risiken bei der anschließenden Bohung des Haupttunnels minimiert werden<ref name="DAUB" />. |
|||
=== Tunnelausbau === |
|||
Tunnelbohrmaschinen sind [[Vollschnittmaschine]]n, das heißt, sie bauen, anders als [[Teilschnittmaschine]]n, den gesamten Tunnelquerschnitt in einem Arbeitsschritt ab. |
|||
[[Datei:Positionieren-der-Tübbinge.jpg|mini|Tübbingeinbau]] |
|||
Der Ausbau des Tunnels erfolgt meist in Form einer Tunnelauskleidung mit vorgefertigten Segmenten, den [[Tübbing|Tübbings]]. Der Einbau der Tübbings kann mit einem ''Erektor'' genannten roboterähnlichen Gerät automatisch erfolgen. Dies geschieht im Schutze des hinteren Schildmantels, dem sogenannten Schildschwanz<ref>{{Webarchiv |url=http://www.wirth-erkelenz.de/index.php?id=49&L=1 |archive-is=20130212154831 |text=''Tunnelbohrmaschinen für Hartgestein.''}} In: ''[[Aker Solutions#Beteiligung in Deutschland|Aker Wirth GmbH]]'', aufgerufen am 5. Mai 2015.</ref>. Die Maschine verfügt dann außerdem über weitere Transportvorrichtungen zur Zulieferung der Tübbings zum Erektor. |
|||
Bei Tunnelbohrmaschinen ohne Schild werden auch andere Verfahren des Tunnelausbaus eingesetzt, insbesondere die [[Neue Österreichische Tunnelbaumethode|Spritzbetonbauweise]]<ref name="DAUB" />. |
|||
Derartige Maschinen werden üblicherweise von [[Förderband|Förderbändern]] unterstützt, um den bei der Arbeit entstehenden Abraum schnell fortzuschaffen, oder führen einen [[Bauzug]] mit sich, um beispielsweise [[Betonfertigteil]]e für den im Anschluss zu errichtenden Tunnel an die ähnlich nachgeführte Tunnelauskleide-Maschine heranzuführen – möglich ist zudem auch [[Spritzbeton]], welcher über Förderbänder oder [[Fahrmischer]] herangeführt und vor Ort an die Tunnelwände gebracht werden kann. |
|||
=== Vorschub === |
|||
=== Bauteile einer Tunnelbohrmaschine === |
|||
[[Datei:Distelrasen Rückseite Vortriebsschild und Stempel.jpg|mini|Hydraulikzylinder für den Vorschub]] |
|||
* Abbauschild mit Rollenmeißeln, Vorschub- und Verspanneinrichtungen |
|||
Beim Vorschub wird die TVM in Richtung der Ortsbrust verschoben, sodass sie sich im Rahmen des Tunnelvortriebs immer unmittelbar vor dieser befindet. Die Vorschubeinrichtung drückt den Bohrkopf oder das Schneidrad gegen die Ortsbrust und bewegt die Maschine nach vorne. Dies geschieht mit [[Hydraulikzylinder]]<nowiki/>n. Als [[Widerlager (Bautechnik)|Widerlager]] für diese dient meist die Vorderkante des zuletzt eingebauten Tübbing-Rings. Alternativ können Maschinen ohne Schild auch direkt am Fels der seitlichen Tunnelwand abgestützt werden''.'' Mittels sogenannter ''Gripper'' wird hierbei die Vorschubeinrichtung im Fels verankert, die entsprechende Bauform wird auch als ''Gripper-TBM'' bezeichnet. |
|||
* Einrichtungen für den Einbau von Stütz- und Ausbaumaßnahmen |
|||
* Einrichtungen zum Materialabtransport (Schutteranlagen) |
|||
* Versorgungseinheit für Strom und Druckluft zum Betrieb der Rollenmeißel, sowie Bewetterung, und Wasser zum Kühlen der Meißel |
|||
* Transporteinrichtungen für Ausbruchsmaterial, Stützmittel und Ausbaumaterialien |
|||
Beim Auffahren des Tunnels ergeben sich also üblicherweise die die folgenden beiden Arbeitsschritte: |
|||
=== Einteilung von Tunnelbohrmaschinen === |
|||
Man unterteilt in ''Offene Tunnelbohrmaschinen'' (offene Grippermaschinen und offene Doppelgrippermaschinen) und ''Schildmaschinen'' (Einfachschildmaschinen und Doppelschildmaschinen, auch Teleskopschildmaschinen). |
|||
* Der Vortrieb, bei dem die Maschine nach vorne fährt und die Ortsbrust mit Druck abbaut. |
|||
* ''Offene Tunnelbohrmaschinen'' sind für den Vortrieb in standfestem<ref group="ANM" name="Anm. KlBBL." /> Fels geeignet und kommen vielfältig für die [[Streckenauffahrung|Auffahrung]] von Verkehrswegetunneln (Bahnen und Straßen), Leitungsstollen (Elektrizität, Wasser, Gas), Druckwasserstollen (Wasserkraftwerke), sowie für Tunneln für geologische Untersuchungen oder Standseilbahnen im Hochgebirge zum Einsatz. Die Hauptbauelemente der offenen Tunnelbohrmaschine sind der Bohrkopf mit dem zugehörigen Antrieb, Verspanneinrichtung (Verspannung) und die Vorschubeinrichtung (''Kelly''). |
|||
* Der Ringbau, bei dem ein neuer Ring aus [[Tübbing]]s eingebaut wird. Hierfür werden die jeweilgen Hydraulikzylinder eingefahren. Anschließend presst die Maschine den neuen Ring gegen den vorherigen fest und beginnt erneut mit dem Vortrieb. |
|||
* ''Schildmaschinen'' werden für Vortriebe in standfesten bis nicht standfesten Felsformationen eingesetzt und werden regelmäßig für die Auffahrung von Verkehrswegetunneln (Bahnen und Straßen) und Leitungsstollen (Elektrizität, Wasser, Gas) verwendet. Namensgebendes Bauelement dieser Tunnelbohrmaschinen ist der ''Schild'' oder ''Schildmantel''. Es handelt sich dabei um röhrenartige Stahlkonstruktionen, in die alle weiteren Bauteile der Maschine sowie Bewegungsräume für Material und Personal eingebettet sind. Bei diesen Teilen handelt es sich um den Bohrkopf mit Antrieb, die Vortriebsmechanik und das roboterähnliche Gerät zum Einbau der Tunnelauskleidung, der sogenannte Erektor. Die Tunnelauskleidung – zumeist bestehend aus Betonfertigteilen – wird mit dem Erektor im Schutze des hinteren Schildmantels, dem sogenannten Schildschwanz, eingebaut.<ref>{{Webarchiv |url=http://www.wirth-erkelenz.de/index.php?id=49&L=1 |archive-is=20130212154831 |text=''Tunnelbohrmaschinen für Hartgestein.''}} In: ''[[Aker Solutions#Beteiligung in Deutschland|Aker Wirth GmbH]]'', aufgerufen am 5. Mai 2015.</ref> |
|||
** ''Einfachschild-TBM'' besitzen nur einen einzelnen Schildmantel.<ref>[https://www.herrenknecht.com/de/produkte/kernprodukte/tunnelling/einfachschild-tbm.html ''Einfachschild-TBM – Zügiger Vortrieb in wechselnden Gebirgsverhältnissen.''] Webpräsenz der Herrenknecht AG, abgerufen am 14. September 2018</ref> |
|||
** ''Doppelschild-'' oder ''Teleskopschild-TBM'' sind faktisch eine Kombination aus einer offenen und einer Einfachschild-TBM, wobei Vorschub und Erektor im inneren, hinteren Schildmantel liegen, auf dem teleskopartig axial beweglich ein äußerer, vorderer, die Bohreinheit umschließender Schildmantel fahrbar ist. Dadurch kann eine hohe Vortriebsgeschwindigkeit erreicht werden.<ref>[https://www.herrenknecht.com/de/produkte/kernprodukte/tunnelling/doppelschild-tbm.html ''Doppelschild-TBM – Kontinuierlicher Vortrieb mit Höchstgeschwindigkeit.''] Webpräsenz der Herrenknecht AG, abgerufen am 14. September 2018</ref> |
|||
=== Abtransport === |
|||
== Arbeitsschritte beim Tunnelvortrieb == |
|||
Der Abtransport des abgebauten Materials wird auch als ''Schutterung'' bezeichnet<ref>{{Literatur |Autor=Walter Zanoskar |Titel=Abförderung der Felsmassen. Schutterarbeit, Schutterung |Sammelwerk=Stollen- und Tunnelbau |Verlag=Springer Vienna |Ort=Vienna |Datum=1964 |ISBN=978-3-7091-8117-1 |DOI=10.1007/978-3-7091-8116-4_3 |Seiten=80–92}}</ref>. Die hierfür geeigneten Vorrichtungen hängen ganz von der Art und [[Konsistenz (Boden)|Konsistenz]] des abgebauten Materials ab. Grundsätzlich werden die Förderarten Trockenförderung und Pump- oder Flüssigförderung unterschieden. Letztere erfolgt über Förderleitungen und kommt insbesondere bei Flüssigkeits- oder Erddruckgestützer Ortsbrust zum Einsatz. Bei der Trockenförderung werden [[Förderband|Förderbänder,]] Erdtransporter oder gleisgebundene Systeme (''Schutterzüge'') eingesetzt<ref name=":1" />. Weiterhin kann innerhalb der TVM ein [[Brecher (Zerkleinerungsmaschine)|Brecher]] eingesetzt werden, um zu große Gesteinsbrocken, beispielsweise [[Findling|Findlinge]] im Lockergestein, auf ein transportierbares Maß zu zerkleinern<ref>{{Internetquelle |url=https://www.herrenknecht.com/de/produkte/productdetail/mixschild/ |titel=Mixschild - Herrenknecht AG |abruf=2024-02-25}}</ref>. |
|||
Das Bohren erfolgt in mehreren Schritten: |
|||
* dem eigentlichen Vortrieb, bei dem ein rotierendes Schneidrad die [[Ortsbrust]] mit Druck abbaut, |
|||
* dem Ringbau, bei dem nach erfolgtem Vortrieb die [[Tübbing]]s mit einem [[Erektor]] die Ausbruchslaibung auskleiden und abdichten. Danach presst sich die Bohrmaschine zwischen den Ringen zur Verankerung fest und drückt sich wieder weiter vor. |
|||
=== Hilfs- und Versorgungseinrichtungen === |
|||
Mit Hilfe einer Schaumanlage, die mit Tensiden und Wasser unter Druck Schaum erzeugt, kann im weichen Untergrund die Ortsbrust derart verfestigt werden, dass Sandböden wie tonige Böden abgebohrt werden können. In schlammigem Boden wird die Umgebung mit [[Flüssigstickstoff]] vereist ([[Bodenvereisung]]). |
|||
Zusätzlich zu den genannten Hauptkomponenten verfügt eine TVM über weitere unterstützende Anlagen. Dies sind beispielsweise: |
|||
*Versorgungseinheiten für Strom und Druckluft für den laufenden Betrieb, Wasser zum Kühlen der Meißel und zur Bindung von Staub, sowie [[Bewetterung]] |
|||
*Kräne und Transporteinrichtungen für die Anlieferung, insbesondere betreffend die Tübbings oder andere zum Ausbau verwendete Materialien |
|||
*Bewegungsräume und Wartungswege für Material und Personal, beispielsweise zum Austausch der Werkzeuge am Bohrkopf oder Schneidrad |
|||
== Einmalverwendung oder Wiederverwendung == |
== Einmalverwendung oder Wiederverwendung == |
||
TVM hinterlassen in der Regel einen teilausgebauten Tunnel mit einem kleineren Querschnitt als der Ausbruchdurchmesser und der Schilddurchmesser der Maschine. Das liegt an Tübbings, vorstehenden Felsbohrankern, Tunnelauskleidung und Einbauten wie Fahrbahn, Entwässerungs- und Entlüftungsrohren. Das bedingt, dass eine TVM nur in einer Richtung fortschreiten und nicht zurückgefahren werden kann. Einen gewissen Spielraum zum Zurückziehen des Schilds muss sich der Betreiber deshalb für das allfällige Versagen einzelner Teile oder das Verstopfen mit Gesteinsbrocken bewahren, um bestimmte Teile austauschen oder Brocken zerlegen zu können. Der materielle und zeitliche Aufwand für Reparaturen ist wegen der räumlich beengten Zugänglichkeit und der Beschaffung von Ersatz hoch. |
|||
Werden Tunnel nur von einer Seite |
Werden Tunnel nur von einer Seite aufgefahren, liegt die Maschine bei Tunneldurchbruch wieder an oder nahe der Oberfläche und könnte, sofern die Größe Transporte zulässt, zum nächsten Einsatzort verbracht werden. Wird die Maschine – mehr oder weniger in Teile zerlegt – umgedreht und ein Stück versetzt, kann sie zum Bau einer zweiten, parallelen Röhre dienen. |
||
Auf dem Landweg – Straße oder Schiene – können große |
Auf dem Landweg – Straße oder Schiene – können große TVM nur zerlegt transportiert werden. Auch der Schild muss dafür zerlegbar ausgeführt sein. Zwar existieren Schiffe mit ausreichend großvolumigem Laderaum, doch nur in seltenen Fällen ist es möglich, eine TVM auf dem Wasserweg direkt zum Einsatzort zu bringen. |
||
Wenn, was typisch für lange Tunnel ist, von zwei Seiten oder sogar noch mehr Stellen angefahren wird, kommt es zwangsläufig dazu, dass eine |
Wenn, was typisch für lange Tunnel ist, von zwei Seiten oder sogar noch mehr Stellen angefahren wird, kommt es zwangsläufig dazu, dass eine TVM im Berg zerlegt werden muss. Das kann mit der Absicht geschehen, mit diesen und eventuell neuen Teilen rasch wieder eine funktionierende Maschine zusammenzubauen. Besteht kein absehbarer Bedarf für eine Maschine dieses Typs, werden wenige Teile erhaltend zur Wiederverwendung abgebaut und der Maschinenrahmen zerlegt und verschrottet. |
||
In der Liste der größten |
In der Liste der größten Tunnelvortriebsmaschinen (unten) finden sich Beispiele für den Wiedereinsatz von TVM über große geografische Distanz hinweg: Niederlande–China, Deutschland–Russland. |
||
== Herstellerfirmen und Geschichte == |
== Herstellerfirmen und Geschichte == |
||
1844 trug sich der schottische Bauingenieur und Erfinder |
1844 trug sich der schottische Bauingenieur und Erfinder William Brunton (* [[26. Mai]] [[1777]] in [[Dalkeith]]; † [[5. Oktober]] [[1851]] in [[Neath (Wales)]]) mit der Idee, zum Bau eines Tunnels zwischen England und Frankreich einen [[Hammer]] durch [[Druckluft]] zum Stoßen und Bohren anzutreiben. Die erforderlichen [[Kompressor|Kompressoren]] waren zu diesem Zeitpunkt allerdings nicht entwickelt. Seine Maschine glich einem riesigen Bohrer mit dem Durchmesser des Tunnels, der das Gestein zermalmen und die Bruchstücke in den entstandenen Bohrschacht zum Abtransport abwerfen sollte.<ref>Journal ''Über Land und Meer'', Tunnel zwischen England und Frankreich, [[Deutsche Verlags-Anstalt]], Berlin, 1881.</ref> |
||
Mit dem ''stoßenden Bohren'' nach dem Patent von [[John Fowler (Erfinder)|Fowler]] aus dem Jahre 1849 fing das maschinelle Bohren 1857 an, die Einführung der mit Druckluft betriebenen |
Mit dem ''stoßenden Bohren'' nach dem Patent von [[John Fowler (Erfinder)|Fowler]] aus dem Jahre 1849 fing das maschinelle Bohren 1857 an, die Einführung der mit Druckluft betriebenen Stoßbohrmaschinen verkürzte die Bauzeit für den [[Mont-Cenis-Eisenbahntunnel]] von geschätzten 40 bis 50 Jahren auf 14 Jahre.<ref>{{Literatur |Autor=Larry C. Hoffman |Titel=The ROCK DRILL and CIVILIZATION {{!}} Rock drilling is one of the world’s most ancient technologies—and a pre requisite for nearly all the others |Sammelwerk=Invention & Technology Magazine |Band=15 |Nummer=1 |Datum=1999 |Sprache=en-US |Online=https://web.archive.org/web/20070929110558/http://www.americanheritage.com/articles/magazine/it/1999/1/1999_1_56.shtml}}</ref> |
||
Bei ''Stoßbohrmaschinen'' sind Kolben und Bohrstange durch ein Keilschloss verbunden. Bei einer Schlagzahl von 250 bis 300 Stößen pro Minute arbeiten sie mit Hüben von 50 bis 250 mm und können bei Gesamtgewichten bis 280 kg nur auf Spannschlitten mit Handkurbel-Schraubenspindelvorschub an einer Spannsäule oder auf dem Dreibock arbeiten. |
Bei ''Stoßbohrmaschinen'' sind Kolben und Bohrstange durch ein Keilschloss verbunden. Bei einer Schlagzahl von 250 bis 300 Stößen pro Minute arbeiten sie mit Hüben von 50 bis 250 mm und können bei Gesamtgewichten bis 280 kg nur auf Spannschlitten mit [[Handkurbel]]-Schraubenspindelvorschub an einer Spannsäule oder auf dem Dreibock arbeiten. |
||
Um 1870 gab es erste Versuche, eine |
Um 1870 gab es erste Versuche, eine Tunnelvortriebsmaschine zum schnelleren Vortrieb beim Bau des [[Hoosac-Tunnel]]s an der Ostküste ([[Boston]]) der USA einzusetzen und gleichzeitig das Verletzungsrisiko der Arbeiter – durch Arbeit mit Hammer und [[Meißel]] sowie Sprengungen mit [[Schwarzpulver]] (erst später kamen Vorläufer des [[Presslufthammer]]s und [[Nitroglycerin]] erstmals hier zum Einsatz) – zu verringern. Bei der Pressevorführung vor Ort war nach rund 15 Zentimetern Schluss: Sie blieb stecken. Die Schneidmeißel aus [[Gusseisen]] erwiesen sich als zu weich und die [[Dampfmaschine]] zum Antrieb als zu schwach. |
||
1897 entwickelte J. G. Leyner aus Denver die ''Hammerbohrmaschine''. Sie arbeitete nach dem schlagenden Prinzip mit Luftspülung, wobei der Kolben mit nur 1/10 des Gewichtes mit 1500 Schlägen pro Minute auf das Bohrereinsteckende schlägt und eine Drallspindel mit Sperrklinken beim Rückgang des Kolbens über die Bohrerhülse den Bohrer um 12 bis 45 Grad je Schlag umsetzt. Auch diese Geräte wurden zunächst wie die Stoßbohrmaschinen an Spannsäulen oder Dreiböcken mit Spannschlitten und Handvorschub eingesetzt. Sie erreichten nach 1918 bei allerdings höherem Luftverbrauch bereits die 10- bis 13‑fache Leistung der Stoßbohrmaschinen. |
1897 entwickelte J. G. Leyner aus Denver die ''Hammerbohrmaschine''. Sie arbeitete nach dem schlagenden Prinzip mit Luftspülung, wobei der Kolben mit nur 1/10 des Gewichtes mit 1500 Schlägen pro Minute auf das Bohrereinsteckende schlägt und eine Drallspindel mit Sperrklinken beim Rückgang des Kolbens über die Bohrerhülse den Bohrer um 12 bis 45 Grad je Schlag umsetzt. Auch diese Geräte wurden zunächst wie die Stoßbohrmaschinen an Spannsäulen oder Dreiböcken mit Spannschlitten und Handvorschub eingesetzt. Sie erreichten nach 1918 bei allerdings höherem Luftverbrauch bereits die 10- bis 13‑fache Leistung der Stoßbohrmaschinen. |
||
Zeile 62: | Zeile 107: | ||
Die Weiterentwicklung dieser Hammerbohrmaschinen führte mit dem Ersatz des Drallgetriebeumsetzens 1955 zum Druck- und schließlich zum Hydraulikmotorantrieb mit einem konstanten hohen Drehmoment. |
Die Weiterentwicklung dieser Hammerbohrmaschinen führte mit dem Ersatz des Drallgetriebeumsetzens 1955 zum Druck- und schließlich zum Hydraulikmotorantrieb mit einem konstanten hohen Drehmoment. |
||
Die weitere Entwicklung nach den Ideen von Brunton im Tunnel- und Stollenbau, die vor allem im U‑Bahn‑Bau bei geeigneten Bodenverhältnissen eine zunehmende Anwendung findet, ist durch den Einsatz von Tunnel- oder Stollenvortriebsmaschinen für Durchmesser bis zu 10,5 Metern gekennzeichnet. Der Gedanke wurde in den 1960er Jahren wieder aufgegriffen und zunächst nur im Bergbau und dann bei unterirdischen Verlagerungen eingesetzt. Stollen- und Tunnel-Vortriebsmaschinen stellen den unterirdischen Hohlraum ohne den absatzweisen Arbeitszyklus Bohren, Sprengen, Laden und Fördern kontinuierlich her, indem sie durch Werkzeuge, die für das anstehende Gebirge geeignet sind, zerspanend bis 11,7 kN/cm² mit |
Die weitere Entwicklung nach den Ideen von Brunton im Tunnel- und Stollenbau, die vor allem im U‑Bahn‑Bau bei geeigneten Bodenverhältnissen eine zunehmende Anwendung findet, ist durch den Einsatz von Tunnel- oder Stollenvortriebsmaschinen für Durchmesser bis zu 10,5 Metern gekennzeichnet. Der Gedanke wurde in den 1960er Jahren wieder aufgegriffen und zunächst nur im Bergbau und dann bei unterirdischen Verlagerungen eingesetzt. Stollen- und Tunnel-Vortriebsmaschinen stellen den unterirdischen Hohlraum ohne den absatzweisen Arbeitszyklus Bohren, Sprengen, Laden und Fördern kontinuierlich her, indem sie durch Werkzeuge, die für das anstehende Gebirge geeignet sind, zerspanend bis 11,7 kN/cm² mit Warzenmeißeln oder Schneidrollen bis 21,6 kN/cm² die Brust angreifen und das abgebaute Material hinter sich kontinuierlich abgeben. Sie werden in den USA seit 1950 in den verschiedensten Formen gebaut. Die Vorteile liegen in einer Vermeidung der Auflockerung durch den Wegfall der Sprengung, einer Verringerung des Überprofils und einem geringeren Personalbedarf. Nachteile sind die hohen Investitionskosten und die laufenden Kosten des Werkzeugverschleißes. Bekannt geworden sind die ''Alkirk-Lawrence-Pilotankermaschinen'' und die ''Oil-Shaleminer'', die einen Pilotanker vorweg treiben, an dem sich der Bohrkopf gegen die Brust zieht. Seit Anfang der 1960er Jahre werden Maschinen von ''[[Robbins Company]]'' eingesetzt, bei denen das durch die Schneiden des Fräskopfes abgesplitterte Bohrklein von Bechern oder Baggereimern hochgenommen und am Scheitel auf das Austragsband geschüttet wird. Englische und japanische Entwicklungen von Schildvortriebsmaschinen arbeiten innerhalb eines sich auf den Ausbau abstützenden Vortriebsschildes, mit einem großen, die ganze Brust erfassenden Fräskopf bzw. bei [[Mitsubishi Heavy Industries]] mit vier gegenläufigen Fräsköpfen. In Deutschland waren es die Maschinen von den Firmen [[Demag]], [[Wirth]] und [[Atlas Copco]] und die Schildvortriebsmaschinen von Bade-Holzmann, die in den 1960er Jahren die neuen Wege im Tunnel- und Stollenbau gebahnt haben. Es sind inzwischen in der Bundesrepublik Deutschland auch für den Bau von Schrägstollen, zum Bau von senkrechten Schächten und zur stufenweisen Erweiterung der Querschnitte bis auf 11 m geeignete vollmechanische Vortriebsmaschinen entwickelt worden. Bei Gesteinsfestigkeiten von 20 kN/cm² werden Warzen-, Zahn- und Disken-Cuttern eingesetzt. |
||
Seit 1966 werden ''Vollschnittmaschinen'' mit Gewichten von 48 bis 90 t und Längen von 11,5 bis 21 Metern für Profile von 2 bis 6,4 m Durchmesser eingesetzt. Ihre Antriebsleistungen betragen – abhängig von Material und Durchmesser – 240 bis 950 kW, ihre Bohrkopf-Drehzahlen 5 bis 12,7 Umdrehungen pro Minute und der Anpressdruck bis zu 8000 kN. |
Seit 1966 werden ''Vollschnittmaschinen'' mit Gewichten von 48 bis 90 t und Längen von 11,5 bis 21 Metern für Profile von 2 bis 6,4 m Durchmesser eingesetzt. Ihre Antriebsleistungen betragen – abhängig von Material und Durchmesser – 240 bis 950 kW, ihre Bohrkopf-Drehzahlen 5 bis 12,7 Umdrehungen pro Minute und der Anpressdruck bis zu 8000 kN. |
||
Zeile 76: | Zeile 121: | ||
Die Maschine wird in der Tunnelröhre mittels Pratzen durch eine vordere und hintere Verspannung mit mindestens 130 N/cm² gehalten. Der Anpressdruck des Bohrkopfes beträgt 1600 kN bei 2 m bis 6400 kN bei 6 m Durchmesser. Die Tunnelvortriebsmaschinen werden von einem Steuerstand im Schlepptender gesteuert; sie sind kurvenfahrbar mit 80 m Radius bei 2,4 m und 150 m Radius bei 6 m Durchmesser; ein Laser dient der Steuerkontrolle. Das erste Gerät wurde 1966 zum Auffahren eines 2800 m langen Abwasserstollens in Grünsandstein von 2,1 m Durchmesser in Dortmund eingesetzt; das 6‑Meter‑Gerät kam 1973 am Niederrhein zum Einsatz.<ref>[[Georg Garbotz]], ''Baumaschinen einst und jetzt'', in: ''Baumaschine und Bautechnik'', Frankfurt am Main, {{ISSN|0005-6693}}, 22. Jahrgang, Heft 5, 1975, S. 153 ff.</ref> |
Die Maschine wird in der Tunnelröhre mittels Pratzen durch eine vordere und hintere Verspannung mit mindestens 130 N/cm² gehalten. Der Anpressdruck des Bohrkopfes beträgt 1600 kN bei 2 m bis 6400 kN bei 6 m Durchmesser. Die Tunnelvortriebsmaschinen werden von einem Steuerstand im Schlepptender gesteuert; sie sind kurvenfahrbar mit 80 m Radius bei 2,4 m und 150 m Radius bei 6 m Durchmesser; ein Laser dient der Steuerkontrolle. Das erste Gerät wurde 1966 zum Auffahren eines 2800 m langen Abwasserstollens in Grünsandstein von 2,1 m Durchmesser in Dortmund eingesetzt; das 6‑Meter‑Gerät kam 1973 am Niederrhein zum Einsatz.<ref>[[Georg Garbotz]], ''Baumaschinen einst und jetzt'', in: ''Baumaschine und Bautechnik'', Frankfurt am Main, {{ISSN|0005-6693}}, 22. Jahrgang, Heft 5, 1975, S. 153 ff.</ref> |
||
Die vierte Röhre des [[Neuer Elbtunnel|Hamburger Elbtunnels]] wurde in den Jahren von 1997 bis 2000 mit der 2000 Tonnen schweren Schildvortriebsmaschine [[TRUDE]] mit einem Außendurchmesser von 14,20 m gebaut. Die zu diesem Zeitpunkt größte |
Die vierte Röhre des [[Neuer Elbtunnel|Hamburger Elbtunnels]] wurde in den Jahren von 1997 bis 2000 mit der 2000 Tonnen schweren Schildvortriebsmaschine [[TRUDE]] mit einem Außendurchmesser von 14,20 m gebaut. Die zu diesem Zeitpunkt größte Tunnelvortriebsmaschine der Welt erweiterte mit 111 Schälmessern für weiches Gestein und 31 Rollenmeißeln für Hartgestein den Tunnel durchschnittlich um 6 m/Tag. Das Schneidrad mit der „Mixschildtechnik“ war von der Firma [[Herrenknecht]] aus [[Schwanau]] entwickelt worden. Kennzeichnend waren die fünf erstmals von innen begehbaren Speichen zum Auswechseln der Schneidwerkzeuge und einen unabhängig steuerbaren Zentrumsschneider.<ref>''[http://www.museum-der-arbeit.de/de/staendige-ausstellungen/trude-die-groesste-schildvortriebsmaschine-der-welt.htm TRUDE - Die größte Schildvortriebsmaschine der Welt.]'' In: ''[[Museum der Arbeit]]'', Hamburg, aufgerufen am 5. Mai 2015.</ref> |
||
In der Schweiz wurden in den 1960er Jahren zunächst kleinere Profile mit Vortriebsmaschinen hergestellt. Ab 1970 wurden auch Großtunnel des Straßen- und Schienenverkehrs mit |
In der Schweiz wurden in den 1960er Jahren zunächst kleinere Profile mit Vortriebsmaschinen hergestellt. Ab 1970 wurden auch Großtunnel des Straßen- und Schienenverkehrs mit Tunnelvortriebsmaschinen aufgefahren. Bis Ende der 1990er Jahre wurden 19 große Straßen- oder doppelspurige Eisenbahntunnel mit einer Gesamtlänge von 83 km mit TVM aufgefahren.<ref name="schmid-1999">Leonhard Schmid, Josef Elmiger: ''Wie begründet sich der hohe Anteil von Maschinenvortrieben in der Schweiz''. In: ''Tunneltechnologie für die Zukunftsaufgaben in Europa''. Balekma-Verlag, Rotterdam 1999, ISBN 90-5809-051-5, S. 59–71.</ref> Der [[Gotthard-Basistunnel]] wurde in den Jahren von 2002 bis 2010 mit den 400 m langen und 2700 t schweren Gripper-Tunnelbohrmaschinen Heidi (S‑211) und Sissi (S‑210) der Firma [[Herrenknecht|Herrenknecht AG]] geschaffen.<ref>''{{Webarchiv|url=https://www.herrenknecht.com/de/referenzen/case-studies/gotthard-basistunnel.html |wayback=20160223141600 |text=Gotthard-Basistunnel.}}'' In: ''[[Herrenknecht]]'', März 2011, aufgerufen am 5. Mai 2015.</ref> Die Bohrköpfe der Maschinen hatten einen Durchmesser von rund 9,5 m und waren mit mehr als 60 Rollenmeißeln versehen. Sie wurden von zehn Motoren mit jeweils 350 kW angetrieben. |
||
Der Bohrkopf ist mit dem Antrieb am vorderen Ende der Vorschubeinrichtung, wie im Fachjargon ''Kelly'' genannt wird, angeschlagen (die ''kelly'' war beim [[Bohrturm|Erdölbohren]] ein an der abgesenkten Bohrwelle oben befestigtes Rohrstück mit polygonalem Querschnitt (wie etwa ein überdimensionierter [[Innensechskant]]schlüssel) dessen Führung und Drehbewegung ein Drehtisch mit ebendieser polygonalen Öffnung übernahm, das Rohr konnte mit steigender Bohrtiefe in der Führung des Bohrtisches abgesenkt werden). Die Vorschubeinrichtung besteht aus einem inneren Teil, an dem der Bohrkopf befestigt ist, der Innenkelly, und einem äußeren Teil, der sogenannten Außenkelly. Die Außenkelly der Maschine wird mittels der Verspannung in der gebohrten Tunnelröhre fixiert. Die Innenkelly mit dem am vorderen Ende angeschlagenen Bohrkopf gleitet während des Bohrvorganges parallel zur Bohrrichtung in der Außenkelly in Bohrrichtung nach vorne. Innenkelly und Außenkelly sind über die Vorschubzylinder miteinander verbunden. Die Vorschubzylinder schieben die Innenkelly mitsamt dem Bohrkopf nach vorne. Der Bohrkopf der Maschine ist mit Schneidrollen versehen, die mit Hartmetallringen bestückt sind und Diskenschneidrollen genannt werden. Der Drehantrieb des Bohrkopfes wird entweder mit Hydraulikmotoren oder Elektromotoren ausgestattet, wobei die elektrische Antriebsvariante heutzutage die gebräuchlichere geworden ist. Stufenlose Regelung der Drehzahl des Bohrkopfes ist bei modernen Tunnelbohrmaschinen mittlerweile ein Standard geworden. Um den Bohrkopf der Maschine herum ist ein Stahlschild angeordnet, der Bohrkopfmantel, der einerseits eine Stützfunktion für die gebohrte Tunnelröhre übernimmt und andererseits als Kopfschutz gegenüber eventuell herabfallenden Gesteins dient. Das abgebohrte Gestein wird über Förderbänder abtransportiert und für den Transport aus dem Tunnel entweder in Waggons geladen oder per Förderband aus dem Tunnel transportiert. Die gebohrte Tunnelröhre wird unmittelbar nach dem Bohrvorgang bei Bedarf mit der sogenannten Erstsicherung abgestützt. Diese Erstsicherung kann je nach Erfordernissen aus schweren Felsankern, Stahlstützbögen und/oder Stahlmatten bestehen. Ebenso zum Einsatz kommt Spritzbeton. Der endgültige Ausbau der gebohrten Tunnelröhre wird zu einem späteren Zeitpunkt hinter der Maschine eingebracht und folgt der Tunnelbohrmaschine.<ref>''[https://www.herrenknecht.com/de/produkte/kernprodukte/tunnelling/einfachschild-tbm.html Einfachschild-TBM.]'' In: ''Herrenknecht'', aufgerufen am 5. Mai 2015.</ref> |
Der Bohrkopf ist mit dem Antrieb am vorderen Ende der Vorschubeinrichtung, wie im Fachjargon ''Kelly'' genannt wird, angeschlagen (die ''kelly'' war beim [[Bohrturm|Erdölbohren]] ein an der abgesenkten Bohrwelle oben befestigtes Rohrstück mit polygonalem Querschnitt (wie etwa ein überdimensionierter [[Innensechskant]]schlüssel) dessen Führung und Drehbewegung ein Drehtisch mit ebendieser polygonalen Öffnung übernahm, das Rohr konnte mit steigender Bohrtiefe in der Führung des Bohrtisches abgesenkt werden). Die Vorschubeinrichtung besteht aus einem inneren Teil, an dem der Bohrkopf befestigt ist, der Innenkelly, und einem äußeren Teil, der sogenannten Außenkelly. Die Außenkelly der Maschine wird mittels der Verspannung in der gebohrten Tunnelröhre fixiert. Die Innenkelly mit dem am vorderen Ende angeschlagenen Bohrkopf gleitet während des Bohrvorganges parallel zur Bohrrichtung in der Außenkelly in Bohrrichtung nach vorne. Innenkelly und Außenkelly sind über die Vorschubzylinder miteinander verbunden. Die Vorschubzylinder schieben die Innenkelly mitsamt dem Bohrkopf nach vorne. Der Bohrkopf der Maschine ist mit Schneidrollen versehen, die mit Hartmetallringen bestückt sind und Diskenschneidrollen genannt werden. Der Drehantrieb des Bohrkopfes wird entweder mit Hydraulikmotoren oder Elektromotoren ausgestattet, wobei die elektrische Antriebsvariante heutzutage die gebräuchlichere geworden ist. Stufenlose Regelung der Drehzahl des Bohrkopfes ist bei modernen Tunnelbohrmaschinen mittlerweile ein Standard geworden. Um den Bohrkopf der Maschine herum ist ein Stahlschild angeordnet, der Bohrkopfmantel, der einerseits eine Stützfunktion für die gebohrte Tunnelröhre übernimmt und andererseits als Kopfschutz gegenüber eventuell herabfallenden Gesteins dient. Das abgebohrte Gestein wird über Förderbänder abtransportiert und für den Transport aus dem Tunnel entweder in Waggons geladen oder per Förderband aus dem Tunnel transportiert. Die gebohrte Tunnelröhre wird unmittelbar nach dem Bohrvorgang bei Bedarf mit der sogenannten Erstsicherung abgestützt. Diese Erstsicherung kann je nach Erfordernissen aus schweren Felsankern, Stahlstützbögen und/oder Stahlmatten bestehen. Ebenso zum Einsatz kommt Spritzbeton. Der endgültige Ausbau der gebohrten Tunnelröhre wird zu einem späteren Zeitpunkt hinter der Maschine eingebracht und folgt der Tunnelbohrmaschine.<ref>''[https://www.herrenknecht.com/de/produkte/kernprodukte/tunnelling/einfachschild-tbm.html Einfachschild-TBM.]'' In: ''Herrenknecht'', aufgerufen am 5. Mai 2015.</ref> |
||
Es gibt weltweit nur wenige Firmen, die diese Maschinen herstellen. In Deutschland sind es die Firmen [[Herrenknecht|Herrenknecht AG]] aus [[Schwanau]] und [[Aker Solutions#Beteiligung in Deutschland|Aker Solutions]] (ehem. Aker Wirth GmbH) aus [[Erkelenz]]. Die [[Robbins Company]] in den USA, [[Mitsubishi]], [[IHI]], [[Kawasaki Heavy Industries|Kawasaki]] und [[Hitachi Zosen]] in Japan sind weitere Hersteller. |
Es gibt weltweit nur wenige Firmen, die diese Maschinen herstellen. In Deutschland sind es die Firmen [[Herrenknecht|Herrenknecht AG]] aus [[Schwanau]] und [[Aker Solutions#Beteiligung in Deutschland|Aker Solutions]] (ehem. Aker Wirth GmbH) aus [[Erkelenz]]. Die [[Robbins Company]] in den USA, [[Mitsubishi]], [[IHI]], [[Kawasaki Heavy Industries|Kawasaki]] und [[Hitachi Zosen]] in Japan sind weitere Hersteller. NFM Technologies SA in Frankreich baute mit Lizenzen von MHI ([[Mitsubishi Heavy Industries]]) und später SHMG (Shenyang Heavy Machinery Group). Der ehemalige kanadische Hersteller Lovat wurde 2008 von [[Caterpillar]] aufgekauft und 2013 stillgelegt. |
||
Der Weltmarkt für Geräte des maschinellen Tunnelbaus wird von Herrenknecht auf etwa 1,5 Milliarden Euro beziffert, wovon das Unternehmen nach eigenen Angaben etwa 1,1 Milliarden Euro abdeckt (Stand: 2014).<ref name="sz-2014-01-20">{{Literatur |Autor=Max Hägler |Titel=„Der Deutsche hat wirklich vor allem Angst“ |Sammelwerk=[[Süddeutsche Zeitung]] |Band= |Nummer= |Datum=2014-01-20 |Seiten=16}}</ref> |
Der Weltmarkt für Geräte des maschinellen Tunnelbaus wird von Herrenknecht auf etwa 1,5 Milliarden Euro beziffert, wovon das Unternehmen nach eigenen Angaben etwa 1,1 Milliarden Euro abdeckt (Stand: 2014).<ref name="sz-2014-01-20">{{Literatur |Autor=Max Hägler |Titel=„Der Deutsche hat wirklich vor allem Angst“ |Sammelwerk=[[Süddeutsche Zeitung]] |Band= |Nummer= |Datum=2014-01-20 |Seiten=16}}</ref> |
||
Mit [[Ultraschallbohrer]]n (''„ultrasonic drilling“'') ist ein schnellerer Vortrieb als mit Fräsbohrern möglich.<ref>{{Webarchiv|url=https://www.im-halloffame.com/exploration-ray-roussy/ |wayback=20170112091827 |text=International Mining Technology Hall of Fame}}</ref> Der |
Mit [[Ultraschallbohrer]]n (''„ultrasonic drilling“'') ist ein schnellerer Vortrieb als mit Fräsbohrern möglich.<ref>{{Webarchiv|url=https://www.im-halloffame.com/exploration-ray-roussy/ |wayback=20170112091827 |text=International Mining Technology Hall of Fame}}</ref> Der BADGER (Tunnelbauroboter) ist ein von der EU gefördertes Forschungsprojekt<ref>[https://www.badger-robotics.eu/content/what-badger-project What is the BADGER project?]</ref> zur Schaffung eines autonom arbeitenden Erdbohr[[roboter]]s der die Tunnelwände als Beton-[[3D-Drucker]] produziert.<ref>[https://all3dp.com/robot-badger-drill-3d-print-tunnels/ Robot BADGER Can Drill Underground and 3D Print Tunnels]</ref> BADGER ist ein [[Apronym]] für „ro'''B'''ot for '''A'''utonomous un'''D'''er'''G'''round trenchless op'''ER'''ations, mapping and navigation“<ref>{{Internetquelle |autor=European Comission |url=https://cordis.europa.eu/project/id/731968 |titel=RoBot for Autonomous unDerGround trenchless opERations, mapping and navigation |werk=cordis.europa.eu |hrsg=European Comission |datum=18 August 2022 |sprache=en |abruf=2022-10-31}}</ref>. |
||
== Einsätze von Tunnelvortriebsmaschinen (Auswahl) == |
|||
== Bekannte Projekte == |
|||
[[Datei:TBM City-Tunnel Leipzig - S326.jpg|mini|Tunnelvortriebsmaschine beim Auffahren des [[City-Tunnel Leipzig|City-Tunnels Leipzig]] (2007)]] |
|||
Im Folgenden eine Auflistung von Tunnelprojekten, die mit Tunnelbohrmaschinen realisiert wurden oder noch im Bau sind: |
|||
[[Datei:Bohrkopf.jpg|mini|12-Meter-Bohrkopf ([[Pfändertunnel]]-Weströhre; 2008)]] |
|||
[[Datei:TBM S-210 Alptransit Faido East.jpg|mini|Kopf der S-210, die die östliche Röhre des Gotthard-Basistunnels zwischen Bodio und Faido bohrte (Schneidrollen bereits entfernt; 2006)]] |
|||
[[Datei:SAS 6842 (6172980957).jpg|mini|Tunnelbohrmaschine bricht durch (Bau der Second Avenue Subway; New York 2011)]] |
|||
Im Folgenden eine Auswahl von Tunnelprojekten, die mit Tunnelvortriebsmaschinen realisiert wurden oder noch im Bau sind: |
|||
=== Deutschland === |
=== Deutschland === |
||
Zeile 124: | Zeile 173: | ||
* [[Zimmerberg-Basistunnel]] (Eisenbahntunnel, Zürich. 1. Etappe) |
* [[Zimmerberg-Basistunnel]] (Eisenbahntunnel, Zürich. 1. Etappe) |
||
=== |
=== Weitere === |
||
* Canal de [[Navarra]] (Spanien) |
* Canal de [[Navarra]] (Spanien) |
||
* [[Citytunnel Malmö]] (Bahnverbindung in Malmö, Schweden) |
* [[Citytunnel Malmö]] (Bahnverbindung in Malmö, Schweden) |
||
Zeile 130: | Zeile 179: | ||
* [[Großer Belt]]-Bahntunnel (Dänemark) |
* [[Großer Belt]]-Bahntunnel (Dänemark) |
||
* [[Hallandsåstunnel]] (Eisenbahnlinie Göteborg–Lund, Schweden) |
* [[Hallandsåstunnel]] (Eisenbahnlinie Göteborg–Lund, Schweden) |
||
* [[Niagara Tunnel Project]] („Big Becky“, |
* [[Niagara Tunnel Project]] („Big Becky“, TVM mit 14,4 m Durchmesser; Durchbruch Mai 2011; Fertigstellung Sommer 2013)<ref>''[http://www.niagarafrontier.com/tunneltechnical.html Niagara Tunnel Project. Technical Facts.]'' Von: ''[[Ontario Power Generation]]'' und ''[[Strabag]]'', aufgerufen am 5. Mai 2015.</ref> |
||
* [[Westerscheldetunnel]] (Niederlande) |
* [[Westerscheldetunnel]] (Niederlande) |
||
* [[Hsuehshan-Tunnel]] (Taiwan National Highway No. 5) |
* [[Hsuehshan-Tunnel]] (Taiwan National Highway No. 5) |
||
* [[Crossrail]] (Bahnverbindung in London) |
* [[Crossrail]] (Bahnverbindung in London) |
||
== Liste der größten |
== Liste der größten Tunnelvortriebsmaschinen == |
||
{| class="wikitable sortable" |
{| class="wikitable sortable" |
||
|- |
|- |
||
Zeile 342: | Zeile 391: | ||
== Weblinks == |
== Weblinks == |
||
{{Commonscat|Tunnel boring machines| |
{{Commonscat|Tunnel boring machines|Tunnelvortriebsmaschinen}} |
||
{{Wiktionary}} |
{{Wiktionary}} |
||
* [http://www.citytunnelleipzig.info/tunnelbohrmaschine.php Erläuterungen zur |
* [http://www.citytunnelleipzig.info/tunnelbohrmaschine.php Erläuterungen zur TVM am Beispiel City-Tunnel Leipzig] |
||
* [http://www.citytunnelleipzig.info/tuebbingring.php Einbau Blindtübbingring am Beispiel City-Tunnel Leipzig] |
* [http://www.citytunnelleipzig.info/tuebbingring.php Einbau Blindtübbingring am Beispiel City-Tunnel Leipzig] |
||
* Video: [https://www.bauforum24.tv/herrenknecht-s568-einfachschild-tunnelbohrmaschine-449 Funktionsweise einer Einfachschild-Tunnelbohrmaschine.] In: ''bauforum24.tv'', 2011, 3:44 Min. |
* Video: [https://www.bauforum24.tv/herrenknecht-s568-einfachschild-tunnelbohrmaschine-449 Funktionsweise einer Einfachschild-Tunnelbohrmaschine.] In: ''bauforum24.tv'', 2011, 3:44 Min. |
||
Zeile 353: | Zeile 402: | ||
== Anmerkungen == |
== Anmerkungen == |
||
<references group="ANM"> |
<references group="ANM"> |
||
<ref group="ANM" name="Anm. KlBBL.">Mit dem Begriff ''Standfestigkeit'' wird die Fähigkeit von Gesteinsschichten beschrieben, einen bestimmten Zeitraum um einen nicht unterstützten unterirdischen Hohlraum ohne Zerstörung stehen zubleiben. (Quelle: Walter Bischoff, Heinz Bramann, Westfälische Berggewerkschaftskasse Bochum: ''Das kleine Bergbaulexikon.'')</ref> |
|||
</references> |
</references> |
||
{{Normdaten|TYP=s|GND=4186442-6}} |
{{Normdaten|TYP=s|GND=4186442-6}} |
||
[[Kategorie:Baumaschine]] |
[[Kategorie:Baumaschine]] |
||
[[Kategorie:Bohrmaschine]] |
[[Kategorie:Bohrmaschine]] |
Version vom 30. April 2024, 20:07 Uhr

Tunnelvortriebsmaschinen (kurz TVM) kommen beim Bau von Tunneln bzw. Stollen zum Einsatz, insbesondere dem Bau von Straßen- und Bahntunneln. Der Tunnelvortieb oder kurz Vortrieb bezeichnet hierbei das Erweitern des Tunnels ausgehend von seinem vorderen Ende (sogenannte Orstbrust).
Verschiedene Arbeiten im Tunnelbau können mit einer TVM automatisiert werden. Insbesondere verfügt eine derartige Maschine über Vorrichtungen zum Abbau des im Wege befindlichen Materials (Gestein oder Erdreich). Eine weitere Herausforderung im Tunnelbau besteht oftmals darin, den neu geschaffenen Hohlraum unmittelbar gegen ein Eindringen des umgebenden Materials zu sichern. Als temporäre Abstützung verfügen viele TVM daher über einen Schild, auch Schildmantel genannt (siehe Schildvortrieb). Weiterhin kann auch der dauerhafte Ausbau des Tunnels mithilfe der TVM erfolgen.
Die Anforderungen an eine TVM können hierbei je nach Bauprojekt sehr verschieden sein. Insbesondere bestimmt die Art des umgebenden Materials, welche Abbauwerkzeuge geeignet sind und welche Abstützungs- und Ausbaumaßnahmen erforderlich werden. Dementsprechend wird eine TVM in der Regel für einen spezifischen Tunnel individuell angefertigt und vor Ort zusammengesetzt. Ein Transport am Stück ist aufgrund der Größe häufig nicht möglich.
Für das unterirdische Verlegen von Leitungen aller Art existieren weitere Arten von Vortriebsmaschinen und -techniken mit kleineren Querschnitten. Diese werden unter dem Begriff Rohrvortrieb zusammengefasst[1], siehe dort.
Arten von Tunnelvortriebsmaschinen
Entsprechend der unterschiedlichen Aufgaben und Anforderungen werden verschiedene Bauformen definiert. Hierbei werden im Wesentlichen die Tunnelbohrmaschine (TBM) und die Schildmaschine (SM) unterschieden[2].
- Tunnelbohrmaschinen verfügen über einen Bohrkopf am vorderen Ende. Sie werden in der Regel, aber nicht ausschließlich, im Festgestein eingesetzt[1]. Durch die hohe Standfestigkeit des Gebirges bei festem Gestein kann hierbei oftmals auf einen Schild verzichtet werden (offene TBM), dennoch gibt es auch TBM mit Schild.
- Schildmaschinen finden überwiegend im Lockergestein Anwendung und verfügen über einen Schild zur Stützung des umgebenden Materials. Beim Abbau unterscheidet man vollflächig (SM-V), mittels eines rotierenden Schneidrads, und teilflächig (SM-T), mittels Bagger oder Fräse, siehe den Unterabschnitt Abbau.
Die Schildmaschinen werden außerdem dahingehend unterschieden, ob und mit welchem Verfahren zusätzlich zur späteren Außenwand auch die Ortsbrust des Tunnels gestützt wird. Dies erfolgt beispielsweise mechanisch oder mittels Flüssigkeits- oder Druckluftstützung.
Tunnelvortriebsmaschinen TVM | |||||||||||||||||||||||||||
Tunnelbohrmaschinen TBM ![]() | Schildmaschinen SM | ||||||||||||||||||||||||||
Schildmaschinen mit Vollschnittabbau SM-V | Schildmaschinen mit teilflächigem Abbau SM-T ![]() | ||||||||||||||||||||||||||
Aufbau und Komponenten
Der Aufbau einer TVM basiert auf der zeitlichen und räumlichen Abfolge der einzelnen Arbeitsschritte im Tunnelbau. An der Spitze einer TVM (unmittelbar vor der Ortsbrust) befindet sich die Vorrichtung, mit welcher zunächst das im Wege befindliche Material abgebaut wird. Dahinter befindet sich, wenn vorhanden, der Schildmantel, welcher das umgebende Material temporär abstützt, sowie die Vorschubeinrichtung. Abschließend folgt der dauerhafte Ausbau mit den dafür vorgesehenen Vorrichtungen. Der Abtransport des abgebauten Materials erfolgt parallel durch den vorderen Teil hindurch. Im hinteren bereich (Nachläufer) der Maschine befinden sich Hilfs- und Versorgungseinrichtungen sowie Anlagen für Anlieferung und Abtransport. Im Folgenden werden die einzelnen Komponenten nach ihren Aufgaben unterteilt und erläutert.
Abbau

Am vorderen Ende einer TVM, unmittelbar an der Ortsbrust, wird das im Wege befindliche Material abgetragen und den Vorrichtungen zum Abtransport zugeführt. Je nach Beschaffenheit des Gebirges bzw. Baugrunds sind unterschiedliche Abbauverfahren und Werkzeuge geeignet. Man unterscheidet zwischen vollflächigem und teilflächigem Abbau.
Beim vollflächigen Abbau kommt eine rotierende Scheibe zum Einsatz, welche die Querschnittsfläche des Tunnels voll ausfüllt. Dieser sogenannte Werkzeug- oder Meißelträger ist mit den Abbauwerkzeugen bestückt, in der Regel Rollenmeißel (auch Schneidrollen oder Disken genannt) oder Schälmesser. Zusätzlich kommen sogenannte Räumer in Form abgeschrägter Bleche sowie weitere Trichterförmige Vorrichtungen zum Einsatz, um das Ausbruchsmaterial abzuführen. Dieser Aufbau wird im Festgestein insgesamt als Bohrkopf, im Lockergestein als Schneidrad bezeichnet[2]. Zum Tunnelvortrieb wird er mittels Elektromotoren in Rotation versetzt und mit hohem Druck gegen die Ortsbrust gepresst. Bei diesem Verfahren können nur runde Tunnelquerschnitte realisiert werden.
Beim teilflächigen Abbau kommen andere im Erd-und Bergbau zu diesem Zweck verwendete Geräte zum Einsatz. Dies sind insbesondere Teilschnittmaschinen oder Bagger, letztere beispielsweise mit einem Reißzahn als Anbaugerät.
Sicherung des Hohlraums
Eine wesentliche Aufgabe im Tunnelbau besteht darin, den Tunnelhohlraum offen zu halten und einen Einsturz oder das Eindringen von Grundwasser zu verhindern. Dies betrifft die Ortsbrust und die seitliche Außenfläche des Tunnelhohlraums, die sogenannte Ausbruchslaibung. Ein wichtiger zu berücksichtigender Parameter ist hierbei die Standfestigkeit bzw. Standzeit des umgebenden Materials. Sie beschreibt dessen Fähigkeit, einen bestimmten Zeitraum um einen nicht unterstützten Hohlraum ohne Zerstörung stehen zu bleiben[3].
Im fertigen Zustand des Tunnels wird die Ausbruchslaibung durch den Ausbau dauerhaft gesichert bzw. abgestützt. Während dem Bau des Tunnels ergibt sich jedoch im Bereich der Ortsbrust und unmittelbar dahinter ein Bereich ohne eine derartige Stützung. Bei Tunneln im Festgestein kann die Standfestigkeit ausreichend sein, um diesen Bereich ungestützt zu lassen. Dies ist der Einsatzbereich von Tunnelbohrmaschinen ohne Schild. Reicht die Standfestigkeit jedoch nicht aus oder tritt zu viel Grundwasser zu, so werden zusätzliche Abstützungsmaßnahmen erforderlich.
Schildmantel

Zur Stützung der Ausbruchslaibung kommt ein Schildmantel oder kurz Schild zum Einsatz. Es handelt sich dabei um eine röhrenartige Stahlkonstruktion, welche die Maschine nach außen hin abschließt. Im Schutze des Schildes findet dann der Ausbau statt, sodass am hinteren Ende des Schildes kein ungestützter Bereich mehr verbleibt. Der Radius des Bohrkopfes bzw. Schneidrads kann hierbei größer sein als der des Schildes (Überschnitt). Dies dient einer Verbesserung der Kurvenfahrt sowie einer Entspannung des umgebenden Materials, was auch zu einer geringeren Mantelreibung am Schild führt[2]. Als weiterentwickelte Bauform gibt es sogenannte Doppelschild- oder Teleskopschildmaschinen, bei denen zwei Schilde zum Einsatz kommen. Die Vorrichtungen für Vorschub und Ausbau liegen hierbei im inneren, hinteren Schildmantel, auf dem teleskopartig axial beweglich ein äußerer, vorderer, die Bohreinheit umschließender Schildmantel fahrbar ist. Dadurch kann eine hohe Vortriebsgeschwindigkeit erreicht werden[4].
Ortsbruststützung

Für eine zusätzliche Stützung der Ortsbrust gibt es verschiedene Möglichkeiten[2]:
- Flüssigkeitsstützung, beispielsweise mit Bentonit-Suspension
- Erddruckstützung, hierbei wird ein Brei aus abgebautem Boden als Stützmedium verwendet, siehe Flüssigboden
- Druckluftstützung
- Mechanische Stützung mittels Brustplatten (insbesondere beim teilflächigen Abbau)
Bei sogenannten Kombinationsschildmaschinen (KSM) kann das Verfahren der Ortsbruststützung gewechselt werden, um sich an unterschiedliche Baugrundverhältnisse entlang der Trasse anszupassen.
Verfestigung
In manchen Fällen werden bereits vor dem Abbau am Gestein oder Erdreich Maßnahmen durchgeführt, welche der Verfestigung dienen. Dadurch kann der notwendige Aufwand zur Abstützung während des Abuaus verringert werden. Mit Hilfe einer Schaumanlage, die mit Tensiden und Wasser unter Druck Schaum erzeugt, kann im weichen Untergrund die Ortsbrust derart verfestigt werden, dass Sandböden wie tonige Böden abgebohrt werden können. In schlammigem Boden kann die Umgebung mit Flüssigstickstoff vereist werden (Bodenvereisung). Im Festgestein wird bei sogenannten Erweiterungstunnelbohrmaschinen im Vorfeld zunächst ein Pilotstollen erstellt. Von diesem aus können Störzonen im Gestein ertüchtigt und so die Risiken bei der anschließenden Bohung des Haupttunnels minimiert werden[2].
Tunnelausbau

Der Ausbau des Tunnels erfolgt meist in Form einer Tunnelauskleidung mit vorgefertigten Segmenten, den Tübbings. Der Einbau der Tübbings kann mit einem Erektor genannten roboterähnlichen Gerät automatisch erfolgen. Dies geschieht im Schutze des hinteren Schildmantels, dem sogenannten Schildschwanz[6]. Die Maschine verfügt dann außerdem über weitere Transportvorrichtungen zur Zulieferung der Tübbings zum Erektor.
Bei Tunnelbohrmaschinen ohne Schild werden auch andere Verfahren des Tunnelausbaus eingesetzt, insbesondere die Spritzbetonbauweise[2].
Vorschub

Beim Vorschub wird die TVM in Richtung der Ortsbrust verschoben, sodass sie sich im Rahmen des Tunnelvortriebs immer unmittelbar vor dieser befindet. Die Vorschubeinrichtung drückt den Bohrkopf oder das Schneidrad gegen die Ortsbrust und bewegt die Maschine nach vorne. Dies geschieht mit Hydraulikzylindern. Als Widerlager für diese dient meist die Vorderkante des zuletzt eingebauten Tübbing-Rings. Alternativ können Maschinen ohne Schild auch direkt am Fels der seitlichen Tunnelwand abgestützt werden. Mittels sogenannter Gripper wird hierbei die Vorschubeinrichtung im Fels verankert, die entsprechende Bauform wird auch als Gripper-TBM bezeichnet.
Beim Auffahren des Tunnels ergeben sich also üblicherweise die die folgenden beiden Arbeitsschritte:
- Der Vortrieb, bei dem die Maschine nach vorne fährt und die Ortsbrust mit Druck abbaut.
- Der Ringbau, bei dem ein neuer Ring aus Tübbings eingebaut wird. Hierfür werden die jeweilgen Hydraulikzylinder eingefahren. Anschließend presst die Maschine den neuen Ring gegen den vorherigen fest und beginnt erneut mit dem Vortrieb.
Abtransport
Der Abtransport des abgebauten Materials wird auch als Schutterung bezeichnet[7]. Die hierfür geeigneten Vorrichtungen hängen ganz von der Art und Konsistenz des abgebauten Materials ab. Grundsätzlich werden die Förderarten Trockenförderung und Pump- oder Flüssigförderung unterschieden. Letztere erfolgt über Förderleitungen und kommt insbesondere bei Flüssigkeits- oder Erddruckgestützer Ortsbrust zum Einsatz. Bei der Trockenförderung werden Förderbänder, Erdtransporter oder gleisgebundene Systeme (Schutterzüge) eingesetzt[1]. Weiterhin kann innerhalb der TVM ein Brecher eingesetzt werden, um zu große Gesteinsbrocken, beispielsweise Findlinge im Lockergestein, auf ein transportierbares Maß zu zerkleinern[8].
Hilfs- und Versorgungseinrichtungen
Zusätzlich zu den genannten Hauptkomponenten verfügt eine TVM über weitere unterstützende Anlagen. Dies sind beispielsweise:
- Versorgungseinheiten für Strom und Druckluft für den laufenden Betrieb, Wasser zum Kühlen der Meißel und zur Bindung von Staub, sowie Bewetterung
- Kräne und Transporteinrichtungen für die Anlieferung, insbesondere betreffend die Tübbings oder andere zum Ausbau verwendete Materialien
- Bewegungsräume und Wartungswege für Material und Personal, beispielsweise zum Austausch der Werkzeuge am Bohrkopf oder Schneidrad
Einmalverwendung oder Wiederverwendung
TVM hinterlassen in der Regel einen teilausgebauten Tunnel mit einem kleineren Querschnitt als der Ausbruchdurchmesser und der Schilddurchmesser der Maschine. Das liegt an Tübbings, vorstehenden Felsbohrankern, Tunnelauskleidung und Einbauten wie Fahrbahn, Entwässerungs- und Entlüftungsrohren. Das bedingt, dass eine TVM nur in einer Richtung fortschreiten und nicht zurückgefahren werden kann. Einen gewissen Spielraum zum Zurückziehen des Schilds muss sich der Betreiber deshalb für das allfällige Versagen einzelner Teile oder das Verstopfen mit Gesteinsbrocken bewahren, um bestimmte Teile austauschen oder Brocken zerlegen zu können. Der materielle und zeitliche Aufwand für Reparaturen ist wegen der räumlich beengten Zugänglichkeit und der Beschaffung von Ersatz hoch.
Werden Tunnel nur von einer Seite aufgefahren, liegt die Maschine bei Tunneldurchbruch wieder an oder nahe der Oberfläche und könnte, sofern die Größe Transporte zulässt, zum nächsten Einsatzort verbracht werden. Wird die Maschine – mehr oder weniger in Teile zerlegt – umgedreht und ein Stück versetzt, kann sie zum Bau einer zweiten, parallelen Röhre dienen.
Auf dem Landweg – Straße oder Schiene – können große TVM nur zerlegt transportiert werden. Auch der Schild muss dafür zerlegbar ausgeführt sein. Zwar existieren Schiffe mit ausreichend großvolumigem Laderaum, doch nur in seltenen Fällen ist es möglich, eine TVM auf dem Wasserweg direkt zum Einsatzort zu bringen.
Wenn, was typisch für lange Tunnel ist, von zwei Seiten oder sogar noch mehr Stellen angefahren wird, kommt es zwangsläufig dazu, dass eine TVM im Berg zerlegt werden muss. Das kann mit der Absicht geschehen, mit diesen und eventuell neuen Teilen rasch wieder eine funktionierende Maschine zusammenzubauen. Besteht kein absehbarer Bedarf für eine Maschine dieses Typs, werden wenige Teile erhaltend zur Wiederverwendung abgebaut und der Maschinenrahmen zerlegt und verschrottet.
In der Liste der größten Tunnelvortriebsmaschinen (unten) finden sich Beispiele für den Wiedereinsatz von TVM über große geografische Distanz hinweg: Niederlande–China, Deutschland–Russland.
Herstellerfirmen und Geschichte
1844 trug sich der schottische Bauingenieur und Erfinder William Brunton (* 26. Mai 1777 in Dalkeith; † 5. Oktober 1851 in Neath (Wales)) mit der Idee, zum Bau eines Tunnels zwischen England und Frankreich einen Hammer durch Druckluft zum Stoßen und Bohren anzutreiben. Die erforderlichen Kompressoren waren zu diesem Zeitpunkt allerdings nicht entwickelt. Seine Maschine glich einem riesigen Bohrer mit dem Durchmesser des Tunnels, der das Gestein zermalmen und die Bruchstücke in den entstandenen Bohrschacht zum Abtransport abwerfen sollte.[9]
Mit dem stoßenden Bohren nach dem Patent von Fowler aus dem Jahre 1849 fing das maschinelle Bohren 1857 an, die Einführung der mit Druckluft betriebenen Stoßbohrmaschinen verkürzte die Bauzeit für den Mont-Cenis-Eisenbahntunnel von geschätzten 40 bis 50 Jahren auf 14 Jahre.[10]
Bei Stoßbohrmaschinen sind Kolben und Bohrstange durch ein Keilschloss verbunden. Bei einer Schlagzahl von 250 bis 300 Stößen pro Minute arbeiten sie mit Hüben von 50 bis 250 mm und können bei Gesamtgewichten bis 280 kg nur auf Spannschlitten mit Handkurbel-Schraubenspindelvorschub an einer Spannsäule oder auf dem Dreibock arbeiten.
Um 1870 gab es erste Versuche, eine Tunnelvortriebsmaschine zum schnelleren Vortrieb beim Bau des Hoosac-Tunnels an der Ostküste (Boston) der USA einzusetzen und gleichzeitig das Verletzungsrisiko der Arbeiter – durch Arbeit mit Hammer und Meißel sowie Sprengungen mit Schwarzpulver (erst später kamen Vorläufer des Presslufthammers und Nitroglycerin erstmals hier zum Einsatz) – zu verringern. Bei der Pressevorführung vor Ort war nach rund 15 Zentimetern Schluss: Sie blieb stecken. Die Schneidmeißel aus Gusseisen erwiesen sich als zu weich und die Dampfmaschine zum Antrieb als zu schwach.
1897 entwickelte J. G. Leyner aus Denver die Hammerbohrmaschine. Sie arbeitete nach dem schlagenden Prinzip mit Luftspülung, wobei der Kolben mit nur 1/10 des Gewichtes mit 1500 Schlägen pro Minute auf das Bohrereinsteckende schlägt und eine Drallspindel mit Sperrklinken beim Rückgang des Kolbens über die Bohrerhülse den Bohrer um 12 bis 45 Grad je Schlag umsetzt. Auch diese Geräte wurden zunächst wie die Stoßbohrmaschinen an Spannsäulen oder Dreiböcken mit Spannschlitten und Handvorschub eingesetzt. Sie erreichten nach 1918 bei allerdings höherem Luftverbrauch bereits die 10- bis 13‑fache Leistung der Stoßbohrmaschinen.
Die Weiterentwicklung dieser Hammerbohrmaschinen führte mit dem Ersatz des Drallgetriebeumsetzens 1955 zum Druck- und schließlich zum Hydraulikmotorantrieb mit einem konstanten hohen Drehmoment.
Die weitere Entwicklung nach den Ideen von Brunton im Tunnel- und Stollenbau, die vor allem im U‑Bahn‑Bau bei geeigneten Bodenverhältnissen eine zunehmende Anwendung findet, ist durch den Einsatz von Tunnel- oder Stollenvortriebsmaschinen für Durchmesser bis zu 10,5 Metern gekennzeichnet. Der Gedanke wurde in den 1960er Jahren wieder aufgegriffen und zunächst nur im Bergbau und dann bei unterirdischen Verlagerungen eingesetzt. Stollen- und Tunnel-Vortriebsmaschinen stellen den unterirdischen Hohlraum ohne den absatzweisen Arbeitszyklus Bohren, Sprengen, Laden und Fördern kontinuierlich her, indem sie durch Werkzeuge, die für das anstehende Gebirge geeignet sind, zerspanend bis 11,7 kN/cm² mit Warzenmeißeln oder Schneidrollen bis 21,6 kN/cm² die Brust angreifen und das abgebaute Material hinter sich kontinuierlich abgeben. Sie werden in den USA seit 1950 in den verschiedensten Formen gebaut. Die Vorteile liegen in einer Vermeidung der Auflockerung durch den Wegfall der Sprengung, einer Verringerung des Überprofils und einem geringeren Personalbedarf. Nachteile sind die hohen Investitionskosten und die laufenden Kosten des Werkzeugverschleißes. Bekannt geworden sind die Alkirk-Lawrence-Pilotankermaschinen und die Oil-Shaleminer, die einen Pilotanker vorweg treiben, an dem sich der Bohrkopf gegen die Brust zieht. Seit Anfang der 1960er Jahre werden Maschinen von Robbins Company eingesetzt, bei denen das durch die Schneiden des Fräskopfes abgesplitterte Bohrklein von Bechern oder Baggereimern hochgenommen und am Scheitel auf das Austragsband geschüttet wird. Englische und japanische Entwicklungen von Schildvortriebsmaschinen arbeiten innerhalb eines sich auf den Ausbau abstützenden Vortriebsschildes, mit einem großen, die ganze Brust erfassenden Fräskopf bzw. bei Mitsubishi Heavy Industries mit vier gegenläufigen Fräsköpfen. In Deutschland waren es die Maschinen von den Firmen Demag, Wirth und Atlas Copco und die Schildvortriebsmaschinen von Bade-Holzmann, die in den 1960er Jahren die neuen Wege im Tunnel- und Stollenbau gebahnt haben. Es sind inzwischen in der Bundesrepublik Deutschland auch für den Bau von Schrägstollen, zum Bau von senkrechten Schächten und zur stufenweisen Erweiterung der Querschnitte bis auf 11 m geeignete vollmechanische Vortriebsmaschinen entwickelt worden. Bei Gesteinsfestigkeiten von 20 kN/cm² werden Warzen-, Zahn- und Disken-Cuttern eingesetzt.
Seit 1966 werden Vollschnittmaschinen mit Gewichten von 48 bis 90 t und Längen von 11,5 bis 21 Metern für Profile von 2 bis 6,4 m Durchmesser eingesetzt. Ihre Antriebsleistungen betragen – abhängig von Material und Durchmesser – 240 bis 950 kW, ihre Bohrkopf-Drehzahlen 5 bis 12,7 Umdrehungen pro Minute und der Anpressdruck bis zu 8000 kN.
Der Aufbau der Vortriebsmaschinen lässt folgende Bauteile erkennen:
- den mit 8 bis 10, 18 bis 23 und 18 bis 33 Rollenmeißeln bestückten Bohrkopf,
- den Staubschild mit Gummidichtung hinter dem Bohrkopf,
- Räumer und Schaufeln, die das Bohrgut, über eine Rutsche dem unter der Maschine eingebauten Einkettenkratzförderer oder einem Mulden-Gummiband zuleiten, der es am Ende einem ansteigenden Ladebund übergibt,
- zwei bis vier Elektromotoren, die über Gelenkwellen, Getriebe und Kupplungen den Antrieb vermitteln,
- ein Hydrauliksystem zum Verspannen, Vordrücken, und Abstützen.
Die Maschine wird in der Tunnelröhre mittels Pratzen durch eine vordere und hintere Verspannung mit mindestens 130 N/cm² gehalten. Der Anpressdruck des Bohrkopfes beträgt 1600 kN bei 2 m bis 6400 kN bei 6 m Durchmesser. Die Tunnelvortriebsmaschinen werden von einem Steuerstand im Schlepptender gesteuert; sie sind kurvenfahrbar mit 80 m Radius bei 2,4 m und 150 m Radius bei 6 m Durchmesser; ein Laser dient der Steuerkontrolle. Das erste Gerät wurde 1966 zum Auffahren eines 2800 m langen Abwasserstollens in Grünsandstein von 2,1 m Durchmesser in Dortmund eingesetzt; das 6‑Meter‑Gerät kam 1973 am Niederrhein zum Einsatz.[11]
Die vierte Röhre des Hamburger Elbtunnels wurde in den Jahren von 1997 bis 2000 mit der 2000 Tonnen schweren Schildvortriebsmaschine TRUDE mit einem Außendurchmesser von 14,20 m gebaut. Die zu diesem Zeitpunkt größte Tunnelvortriebsmaschine der Welt erweiterte mit 111 Schälmessern für weiches Gestein und 31 Rollenmeißeln für Hartgestein den Tunnel durchschnittlich um 6 m/Tag. Das Schneidrad mit der „Mixschildtechnik“ war von der Firma Herrenknecht aus Schwanau entwickelt worden. Kennzeichnend waren die fünf erstmals von innen begehbaren Speichen zum Auswechseln der Schneidwerkzeuge und einen unabhängig steuerbaren Zentrumsschneider.[12]
In der Schweiz wurden in den 1960er Jahren zunächst kleinere Profile mit Vortriebsmaschinen hergestellt. Ab 1970 wurden auch Großtunnel des Straßen- und Schienenverkehrs mit Tunnelvortriebsmaschinen aufgefahren. Bis Ende der 1990er Jahre wurden 19 große Straßen- oder doppelspurige Eisenbahntunnel mit einer Gesamtlänge von 83 km mit TVM aufgefahren.[13] Der Gotthard-Basistunnel wurde in den Jahren von 2002 bis 2010 mit den 400 m langen und 2700 t schweren Gripper-Tunnelbohrmaschinen Heidi (S‑211) und Sissi (S‑210) der Firma Herrenknecht AG geschaffen.[14] Die Bohrköpfe der Maschinen hatten einen Durchmesser von rund 9,5 m und waren mit mehr als 60 Rollenmeißeln versehen. Sie wurden von zehn Motoren mit jeweils 350 kW angetrieben.
Der Bohrkopf ist mit dem Antrieb am vorderen Ende der Vorschubeinrichtung, wie im Fachjargon Kelly genannt wird, angeschlagen (die kelly war beim Erdölbohren ein an der abgesenkten Bohrwelle oben befestigtes Rohrstück mit polygonalem Querschnitt (wie etwa ein überdimensionierter Innensechskantschlüssel) dessen Führung und Drehbewegung ein Drehtisch mit ebendieser polygonalen Öffnung übernahm, das Rohr konnte mit steigender Bohrtiefe in der Führung des Bohrtisches abgesenkt werden). Die Vorschubeinrichtung besteht aus einem inneren Teil, an dem der Bohrkopf befestigt ist, der Innenkelly, und einem äußeren Teil, der sogenannten Außenkelly. Die Außenkelly der Maschine wird mittels der Verspannung in der gebohrten Tunnelröhre fixiert. Die Innenkelly mit dem am vorderen Ende angeschlagenen Bohrkopf gleitet während des Bohrvorganges parallel zur Bohrrichtung in der Außenkelly in Bohrrichtung nach vorne. Innenkelly und Außenkelly sind über die Vorschubzylinder miteinander verbunden. Die Vorschubzylinder schieben die Innenkelly mitsamt dem Bohrkopf nach vorne. Der Bohrkopf der Maschine ist mit Schneidrollen versehen, die mit Hartmetallringen bestückt sind und Diskenschneidrollen genannt werden. Der Drehantrieb des Bohrkopfes wird entweder mit Hydraulikmotoren oder Elektromotoren ausgestattet, wobei die elektrische Antriebsvariante heutzutage die gebräuchlichere geworden ist. Stufenlose Regelung der Drehzahl des Bohrkopfes ist bei modernen Tunnelbohrmaschinen mittlerweile ein Standard geworden. Um den Bohrkopf der Maschine herum ist ein Stahlschild angeordnet, der Bohrkopfmantel, der einerseits eine Stützfunktion für die gebohrte Tunnelröhre übernimmt und andererseits als Kopfschutz gegenüber eventuell herabfallenden Gesteins dient. Das abgebohrte Gestein wird über Förderbänder abtransportiert und für den Transport aus dem Tunnel entweder in Waggons geladen oder per Förderband aus dem Tunnel transportiert. Die gebohrte Tunnelröhre wird unmittelbar nach dem Bohrvorgang bei Bedarf mit der sogenannten Erstsicherung abgestützt. Diese Erstsicherung kann je nach Erfordernissen aus schweren Felsankern, Stahlstützbögen und/oder Stahlmatten bestehen. Ebenso zum Einsatz kommt Spritzbeton. Der endgültige Ausbau der gebohrten Tunnelröhre wird zu einem späteren Zeitpunkt hinter der Maschine eingebracht und folgt der Tunnelbohrmaschine.[15]
Es gibt weltweit nur wenige Firmen, die diese Maschinen herstellen. In Deutschland sind es die Firmen Herrenknecht AG aus Schwanau und Aker Solutions (ehem. Aker Wirth GmbH) aus Erkelenz. Die Robbins Company in den USA, Mitsubishi, IHI, Kawasaki und Hitachi Zosen in Japan sind weitere Hersteller. NFM Technologies SA in Frankreich baute mit Lizenzen von MHI (Mitsubishi Heavy Industries) und später SHMG (Shenyang Heavy Machinery Group). Der ehemalige kanadische Hersteller Lovat wurde 2008 von Caterpillar aufgekauft und 2013 stillgelegt.
Der Weltmarkt für Geräte des maschinellen Tunnelbaus wird von Herrenknecht auf etwa 1,5 Milliarden Euro beziffert, wovon das Unternehmen nach eigenen Angaben etwa 1,1 Milliarden Euro abdeckt (Stand: 2014).[16]
Mit Ultraschallbohrern („ultrasonic drilling“) ist ein schnellerer Vortrieb als mit Fräsbohrern möglich.[17] Der BADGER (Tunnelbauroboter) ist ein von der EU gefördertes Forschungsprojekt[18] zur Schaffung eines autonom arbeitenden Erdbohrroboters der die Tunnelwände als Beton-3D-Drucker produziert.[19] BADGER ist ein Apronym für „roBot for Autonomous unDerGround trenchless opERations, mapping and navigation“[20].
Einsätze von Tunnelvortriebsmaschinen (Auswahl)
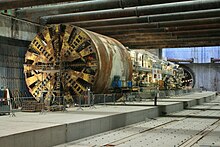
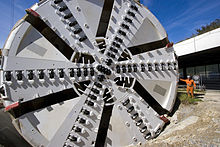


Im Folgenden eine Auswahl von Tunnelprojekten, die mit Tunnelvortriebsmaschinen realisiert wurden oder noch im Bau sind:
Deutschland
- Albvorlandtunnel (Neubaustrecke Wendlingen–Ulm)
- Boßlertunnel (Neubaustrecke Wendlingen–Ulm)
- City-Tunnel Leipzig (Stammstreckentunnel für die S-Bahn Mitteldeutschland, Leipzig)
- Fildertunnel (Bahnprojekt Stuttgart 21)
- Finnetunnel (Neubaustrecke Erfurt–Leipzig/Halle)
- Kaiser-Wilhelm-Tunnel (zweite Tunnelröhre zwischen Ediger-Eller und Cochem)
- Katzenbergtunnel (Eisenbahnverbindung Karlsruhe–Basel)
- Kombilösung (Karlsruhe) (U‑Straßenbahn Karlsruhe)
- Neuer Schlüchterner Tunnel (zweite Tunnelröhre unter dem Distelrasen bei Schlüchtern)
- Nord-Süd-Stadtbahn (Köln)
- TRUDE (Autobahn A7, vierte Elbtunnelröhre, Hamburg)
- Tunnel Nord-Süd-Fernbahn (Tiergartentunnel, Berlin)
- Tunnel Rastatt (Neubau- /Ausbaustrecke Karlsruhe-Basel)
- U-Bahn-Linie 5 (Berlin) (Verlängerung zwischen Alexanderplatz und Brandenburger Tor, Berlin)
- VERA (U-Bahn-Linie 4, Hamburg)
- Bauabschnitt 40 des Abwasserkanals Emscher (zwei parallele, zehn Kilometer lange Tunnelröhren zwischen Bottrop und Oberhausen)
Österreich
- Brennerbasistunnel (Teile der Zulaufstrecke Nord)
- Koralmtunnel (Abschnitt der Koralmbahn)
- Pfändertunnel (Weströhre)
- Semmering-Basistunnel (Abschnitt Fröschnitzgraben)
- Wienerwaldtunnel (Eisenbahnverbindung)
Schweiz
- Neue Eisenbahn-Alpentransversale (NEAT):
- Vereinatunnel (Meterspur-Eisenbahntunnel mit Y‑Teilung)
- Weinbergtunnel (Eisenbahntunnel, Zürich)
- Zimmerberg-Basistunnel (Eisenbahntunnel, Zürich. 1. Etappe)
Weitere
- Canal de Navarra (Spanien)
- Citytunnel Malmö (Bahnverbindung in Malmö, Schweden)
- Eurotunnel (Eisenbahnverbindung England–Frankreich)
- Großer Belt-Bahntunnel (Dänemark)
- Hallandsåstunnel (Eisenbahnlinie Göteborg–Lund, Schweden)
- Niagara Tunnel Project („Big Becky“, TVM mit 14,4 m Durchmesser; Durchbruch Mai 2011; Fertigstellung Sommer 2013)[21]
- Westerscheldetunnel (Niederlande)
- Hsuehshan-Tunnel (Taiwan National Highway No. 5)
- Crossrail (Bahnverbindung in London)
Liste der größten Tunnelvortriebsmaschinen
Nr. | Jahr | Land | Tunnel | Hersteller / Technik | Durchmesser (m)[22] |
---|---|---|---|---|---|
1 | 2015 | Hong Kong | Autobahntunnel Tuen Mun–Chek Lap Kok | Herrenknecht Mixschild | 17,60[23] |
2 | 2011 | USA | Ersatztunnel für das Alaskan Way Viaduct, Seattle | Hitachi Zosen EPB-Schild | 17,48 |
3 | 2016 | Italien | Santa-Lucia-Tunnel (A1) | Herrenknecht EPB-Schild | 15,87 |
4 | 2015 | China | Jangtsekiang-Tunnel der Wuhan Metro | Herrenknecht Mixschild (2×) | 15,76 |
5 | 2011 | Italien | Sparvo-Tunnel (A1) | Herrenknecht EPB-Schild | 15,55 |
6 | 2011 | China | Shanghai West Jangtsekiang-Tunnel[24] | Herrenknecht Mixschild, ex Nr. 8 | 15,43 |
7 | 2010 | China | Qianjiang-Tunnel, Hangzhou | Herrenknecht Mixschild, ex Nr. 8 | 15,43 |
8 | 2006 | China | Shanghai Changjiang Daqiao | Herrenknecht Mixschild (2×) | 15,43 |
9 | 2005 | Spanien | Madrid Calle 30 Autobahntunnel | Herrenknecht | 15,20 |
Mitsubishi | 15,00 | ||||
10 | 2013 | Italien | Caltanissetta-Tunnel, Sizilien (SS 640) | NFM Technologies | 15,08 |
11 | 2011 | China | Weisan-Straßentunnel, Nanjing | IHI/Mitsubishi/CCCC Slurry-TBMs (2×) | 14,93 |
12 | 2012 | China | Hongmei-Straßentunnel, Shanghai | Herrenknecht Mixschild | 14,93 |
13 | 2008 | China | Jangtsekiang-Tunnel Nanjing | Herrenknecht Mixschild (2×) | 14,93 |
14 | 2013 | China | ? | Herrenknecht Mixschild, ex Nr. 13 | 14,93 |
15 | 2006 | China | Jungong-Straßentunnel, Shanghai | NFM Technologies, ex Nr. 17 | 14,87 |
16 | 2004 | China | Shangzhong-Straßentunnel, Shanghai | NFM Technologies, ex Nr. 17 | 14,87 |
17 | 2000 | Niederlande | Groene Harttunnel (Eisenbahn) | NFM Technologies | 14,87 |
18 | 2006 | Kanada | Niagara Tunnel Project | Robbins Hartgestein-Gripper-TBM | 14,40 |
19 | 2013 | Neuseeland | Waterview Connection, Auckland | Herrenknecht EPB-Schild | 14,41 |
20 | 2004 | Russland | Silberwald-Autobahntunnel, Moskau | Herrenknecht Mixschild, ex Nr. 22 | 14,20 |
21 | 2001 | Russland | Lefortowoer Tunnel, Moskau | Herrenknecht Mixschild, ex Nr. 22 | 14,20 |
22 | 1997 | Deutschland | 4. Röhre des Neuen Elbtunnels | Herrenknecht Mixschild (TRUDE) | 14,20 |
23 | 2009 | China | Yingbinsan-Straßentunnel, Shanghai | Mitsubishi EPB-Schild, ex Nr. 24 | 14,27 |
24 | 2007 | China | Bund-Tunnel, Shanghai | Mitsubishi EPB-Schild | 14,27 |
25 | 2004 | Japan | Namboku-Linie der Tokyo Metro | IHI EPB-Schild | 14,18[25] |
26 | 1994 | Japan | Tōkyō-wan-Aqua-Line (Trans Tokyo Bay) | 8 TBM: 3 Kawasaki, 3 Mitsubishi, 1 Hitachi, 1 IHI | 14,14 |
27 | 2010 | Spanien | Autobahn SE-40, Sevilla | NFM Technologies (2×) | 14,00 |
Siehe auch
Weblinks
- Erläuterungen zur TVM am Beispiel City-Tunnel Leipzig
- Einbau Blindtübbingring am Beispiel City-Tunnel Leipzig
- Video: Funktionsweise einer Einfachschild-Tunnelbohrmaschine. In: bauforum24.tv, 2011, 3:44 Min.
Einzelnachweise
- ↑ a b c Ulrich Maidl, Bernhard Maidl: Maschineller Tunnelbau mit Tunnelvortriebsmaschinen und Rohrvortrieb. In: Handbuch für Bauingenieure: Technik, Organisation und Wirtschaftlichkeit (= Handbuch für Bauingenieure). Springer Fachmedien, Wiesbaden 2020, ISBN 978-3-658-21749-5, S. 1–74, doi:10.1007/978-3-658-21749-5_32-4.
- ↑ a b c d e f Empfehlung zur Auswahl von Tunnelvortriebsmaschinen, Deutscher Ausschuss für unterirdisches Bauen (DAUB), 2010 (Abgerufen am 23. Januar 2024)
- ↑ Walter Bischoff, Heinz Bramann: Das kleine Bergbaulexikon. Verlag Glückauf, Essen 1998, ISBN 978-3-7739-0501-7.
- ↑ Doppelschild-TBM – Kontinuierlicher Vortrieb mit Höchstgeschwindigkeit. Webpräsenz der Herrenknecht AG, abgerufen am 14. September 2018
- ↑ Hallandsåstunnel - Herrenknecht AG. Abgerufen am 9. März 2024.
- ↑ Tunnelbohrmaschinen für Hartgestein. ( vom 12. Februar 2013 im Webarchiv archive.today) In: Aker Wirth GmbH, aufgerufen am 5. Mai 2015.
- ↑ Walter Zanoskar: Abförderung der Felsmassen. Schutterarbeit, Schutterung. In: Stollen- und Tunnelbau. Springer Vienna, Vienna 1964, ISBN 978-3-7091-8117-1, S. 80–92, doi:10.1007/978-3-7091-8116-4_3.
- ↑ Mixschild - Herrenknecht AG. Abgerufen am 25. Februar 2024.
- ↑ Journal Über Land und Meer, Tunnel zwischen England und Frankreich, Deutsche Verlags-Anstalt, Berlin, 1881.
- ↑ Larry C. Hoffman: The ROCK DRILL and CIVILIZATION | Rock drilling is one of the world’s most ancient technologies—and a pre requisite for nearly all the others. In: Invention & Technology Magazine. Band 15, Nr. 1, 1999 (amerikanisches Englisch, archive.org).
- ↑ Georg Garbotz, Baumaschinen einst und jetzt, in: Baumaschine und Bautechnik, Frankfurt am Main, ISSN 0005-6693, 22. Jahrgang, Heft 5, 1975, S. 153 ff.
- ↑ TRUDE - Die größte Schildvortriebsmaschine der Welt. In: Museum der Arbeit, Hamburg, aufgerufen am 5. Mai 2015.
- ↑ Leonhard Schmid, Josef Elmiger: Wie begründet sich der hohe Anteil von Maschinenvortrieben in der Schweiz. In: Tunneltechnologie für die Zukunftsaufgaben in Europa. Balekma-Verlag, Rotterdam 1999, ISBN 90-5809-051-5, S. 59–71.
- ↑ Gotthard-Basistunnel. ( vom 23. Februar 2016 im Internet Archive) In: Herrenknecht, März 2011, aufgerufen am 5. Mai 2015.
- ↑ Einfachschild-TBM. In: Herrenknecht, aufgerufen am 5. Mai 2015.
- ↑ Max Hägler: „Der Deutsche hat wirklich vor allem Angst“. In: Süddeutsche Zeitung. 20. Januar 2014, S. 16.
- ↑ International Mining Technology Hall of Fame ( vom 12. Januar 2017 im Internet Archive)
- ↑ What is the BADGER project?
- ↑ Robot BADGER Can Drill Underground and 3D Print Tunnels
- ↑ European Comission: RoBot for Autonomous unDerGround trenchless opERations, mapping and navigation. In: cordis.europa.eu. European Comission, 18. August 2022, abgerufen am 31. Oktober 2022 (englisch).
- ↑ Niagara Tunnel Project. Technical Facts. Von: Ontario Power Generation und Strabag, aufgerufen am 5. Mai 2015.
- ↑ Tracking the world's mega-TBMs, TunnelTalk
- ↑ Chronik – Seit über 35 Jahren eine Erfolgsgeschichte herrenknecht.com, bis 2015, abgerufen 26. Februar 2023.
- ↑ XXL-Tunnelbohrmaschinen im Jangtse-DeltaXXL-Tunnelbohrmaschinen im Jangtse-Delta, 14. März 2014
- ↑ „Used a world's largest diameter 14.18 m double shield tunnel boring machine for the construction of the Tokyo Metro Namboku Line's Azabu section construction“
Anmerkungen